Rietschle thomas gmbh + co. kg page – Elmo Rietschle R-WPB User Manual
Page 10
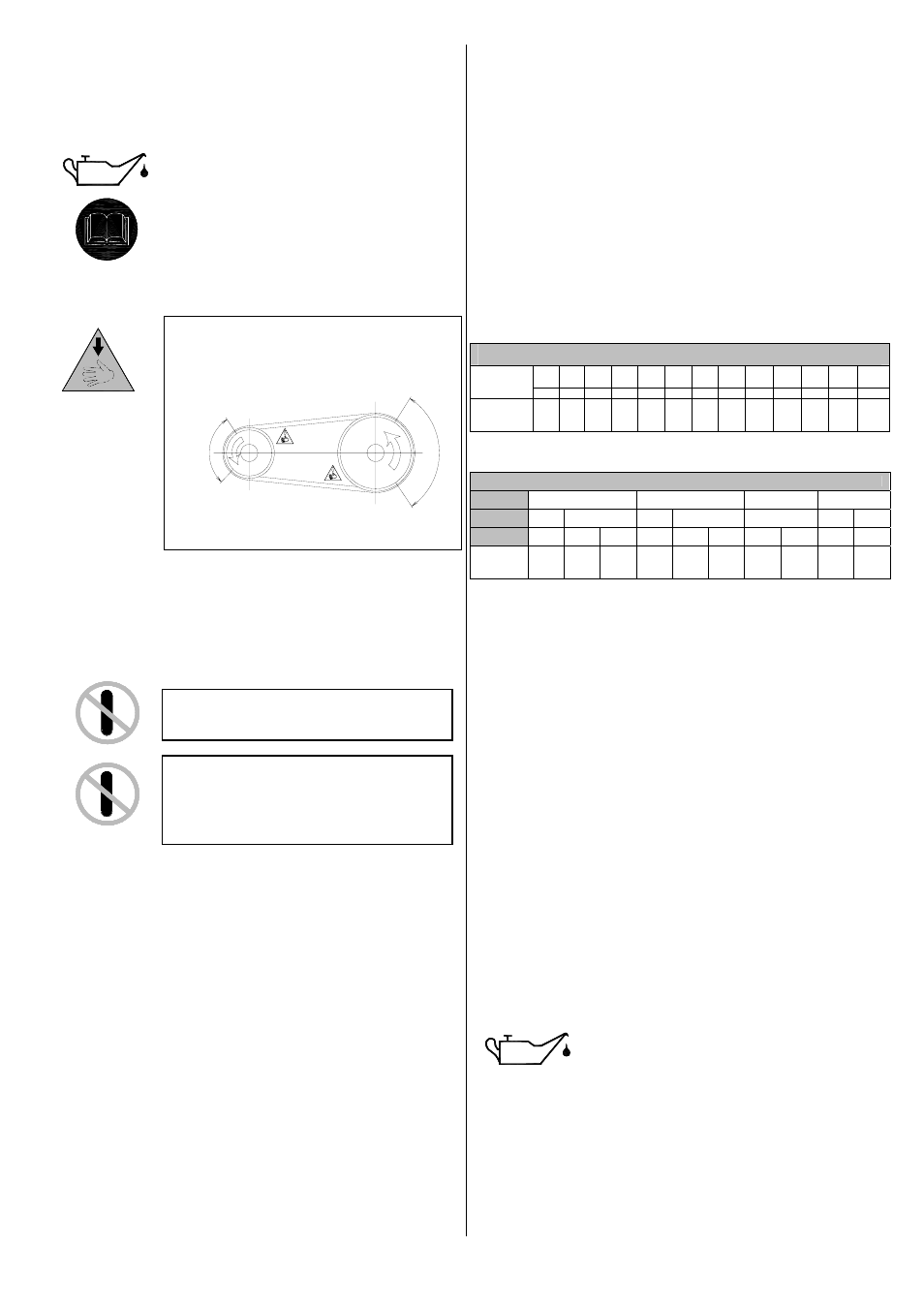
Rietschle Thomas GmbH + Co. KG
page
10
/
23
- Check all valves in the discharge pipeline whether they
are open.
Connecting elements
- Check whether all connecting elements are installed and
tight.
Filling with oil
Blowers are transported without oil. The approximate
volumes of oil charges and the recommend types of oil are
stated in Table 1 and Table 2 respectively (Chapter 4.5.4).
On no account should oils be mixed! See Chapter 5.5.1 for
more information.
Movement inspection
Check whether the blower moves smoothly (turn the pulley
slowly with your hand).
WARNING!
You might be hurt when turning the pulley. You
must hold the pulley at the places of contact with
the belt **).
Motor
Dmychadlo
*
*
*
*
Be careful you do not crush your fingers!
Pipeline Inspection
Check whether the suction and discharge sides are clear.
Inspection of the direction of rotation
Turn the blower on for no more than 1 second. If it were
turned on for a longer time and the direction of rotation
were incorrect, the blower could be damaged. The blower
drive must turn in the direction indicated by the arrows.
FORBIDDEN!
Backward running will damage the blower.
FORBIDDEN!
Do not turn the blower on again when it is still
running down. Otherwise, it could be seriously
damaged (the blower must be turned on only
when at a standstill).
Take care the following steps:
• Open the acoustic enclosures (if installed).
• Turn on the electric motor. Check the position of the
stop bolt (the pendulous motor frame must not hit the
bolt).
• Check the functioning and adjustment of the safety
valve when the machine is in operation.
• After approximately 1 minute, check the operating
pressure. When the specified pressure is reached, turn
off the drive unit.
• Observe the blower running down. The blower must
run down smoothly, without impacts and/or sudden
stop.
• Check whether the direction of fan rotation is correct -
air must flow from the opening above the top wall of
the noise-damping hood.
Safety valve functioning inspection
You should check the functioning of the safety valve and
the mobility of the sealing cone during operation, at a
pressure of 80% (or higher) of the opening pressure. If
HEROSE valves are used in smaller blower sets, it is
necessary to check the cone mobility. You must unload the
cone by loosening the knurled nut in the valve body cover.
You must turn the nut until it moves with difficulty, then
turn the nut a further approximately 180°. The cone will be
unloaded and the safety valve will start releasing air. Then
you must tighten the nut again. Larger blower sets are
equipped with safety valves with control valves. After one
end of the hose has been disconnected from the control
valve, the “bellows” space will open into the atmosphere
and the valve will open automatically. After re-connecting
the hose, you must check the joint for tightness (for
example, with soapy water).
• Check, monitor and document the operating pressure
and temperature;
• Monitor the noise level and vibrations when the blower
set is in operation;
• Check the temperature on the blower surface for local
overheating; and
• Check the state and volume of oil in the oil level gauges.
Table 3 – Maximum oscillation power of blowers
Type
Blower revolutions [1.min
-1
]
120 300 400
430
550
750
780
1000
1300 1600 2000 3300
4000
5500
6500
7000
8300
WPB/WVB
5000 6000 5600 5500 5250 5250 4600 3000 3500 3000 2600 2200 1850
Oscillation
power
[mm.s
-1
]
< 2
< 3
< 3
< 4
< 4
< 5
< 5
< 6
< 7
< 7
< 8
< 8
< 9
Note: The power of blower mechanical oscillation is in accordance with the ČSN ISO 3945 Standard.
Table 4 – Maximum oscillation power of electric motors
ELECTRIC MOTOR
Type
56 - 132
160 - 225
250 - 280
315 - 355
Category N
R
N R
N, R
N
R
No. of poles 2,4,6,8
4,6,8 2 2,4,6,8
4,6,8 2 4,6,8 2 2,4,6,8
2,4,6,8
Oscillation
power
[mm.s
-1
]
< 1.8
< 0.71 < 1.12
< 2.8
< 1.12
< 1.8
< 4.5
< 4.5
< 4.5
< 1.8
Note: The power of electric motors’ mechanical oscillation is in accordance with the ČSN ISO 35 0000
Standard, Part 14 (IEC 34-14), Category N – normal, Category R – reduced.
If the values stated in Tables 3 and 4 are exceeded, you must contact the RT service department!!!
- During the first two operating hours, a permanent
operator records values in a report every 15 minutes.
- During the next two operating hours, the permanent
operators record values in the operating diary every 30
minutes.
- During another eight operating hours, the permanent
operators hourly record values in the operating diary.
No emergency stopping controllers are normally delivered
with the RT compact units. The electric part supplier is
required to ensure their installation.
The blower has two separate oil charges.
Oil is filled through the filling holes in the tops of both
covers. After removing their caps, you can pour in oil. You
should use a funnel so that oil will not leak uncontrollably
into the surroundings, stain the belt drive, etc.
Oil is discharged through the drain holes in the cover
bottoms. Used oil must be drained into sufficiently large
tanks. After removing the drain hole cap, you must also
remove the filling hole cap so that oil can drain freely into
the tank and a vacuum cannot build up when oil is being
discharged. You must visually check the used oil whether it
does not contain metal particles or metal dust. The presence
of such substances might indicate the initial stage of
malfunction of either the bearings or the gear. In such
cases, you must contact the RT service department.
The blower can be refilled with oil only when all the
remaining oil has drained away and the drain hole cap is
closed.
5.3 T
RIAL
OPERATION
5.4
E
MERGENCY
STOPPING
CONTROLLERS
5.5 S
ETTING
AND
ADJUSTMENT
INSTRUCTIONS
5.5.1 F
ILLING AND
CHANGING THE OIL
5.3.1 C
HECK
INTERVALS FOR THE
TRIAL OPERATION
5.2 F
IRST
TURNING ON THE
BLOWER SET OR
BLOWER