Wide brightness range ccfl backlight controllers – Rainbow Electronics MAX1839 User Manual
Page 11
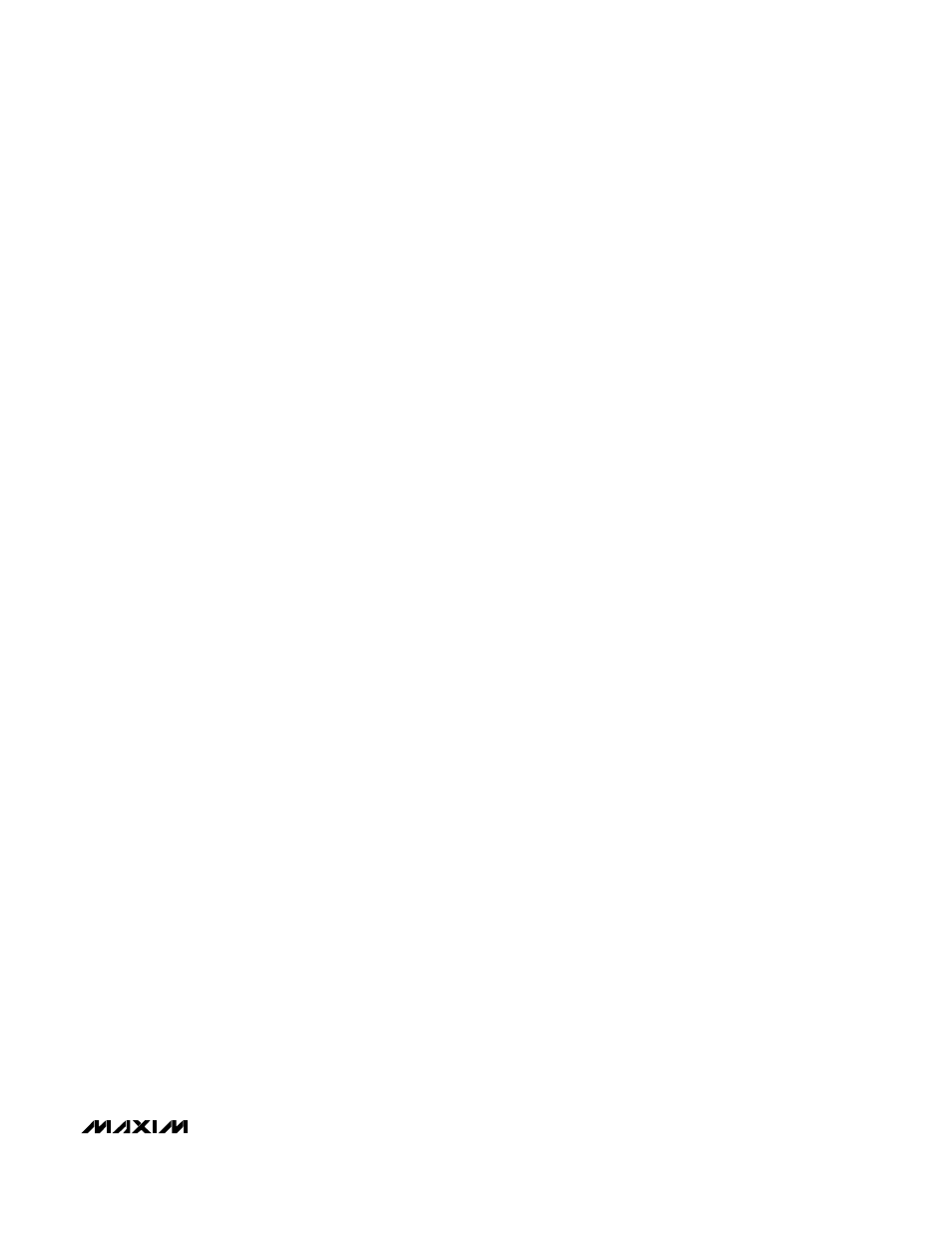
MAX1739/MAX1839
†
Wide Brightness Range
CCFL Backlight Controllers
_______________________________________________________________________________________
11
Voltage and Current Control Loops
The MAX1739/MAX1839 use two control loops. The cur-
rent control loop regulates the average lamp current. The
voltage control loop limits the maximum average primary-
side transformer voltage. The voltage control loop is
active during the beginning of DPWM on-cycles and in
some fault conditions. Limiting the transformer primary
voltage allows for a lower transformer secondary voltage
rating that can increase reliability and decrease cost of
the transformer. The voltage control loop acts to limit the
transformer voltage any time the current control loop
attempts to steer the transformer voltage above its limit as
set by V
CTFB
(see Sense Resistors).
The voltage control loop uses a transconductance
amplifier to create an error current based on the volt-
age between CTFB and the internal reference level
(600mV typ) (Figure 2). The error current is then used
to charge and discharge C
CCV
to create an error volt-
age V
CCV
. The current control loop produces a similar
signal based on the voltage between CSAV and its
internal reference level (see the Dimming Range sec-
tion). This error voltage is called V
CCI
. The lower of
V
CCV
and V
CCI
is used with the buck regulator’s PWM
ramp generator to set the buck regulator’s duty cycle.
During DPWM, the two control loops work together to
limit the transformer voltage and to allow wide dimming
range with good line rejection. During the DPWM off-
cycle, V
CCV
is set to 1.2V and CCI is set to high imped-
ance. V
CCV
is set to 1.2V to create soft-start at the
beginning of each DPWM on-cycle in order to avoid
overshoot on the transformer primary. V
CCI
is set to
high impedance to keep V
CCI
from changing during the
off-cycles. This allows the current control loop to regu-
late the average lamp current only during DPWM on-
cycles and not the overall average lamp current.
Upon power-up, V
CCI
slowly rises, increasing the duty
cycle, which provides soft-start. During this time, V
CCV
,
which is the faster control loop, is limited to 150mV
above V
CCI
by the CCV-CLAMP. Once the secondary
voltage reaches the strike voltage, the lamp current
begins to increase. When the lamp current reaches the
regulation point, V
CCI
reaches steady state. With MIN-
DAC = VL (DPWM disabled), the current control loop
remains in control and regulates the lamp current.
With MINDAC between REF and GND, DPWM is
enabled and the MAX1739/MAX1839 begin pulsing the
lamp current. During the on-cycle, V
CCV
is at 150mV
above V
CCI
. After the on-cycle, V
CCV
is forced down to
1.2V to provide soft-start at the beginning of the next
on-cycle. Also, V
CCI
retains its value until the beginning
of the next on-cycle. When V
CCV
increases, it causes
the buck regulator duty cycle to increase and provides
soft-start. When V
CCV
crosses over V
CCI
, the current
control loop regains control and regulates the lamp cur-
rent. V
CCV
is limited to 150mV above V
CCI
for the
remainder of the on-cycle.
In a lamp-out condition, V
CCI
increases the primary
voltage in an attempt to maintain lamp current regula-
tion. As V
CCI
rises, V
CCV
rises with it until the primary
voltage reaches its set limit point. At this point, V
CCV
stops rising and limits the primary voltage by limiting
the duty cycle. Because V
CCV
is limited to 150mV
above V
CCI
, the voltage control loop is quickly able to
limit the primary voltage. Without this clamping feature,
the transformer voltage would overshoot to dangerous
levels because V
CCV
would take more time to slew
down from its supply rail. Once the MAX1739/MAX1839
sense less than 1/6 the full-scale current through the
lamp for 2 seconds, it shuts down the Royer oscillator
(see Lamp-Out Detection).
See the Sense Resistors section for information about
setting the voltage and current control loop thresholds.
Feed-Forward Control
Both control loops are influenced by the input voltage
feed-forward (V
BATT
) control circuitry of the MAX1739/
MAX1839. Feed-forward control instantly adjusts the
buck regulator’s duty cycle when it detects a change in
input voltage. This provides immunity to changes in
input voltage at all brightness levels. This feature
makes compensation over wide input ranges easier,
makes startup transients less dependent on input volt-
age, and improves line regulation for short DPWM on-
times.
The MAX1739/MAX1839 feed-forward control is imple-
mented by varying the amplitude of the buck-switch’s
PWM ramp amplitude. This has the effect of varying the
duty cycle as a function of input voltage while maintain-
ing the same V
CCI
and V
CCV
. In other words, V
BATT
feed
forward has the effect of not requiring changes in error-
signal voltage (V
CCI
and V
CCV
) to respond to changes in
V
BATT
. Since the capacitors only need to change their
voltage minimally to respond to changes in V
BATT
, the
controller’s response is essentially instantaneous.
Transient Overvoltage Protection
from Dropout
The MAX1739/MAX1839 are designed to maintain tight
control of the transformer primary under all transient
conditions. This includes transients from dropout,
where V
BATT
is so low that the controller loses regula-
tion and reaches maximum duty cycle. Backlight
designs will want to choose circuit component values to
minimize the transformer turns ratio in order to minimize
primary-side currents and I
2
R losses. To achieve this,