Orion STARBLAST 6/6I User Manual
Page 32
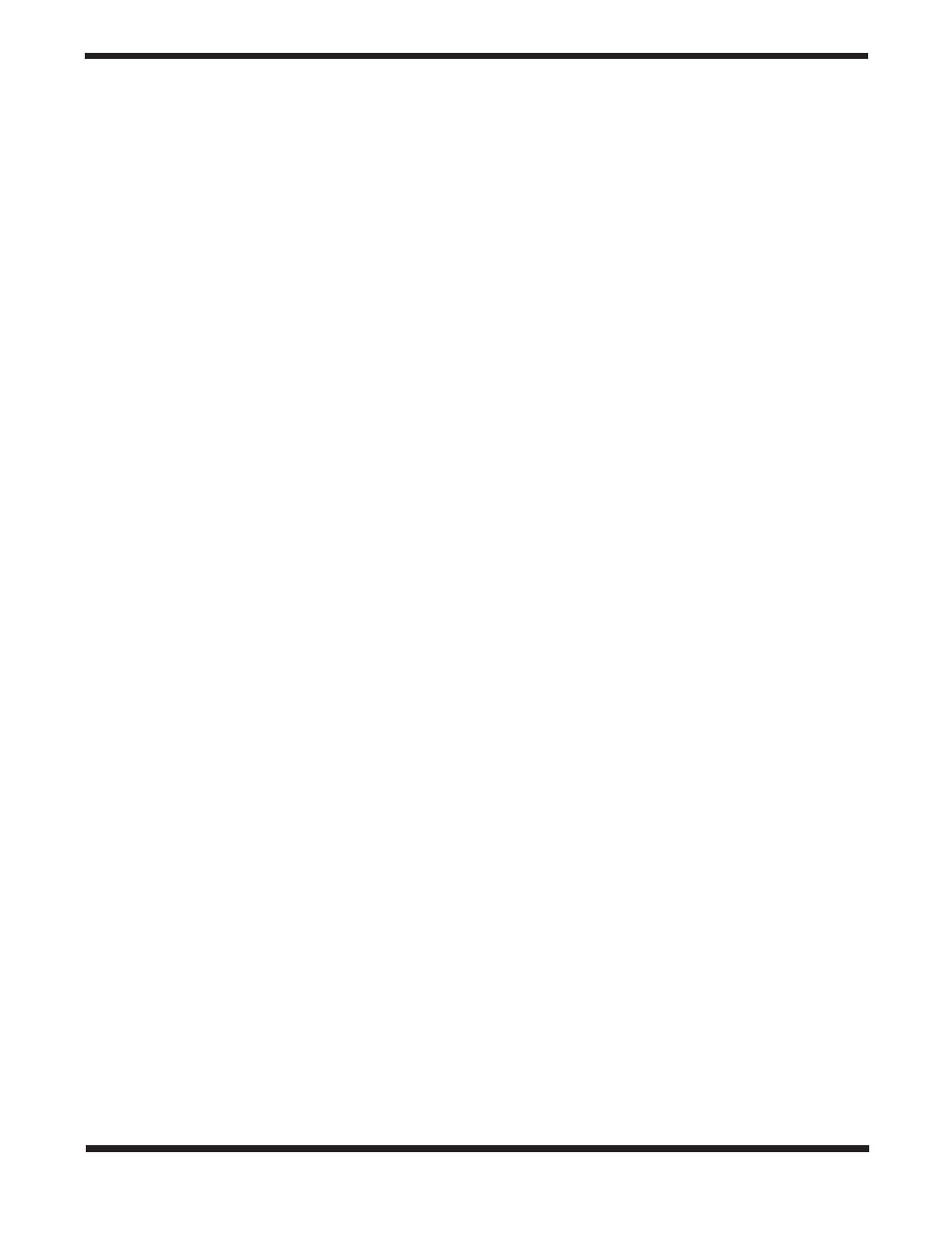
32
screws? If you didn’t and the disk is free to rotate on the
mounting bracket shaft, the IntelliScope system will not
work.
Did you install the aluminum spacer ring on the telescope
6.
mounting bracket shaft after you attached the encoder
disk? The spacer ring is important for maintaining the
correct spacing between the altitude encoder disk and
the sensors on the encoder board.
Is the compression spring seated in its hole just below
7.
the hole for the telescope mounting bracket shaft? Does
it make contact with the altitude encoder board when the
board is in place? This is also important for maintaining
the correct spacing between the altitude encoder disk
and the sensors on the encoder board.
Warp factor consistently above ±0.5 but
below ±2.0
Check accuracy of vertical stop. Use a carpenter’s level
8.
to do this.
Are alignment stars being centered with reasonable
9.
precision? A high-power eyepiece (at least 10mm focal
length), or an illuminated reticle eyepiece (preferred) is
recommended.
Check encoders as outlined previously.
10.
Try to use alignment stars that are well above the
11.
horizon. Light from stars is refracted as it travels through
the atmosphere and starlight near the horizon has to
travel through the greatest amount of atmosphere before
reaching your telescope. Stars near the horizon can
appear as much as 2° away from their actual position.
Avoid long delays between aligning on the first and
12.
second alignment stars. The stars in the night sky appear
to move due to the rotation of the Earth. If you take
more than a few minutes to align on the second star, this
stellar motion will result in an increase in the warp factor
(and decrease the resultant pointing accuracy). This
is because the controller does not yet have a frame of
reference to tell which way the stars should appear to be
moving before the second star is aligned on.
Warp numbers larger than 2.0
Are the stars you aligned on actually the stars you
13.
selected on the controller? Consult the finder charts in
Appendix D if you are unsure.
The encoder sensors may be coming into contact with
14.
the encoder disks. Check both the altitude and azimuth
encoders as outlined above.
altitude readouts do not change when you move
the scope (during “alT aZM TEST”)
Check the altitude cable’s connections.
15.
Make sure the altitude tension knob is not too loose.
16.
azimuth readouts do not change when you move
the scope (during “alT aZM TEST”)
Check the azimuth cable’s connections.
17.
Make sure the hex lock nut on the azimuth axis screw
18.
is tight. The fender washer underneath the hex lock nut
should not be able to move. Remember, the hex lock nut
should be tightened about 3/16 to 1/4 turn beyond the
point where the washer cannot move any longer.
Try disassembling then reassembling the azimuth
19.
encoder by disassembling the top and bottom
baseplates.