Danfoss AVP-F (Generation 2006) User Manual
Page 5
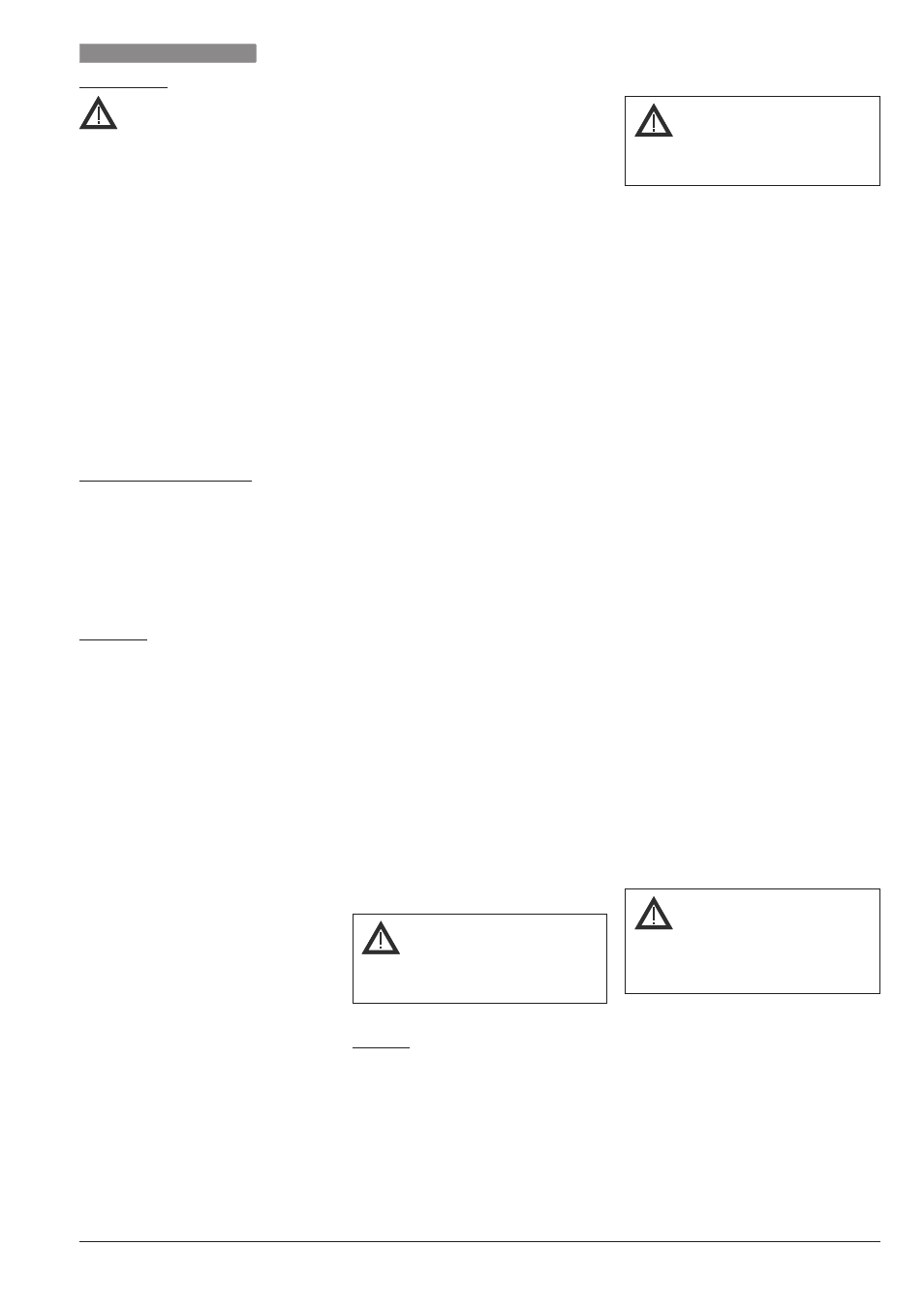
73695010 DH-SMT/SI
VI.DB.N3.8I
© Danfoss 04/2009
5
safety Notes
Prior to assembly and commissioning
to avoid injury of persons and damages
of the devices, it is absolutely necessary
to carefully read and observe these
instructions.
Necessary assembly, start-up, and
maintenance work must be performed
only by qualified, trained and authorized
personnel.
Prior to assembly and maintenance work
on the controller, the system must be:
- depressurized,
- cooled down,
- emptied and
- cleaned.
Please comply with the instructions of the
system manufacturer or system operator.
Definition of Application
The controller is used for pressure relief
control of water and water glycol mixtures
for heating, district heating and cooling
systems.
The technical parameters on the product
labels determine the use.
Assembly
Admissible Installation Positions ❶
Medium temperatures up to 100 °C ①:
- Can by installed in any position.
Medium temperatures > 100 °C ②:
- Installation permitted only in
horizontal pipelines with the
actuator oriented downwards.
Installation location and
Installation scheme ❷
AVP (-F) return mounting ①
AVP (-F) flow mounting ②
Valve Installation ❸
1. Clean pipeline system prior to assembly.
2. The installation of a strainer in
front of the controller is strongly
recommended ①.
3. Install pressure indicators in front of and
behind the system part to be controlled.
4. Install valve
• The flow direction indicated on
the product label ② or on the
valve ③ must be observed.
• The valve with mounted weld-
on tailpieces may only be
spotwelded to the pipeline ④.
The weld-on tailpieces may be welded
only without the valve and seals! ⑤
⑥
If these instructions are not observed,
high welding temperatures
may destroy the seals.
• Flanges ⑦ in the pipeline must be in
parallel position and sealing surfaces
must be clean and without any
damage.
Tighten screws in flanges
crosswise in 3 steps up to the
maximum torque (50 Nm).
5. Caution:
Mechanical loads of the valve body by the
pipelines are not permitted ⑧.
Impulse tube and seal pot mounting
• Which impulse tubes to use?
❹
Use Impulse tube set AV ① or
use following pipe:
Copper Ш 6 Ч 1 mm EN 12449
• Connection of impulse tube and seal pot
③
in the system
❺
- Return mounting ①
- Flow mounting ②
• Connection to the pipeline ❻
It is strongly recommended to install the
impulse tube to the pipeline horizontally
①
or upwards ②.
This prevents dirt accumulation in the
impulse tube and possible malfunction
of the controller.
Connection downwards is not
recommendable ③.
• Impulse Tube Mounting ❼
1. Cut pipe perpendicularly to the pipe
axis and smooth edges out ①.
2. Press impulse tube ② into the
threaded joint up to its stop.
3. Tighten union nut ③ Torque 14 Nm
Insulation ❽
For medium temperatures up to 100 °C the
pressure actuator ① may also be insulated.
Dimensions, Weights
❾
(See page 2)
1)
Conical ext. thread acc. to EN 10226-1
2)
Flanges PN 25, acc. to EN 1092-2
Other flange dimensions - see table for
tailpieces.
start-up
❿
Filling the system, first start-up
1. Slowly open shut-off devices ① in the
flow pipeline.
2. Slowly open shut-off devices ② in the
return pipeline.
3. Slowly open shut-off devices ③ in the
flow pipeline.
4. Slowly open shut-off devices ④ in the
return pipeline.
leak and Pressure Tests
Pressure must be gradually increased at
the +/- connection ⑤.
Non-compliance may cause damages at
the actuator or the valve.
A pressure test of the entire system
must be carried out in accordance with
manufacturer’s instructions.
The maximum test pressure is: 1.5 × PN
PN - see product label!
Putting out of operation
1. Slowly close shut-off devices ③ in the
flow pipeline.
2. Slowly close shut-off devices ④ in the
return pipeline.
settings
Differential Pressure setting
⓫
(not relevant at fixed setting version AVP-F)
The pressure setting range is indicated on
the product label ①.
Procedure:
1. Start system, see section “Filling the
system, first start-up“
Completely open all shut-off devices in
the system.
2. Set flow rate on a motorised valve ②, on
which differential pressure is controlled,
to about 50 %.
3. Adjustment
Observe pressure indicators ③ or/and
alternatively see handle scale indication.
Turning to the right (clockwise) ④
increases the set-point (stressing the
spring).
Turning to the left (counter clockwise)
⑤
reduces the set-point (releasing the
spring).
If the required differential pressure is not
attained, a cause may be a too small
pressure loss in the system.
seal
⓬
The set-point adjuster can be sealed by a
seal wire ①, if necessary.
ENglIsh