Gorman-Rupp Pumps 810A2-4045T 1529947 and up User Manual
Page 29
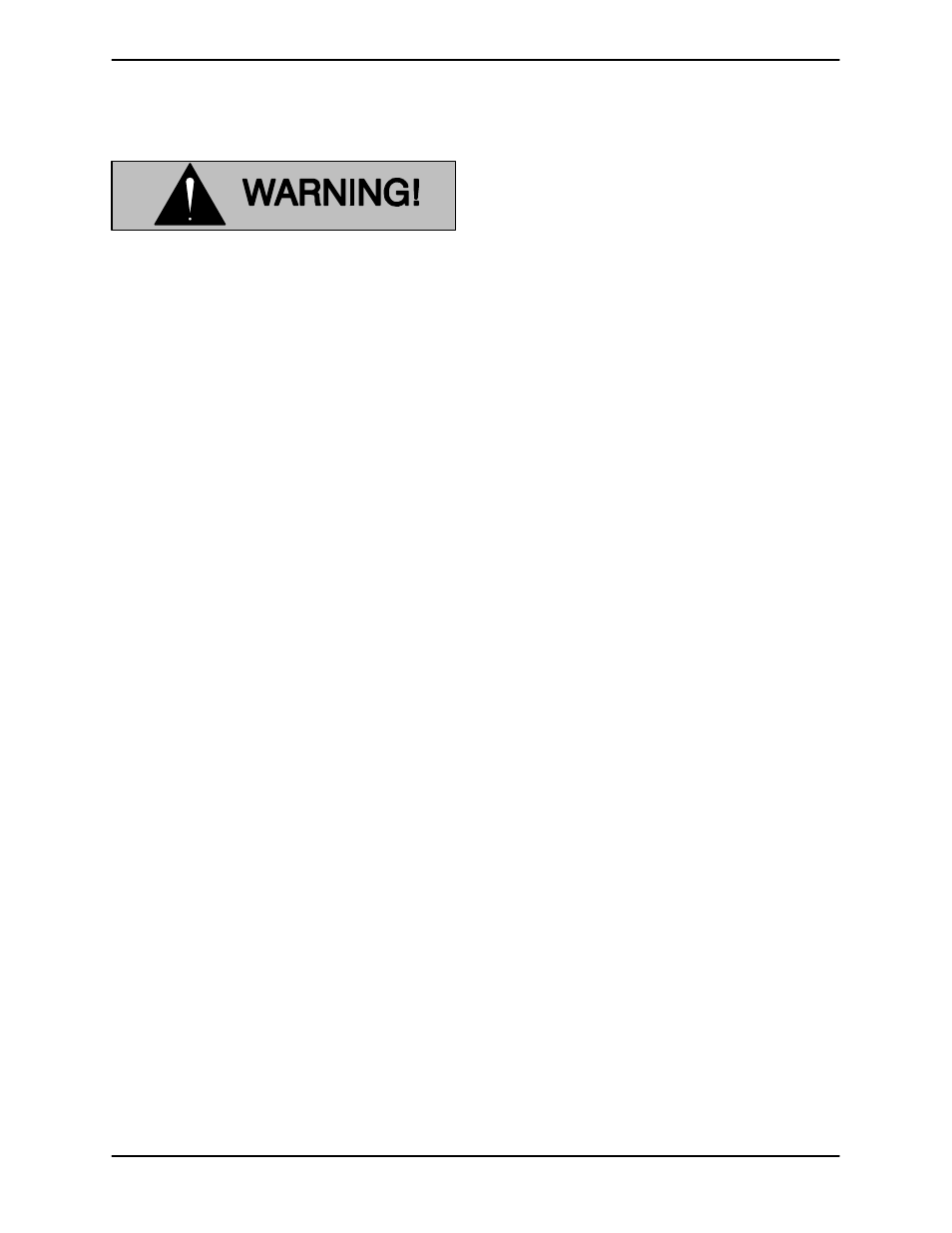
OM-06543
80 SERIES
MAINTENANCE & REPAIR
PAGE E - 9
must be separated from the base and intermedi
ate. Remove the hardware securing the pump cas
ing (1) to the base.
Do not attempt to lift the complete pump
unit using the lifting eye. It is designed
to facilitate removal or installation of in
dividual components only. Additional
weight may result in damage to the
pump or failure of the eye bolt.
Tie and tag any leveling shims used under the
pump casing mounting feet to ease reassembly.
Support the pump casing and intermediate using a
suitable hoist and sling. Remove the hardware (14)
and separate the pump casing and gasket set (12)
from the seal plate assembly (36) and the interme
diate (19). Replace the gasket set as required.
Inspect the wear plate (41) and replace if scored or
worn. To remove the wear plate, disengage the
hardware (43 and 44) from the wear plate studs
(42) and pull the wear plate from the pump casing.
Remove the wear plate O‐ring (40).
Impeller Removal
(Figure 3)
Before removing the impeller, turn the cross arm on
the automatic lubricating grease cup (15) clock
wise until it rests against the cover (see Figure 6 in
LUBRICATION). This will prevent the grease in the
cup from escaping when the impeller is removed.
Use an impeller wrench to remove the impeller. If
an impeller wrench is not available, place a block of
wood against one of the vanes and strike it sharply
with a hammer. Be careful not to damage the
vane. Unscrew the impeller in a counterclockwise
direction (when facing the impeller). Use caution
when removing the impeller; tension on the seal
spring will be released as the impeller is un
screwed.
Inspect the impeller and replace it if cracked or
badly worn. Slide the impeller adjusting shims (4)
off the shaft. For ease of reassembly, tie and tag the
shims or measure and record their thickness.
Seal Removal
(Figure 3)
Make certain that the cross arm on the grease cup
has been turned down against the cover before re
moving the seal assembly.
For ease of disassembly, the seal and seal plate as
sembly (36) may be removed as a single unit. Be
fore attempting to remove the seal plate, remove
the seal cavity grease cup and piping (15, 16 and
17).
Remove the outer rotating element. Slide the seal
plate, shaft sleeve and remaining seal parts off the
shaft as a unit.
Carefully remove the outer stationary seat, packing
ring, spring washer and seal spring from the seal
plate. Remove the spacer sleeve, inner spring
washer, packing ring, stationary seat and rotating
element. Use a stiff wire with a hooked end if nec
essary.
Inspect the seal liner (38) for wear or grooves that
could cause leakage or damage to the seal pack
ing rings. The seal liner is secured by a press fit into
the seal plate (37) and does not normally require
replacement. If replacement is required, see Seal
Installation.
If no further disassembly is required, refer to Seal
Installation.
Separating Intermediate And Drive Assembly
From Engine
(Figure 3)
If it is necessary to separate the intermediate and
drive assembly from the engine, support the inter
mediate using a suitable hoist and sling. Remove
the hardware (20 and 21) securing the intermedi
ate (19) and guards (61 and 62) to the engine bell
housing. Separate the assemblies by pulling
straight away from the engine.
It is not necessary to remove the drive plate assem
bly (26) from the engine flywheel unless replace