Rietschle thomas gmbh + co. kg page – Elmo Rietschle R-WPB User Manual
Page 13
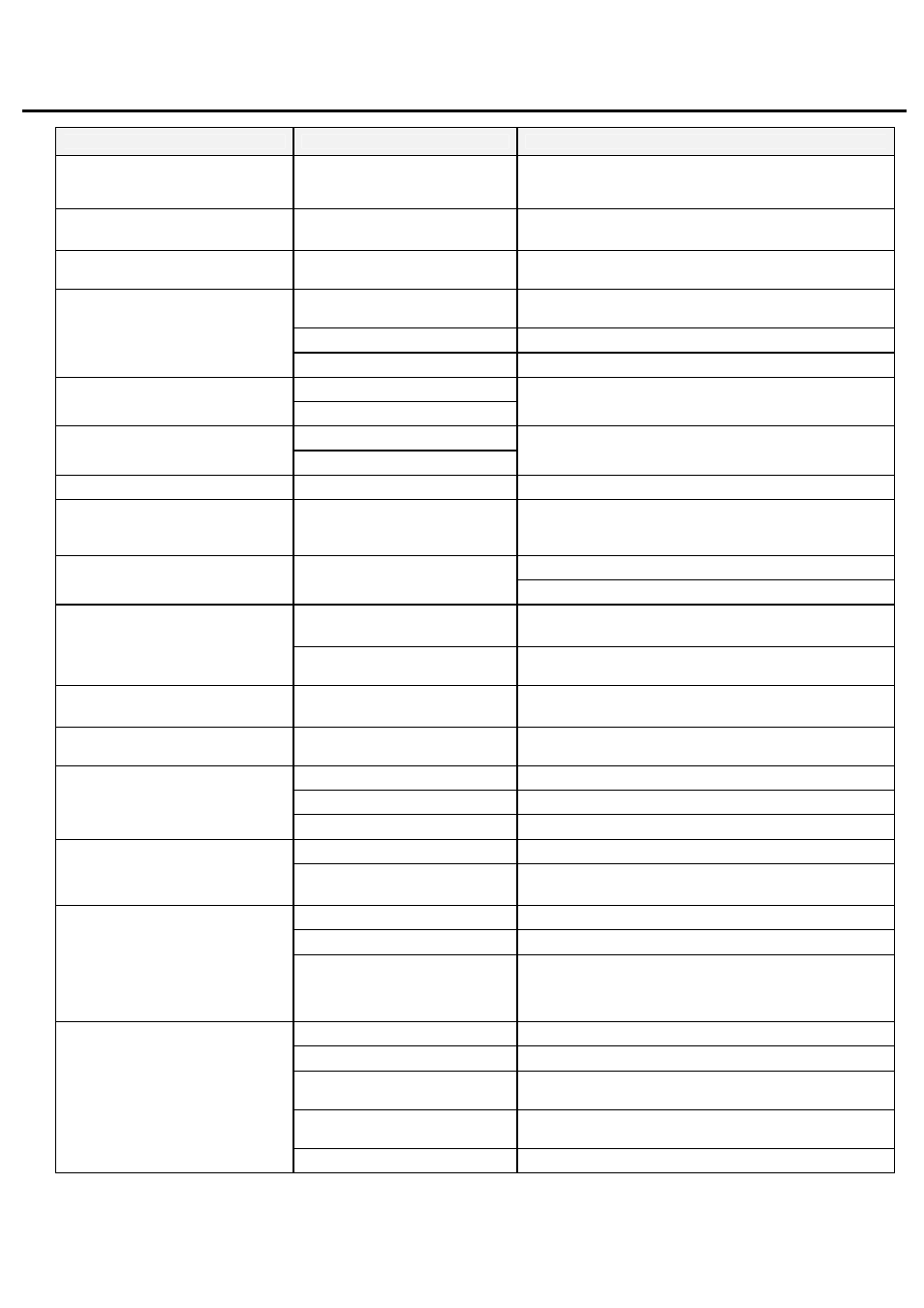
Rietschle Thomas GmbH + Co. KG
page
13
/
23
L
IST OF POSSIBLE FAILURES AND METHODS FOR REMOVING THEM
FAILURE
POSSIBLE CAUSE
REMOVAL
The machine will not start
Electrical part failure
Check the wiring, contactors, fuses, thermal or other protection, and
cable connection state. Check the state and functioning of the electric
motor.
Oil leaks through the ventilation openings
High oil level (measured when the
blower is turned off)
Drain excessive oil.
Elevated noise level, the blower makes a
“metallic” sound
Blower rotor knocking, bearing failure or
incorrect setting of the limit clearances
Repair by the Rietschle Thomas servicemen
Bearing failure or seizing of the rotors in
their working space
Repair by the Rietschle Thomas servicemen
High overpressure in the outlet pipeline
Measure the overpressure and remove the cause.
High current consumption
High vacuum
Replace the filter inserts.
No oil in the blower
High temperature of the cover at the blower
pulley
Bearing failure
Repair by the Rietschle Thomas servicemen
No oil in the blower
High temperature of the cover at the gear
Failure of the bearing or gear
Repair by the Rietschle Thomas servicemen
Slipping belt
Greasy belt
Clean both the belt and the pulleys and degrease them with petrol.
The blower is loaded immediately after
start-up (applies only to blower sets with
PVO valves)
Disengaged starting valve function
Set the combined safety and starting valve so that it will be open when
the machine is turned off.
Check the non-return valve and replace if necessary.
The blower turns spontaneously in the
opposite direction when being turned off
Malfunctioning non-return valve
Disassemble the pipeline and replace the sealing ring.
High overpressure in the outlet pipeline
Measure the overpressure in the outlet pipeline and remove the cause *)
The safety valve is set for maximum + 10% of the outlet overpressure.
The safety valve releases air when the
blower is in operation
Failure of the combined safety and
starting valve
Remove leakage and dirt from the control valve, and/or replace the
rubber bellows.
The safety valve sucks air when the blower
is in operation
High vacuum in the inlet pipeline
Measure the vacuum in the inlet pipeline and remove the cause *)
The safety valve is set for maximum + 10% of the vacuum.
The safety valve will not open when the full
blower load is exceeded
The safety valve is clogged with dirt
(applies to the Herose valves)
Disassemble and clean the valve.
Dirty filter insert
Replace the filter insert.
Overload Maintain
the load - data.
An overheated blower
Large piston clearances
Repair by Rietschle Thomas
Incorrectly installed non-return valve
Repair the installation.
No transport
Slipped or broken belt
Belt failure and/or incorrectly set pulleys
Blower failure
Incorrectly dimensioned blower
Compare the values with the efficiency table.
Leaky safety valve
Check the valve setting and operating pressure.
Low supplied volume
Slipping belt
Check visually the operation of the belt whether it runs without
vibrations. Check the motor power. Recheck the belt state. Set the lower
possible limit of the pendulous motor frame position lower by adjusting
the stop bolt.
The rotors touch each other
Check the bearings and gear setting.
Damaged bearings
Replace the bearings and change oil
Incorrectly aligned pulley and/or
coupling
Adjust it/them and tension the belt of the belt drive.
Loosened bolts securing the motor and/or
blower
Tighten and adjust them.
Vibration
Rotor imbalance due to dirt
Clean the transport space and rotors.
*) The cause might lie in a project error, for example. At a specific flow, the pipeline resistance is higher than the overpressure (required when the blower parameters
were being specified). This is usually detected when the blower is first turned on and/or when the projected machines are being put into operation. Another cause