Burkert Type 1060 User Manual
Page 2
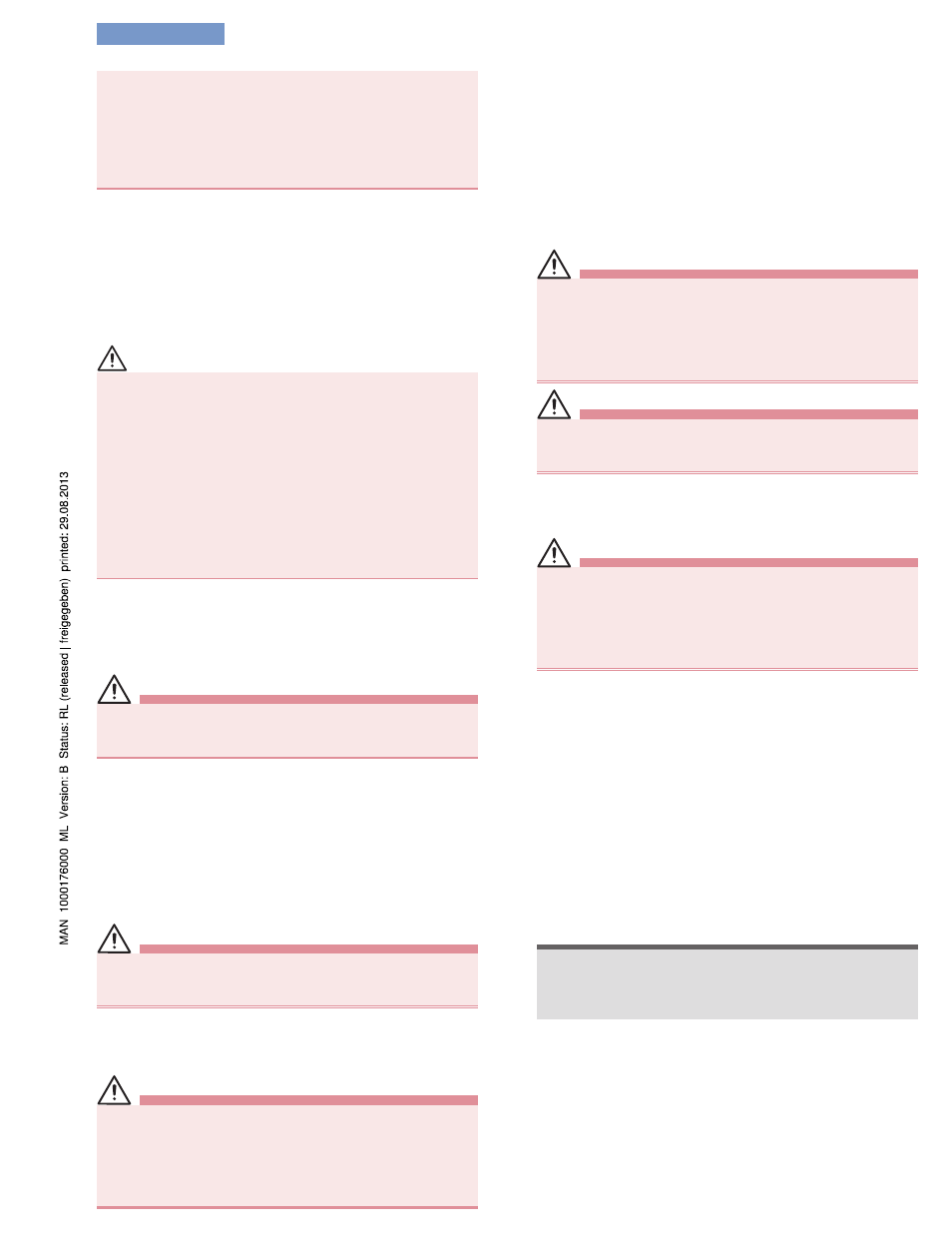
1.
OPERATING INSTRUCTIONS
The operating instructions contain important information.
• Read the instructions carefully and follow the safety instructions
in particular.
• Keep the instructions in a location where they are available to
every user.
• The liability and warranty for Type 1060 are void if the operating
instructions are not followed.
2.
INTENDED USE
Operate the electrical position feedback type 1060 only when in
perfect condition and pay attention to correct storage, transportation,
installation and operation.
3.
BASIC SAFETY INSTRUCTIONS
These safety instructions do not make allowance for any contin-
gencies and events which may arise during installation, operation
and maintenance.
WARNING!
Danger – high pressure!
• Before loosening lines or valves, turn off the pressure and vent
the lines.
To prevent injury, ensure the following:
• Do not use type 1060 in potentially explosive areas.
• Do not make any internal or external changes to type 1060.
Secure device from unintentional actuation.
• Only trained technicians may perform installation and mainte-
nance work.
• After an interruption in the power supply, ensure that the pro-
cess is restarted in a controlled manner.
• Observe the general regulations of technology.
4.
INSTALLATION AND START-UP
4.1. Actuator D-50 to F-80
Tasks before Installation
DANGER!
Risk of injury from high pressure!
• Before converting the devices, switch off the pressure and
vent the lines.
→
Interrupt the control air supply and flow of medium.
→
Screw transparent hood off the actuator cover.
→
Unscrew position indicator using Allen key (size 5).
→
Screw adapter
② instead of the transparent hood onto the
actuator (see Fig. 1).
→
Screw electr. position feedback
① into adapter ② (see Fig. 1).
4.2. Actuator G-100, H-125
Tasks before Installation
DANGER!
Risk of injury from high pressure!
• Before converting the devices, switch off the pressure and
vent the lines.
→
Interrupt the flow of medium.
→
Empty the valve housing.
→
Move actuator into upper piston position.
DANGER!
Control function B and I:
Risk of injury when unscrewing the transparent hood!
Transparent hood must not be under pressure when unscrewed.
• Before unscrewing the transparent hood, pressurize only
lower piston chamber with compressed air via lower control
air connection.
→
Screw transparent hood off the actuator cover.
→
Unscrew position indicator using Allen key (size 8).
→
Type 2030, 2031: Screw threaded bushing
③ (see Fig. 1)
onto the actuator spindle (size 14).
→
Then interrupt the control air supply.
→
Screw adapter
② instead of the transparent hood onto the
actuator (see Fig. 1).
→
Screw electr. position feedback
① into adapter ② (see Fig. 1).
4.3. Actuator K-175, L-225
Tasks before Installation
WARNING!
Risk of injury and malfunction caused by parts jumping out
or slipping!
The actuators contain pretensioned springs which can jump out
or slip if not opened properly.
• The actuators K-175 / L-225 may be opened by the manufac-
turer or responsible sales office only.
DANGER!
Risk of injury from high pressure!
• Before converting the devices, switch off the pressure and
vent the lines.
→
Interrupt the flow of medium.
→
Empty the valve housing.
→
Move actuator into upper piston position.
DANGER!
Control function A and I:
Risk of injury when unscrewing the transparent hood!
Transparent hood must not be under pressure when unscrewed.
• Before unscrewing the transparent hood, pressurize only
lower piston chamber with compressed air via lower control
air connection.
→
Screw transparent hood off the actuator cover.
→
Unscrew position indicator (yellow screw cap) by hand.
→
Screw spindle cover cap
④ (see Fig. 1) instead of the position
indicator onto the end of the spindle (size 14).
→
Then interrupt the control air supply.
4.4. Installation and start-up
→
Screw adapter
② instead of the transparent hood onto the
actuator (see Fig. 1).
→
Screw electr. position feedback
① into adapter ② (see Fig. 1).
5.
ELECTRICAL CONNECTION (for all actuators)
→
Loosen cylinder head screw
⑦ (see Fig. 2) on device socket
and remove socket.
NOTE!
Bent plug tabs will prevent the contact insert from being
reinstalled properly, thereby resulting in functional failure!
• Carefully remove the contact insert and make certain the plug
tabs are not bent.
→
Loosen screw in the contact insert
⑥, take out contact insert
(see Fig. 2).
→
Feed cable through union nut
⑨.
→
Connect according to the circuit (see Fig. 3).
→
Max. connected loads:
5 A
at 250 V AC
0.25 A at 250 V DC.
→
Insert contact insert
⑥ into cap ⑧ and screw on (see Fig. 2).
→
Screw on device socket with cylinder head screw
⑦, ensuring
that the flat seal is securely positioned
⑤ (see Fig. 2).
→
Check the valve for function and leaks.
Type 1060
english