3 fault codes, troubleshooting – R&M Materials Handling VARIABLE SPEED CONTROLS CMXC 022 Service Manual User Manual
Page 9
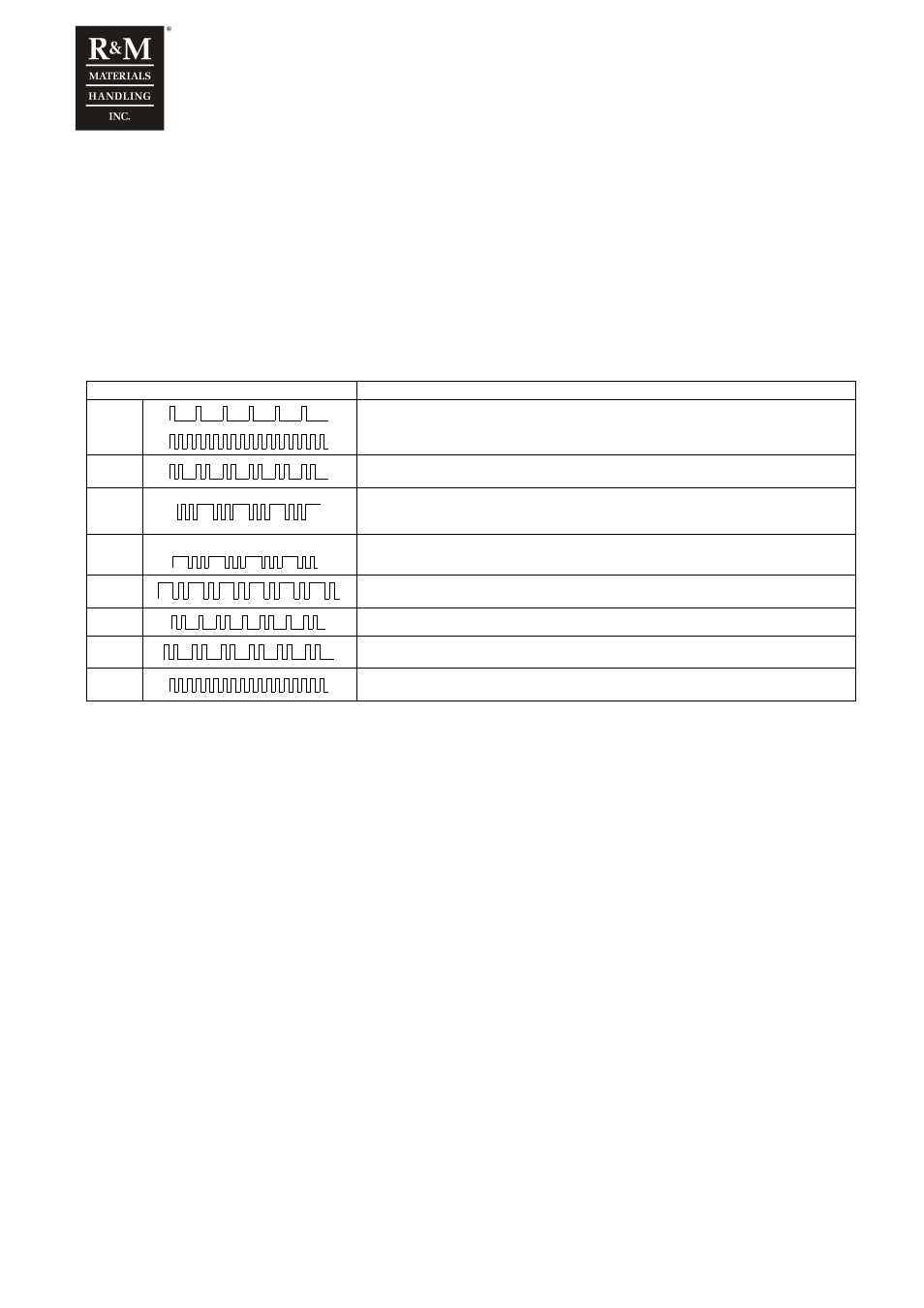
R&M Materials Handling, Inc.
4501 Gateway Boulevard
Springfield, Ohio 45502
P.: (937) 328-5100
FAX: (937) 325-5319
9/14
R&M Materials Handling, Inc. reserves the right to alter or amend the above information without notice.
3 FAULT CODES, TROUBLESHOOTING
There are high voltages inside the inverter (including the programming switches).
Wait for at least three minutes after the supply voltage has been switched off before
any service actions.
When the inverter detects a fault situation it stops running and starts signalling the fault code by blinking the
indication leds (green and red). The blinking of the code is carried on until a new fault occurs or until power is
switched off. The fault codes are explained in the table below.
Fault code, color
Fault. Possible cause. Checkings.
Green
Overvoltage. Mains voltage is too high or deceleration ramp time is too short. Check
the voltage of all supply phases at the terminal X2. If they are ok, set a longer ramp by
switch S3 (and S5-3).
Green
Stall supervision / overcurrent. Brake does not open properly or there is an obstackle
on the track. Check also the motor dependent parameters.
Green
Deceleration ramp supervision. Deceleration ramp has not been followed. If the fault
occurs again set longer ramp time by switch S3. Check also the setting of the motor
nominal current (switch S5).
Green
Motor overtemperature. Check the type and the loading of the motor. If there is no
sensor in the motor the inverter terminals X1:10-11 must be short circuited.
Green
Inverter overtemperature. Motor current is too high (bearing problem, obstacle on the
track, brake does not open properly,…) or the ambient temperature is too high.
Green
Undervoltage. Check the voltage of all supply phases at the terminal X2.
Red
Short circuit. Switch the power off. Check the insulation of the motor cables and the
motor windings.
Red
Microprosessor fault. Switch the power off for 10 seconds. Then power-up the
inverter.
The latest active fault is removed from the memory always when power is switched off.
If inverter is not in a fault state, but driving is not possible:
Motor will not start if dc-bus voltage too high (above 745V), this occurs if any of line-to-line voltages exceeds
480V+10% = 528V
If line voltage cannot be reduced, install drop-down transformer
Check the supply voltage phases at terminal X2.
Check the drive command signal at terminal X1.
Check the limit-switch signals at terminal X1.
Check that the control voltage level is correct. Rating plate is located on the left side of the inverter.
Check all parameters, especially the motor dependent parameters.
Check that the motor(s) corresponds the selected motor parameters.
Check that the brake opens and closes properly. Check the brake airgap if necessary.
Inverter starts and opens the brake, but motor does not rotate. Check motor current parameter.