Gorman-Rupp Pumps 06C1-GAR 1289163 and up User Manual
Page 24
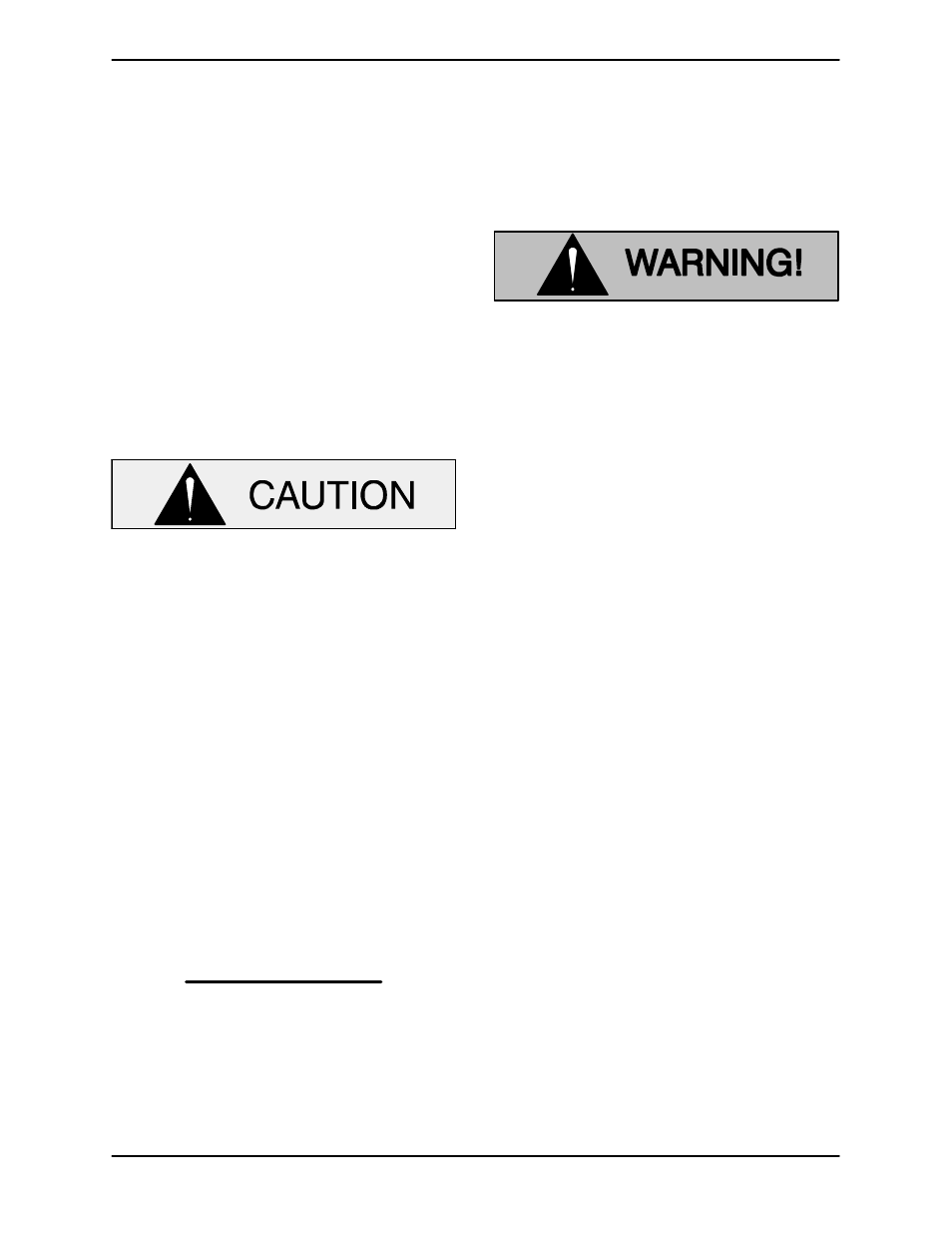
0 SERIES
OM--05688
MAINTENANCE & REPAIR
PAGE E -- 6
PUMP AND SEAL REASSEMBLY
If the gearbox requires disassembly, refer to
GEARBOX DISASSEMBLY and GEARBOX
REASSEMBLY, followed by PUMP AND SEAL
REASSEMBLY.
Pump Casing And Wear Ring Installation
If the wear ring (38) was removed for replacement,
press the replacement ring into the pump casing
(1) until it seats squarely against the shoulder bore.
The wear ring
must seat squarely in the
pump casing bore or binding and/or ex-
cessive wear will result.
Position the oil seal (33) in the casing bore with the
lip positioned as shown in Figure 1. Press the oil
seal into the bore until fully seated against the bore
shoulder.
Lubricate the O-ring (37) and install it in the groove
in the gearbox housing (32). Install the same thick-
ness of bearing adjusting shims (34) as previously
removed.
NOTE
Shaft endplay should be between .000 and .005
inch (0,0 and 0,127 mm). Add or remove bearing
shims to achieve correct endplay.
Install the gearbox housing gasket (5) over the cas-
ing studs (35). Carefully slide the pump casing
over the shaft until fully seated against the gearbox
housing.
Be careful not to damage the lip of the oil
seal on the shaft keyway.
Make sure the bearing
shims remain in position in the casing bore. Secure
the casing to the gearbox with the nuts (36).
Seal Reassembly and Installation
(Figures 1 and 2)
Clean the seal cavity and shaft with a cloth soaked
in fresh cleaning solvent.
Most cleaning solvents are toxic and
flammable. Use them only in a well-ven-
tilated area free from excessive heat,
sparks, and flame. Read and follow all
precautions printed on solvent contain-
ers.
The seal is not normally reused because wear pat-
terns on the finished faces cannot be realigned
during reassembly. This could result in premature
failure. If necessary to reuse an old seal in an emer-
gency, carefully wash all metallic parts in
fresh
cleaning solvent and allow to dry thoroughly.
Handle the seal parts with extreme care to prevent
damage. Be careful not to contaminate precision
finished faces; even fingerprints on the faces can
shorten seal life. If necessary, clean the faces with a
non-oil based solvent and a clean, lint-free tissue.
Wipe
lightly in a concentric pattern to avoid
scratching the faces.
Inspect the seal components for wear, scoring,
grooves, and other damage that might cause leak-
age. Clean and polish the pinion shaft, or replace it
if there are nicks or cuts on either end (see
GEAR-
BOX DISASSEMBLY). If any components are
worn, replace the complete seal;
never mix old
and new seal parts.
If a replacement seal is being used, remove it from
the container and inspect the precision finished
faces to ensure that they are free of any foreign
matter.
To ease installation of the seal, lubricate the sta-
tionary seat O-ring, bellows and pinion shaft with
water or a very
small amount of oil, and apply a
drop of light lubricating oil on the finished faces.
Assemble the seal as follows, (see Figure 2).