Wiring diagra, Wiring diagrams, Maintenance – Raypak MVB 503-2003 User Manual
Page 48: Udb fault history, Suggested minimum maintenance schedule
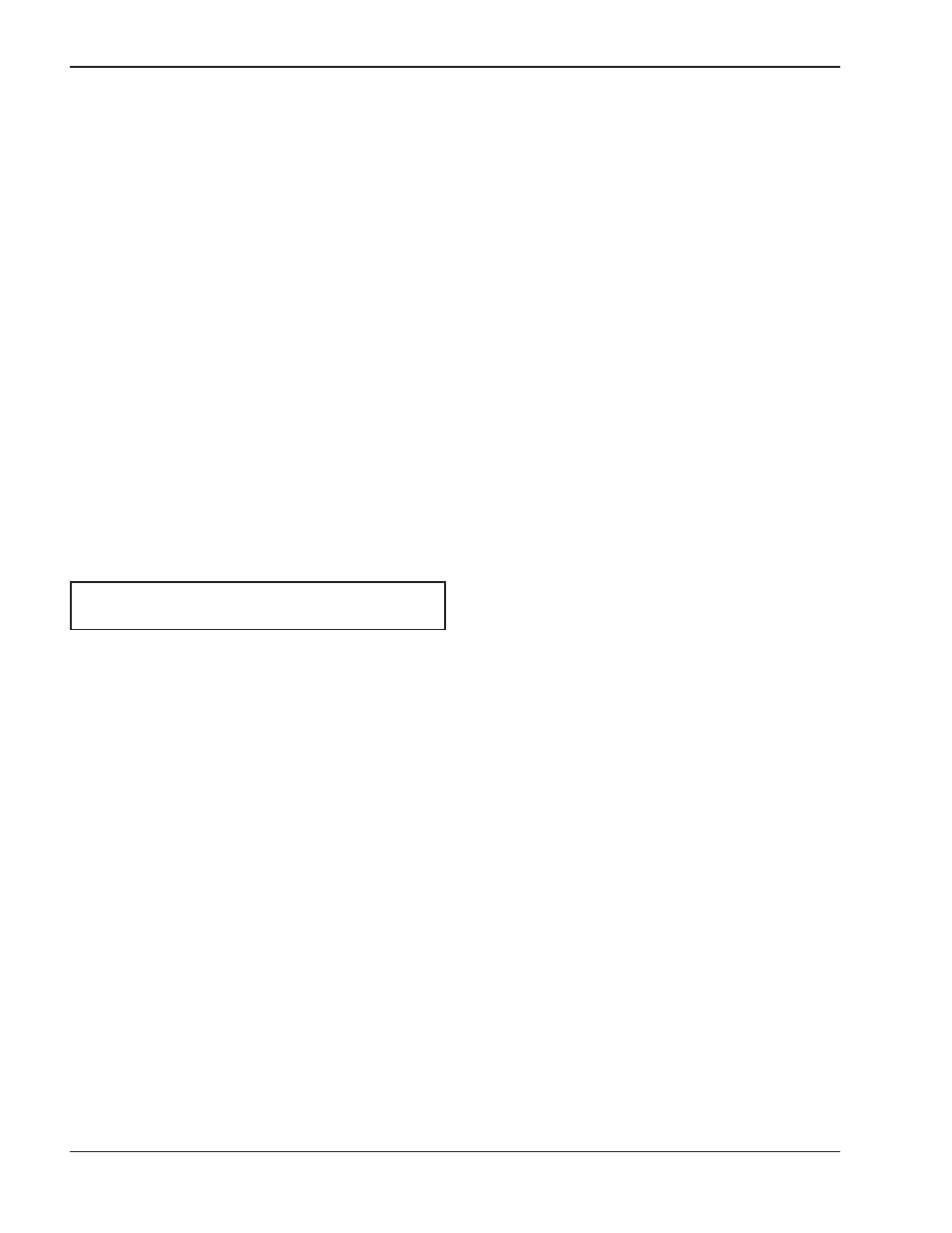
48
UDB Fault History
To view the fault codes in the UDB history file:
1. Press the UP or DOWN buttons on the membrane
switch for 2 seconds to access the fault history.
2. Press either button to scroll through the recorded
faults in history.
3. The most recent fault recorded will be the first fault
displayed (the last 16 faults are stored in the his-
tory, on a rolling basis). There is no time or date
stamp associated with these faults.
4. When the history of faults has been exhausted,
pushing the UP or DOWN buttons again will roll
the fault history over and it will start again.
5. To exit the fault history, wait for 10 seconds and
the board will automatically exit the history mode.
To clear the fault history, press and hold both the UP
and DOWN buttons for 5 seconds while the power is
on.
Diagnostic information is provided any time a fault is
recorded. This information is intended to assist in
locating the problem with the heater, but is not exhaus-
tive.
If multiple fault conditions occur at the same time, only
the fault that caused the heater to shut down will be
recorded in the history.
NOTE: Once the history has been cleared, it cannot
be recovered.
MAINTENANCE
Suggested Minimum
Maintenance Schedule
Regular service by a qualified service agency and
maintenance must be performed to ensure maximum
operating efficiency.
Maintenance as outlined below may be performed by
the owner.
Daily
1. Check that the area where the heater is installed
is free from combustible materials, gasoline, and
other flammable vapors and liquids.
2. Check for and remove any obstruction to the flow
of combustion or ventilation air to heater.
Monthly
1. Check for piping leaks around pumps, mixing
valves, relief valves, and other fittings. If found,
repair at once. DO NOT use petroleum-based
stop-leak compounds.
2. Visually inspect burner flame.
3. Visually inspect venting system for proper func-
tion, deterioration or leakage.
4. Visually inspect for proper operation of the con-
densate drain in the venting. If leaks are observed
repair at once.
5. Check air vents for leakage.
Yearly (Beginning Of Each Heating
Season)
Schedule annual service call by qualified service
agency.
1. Visually check top of vent for soot. Call service
person to clean. Some sediment at bottom of vent
is normal.
2. Visually inspect venting system for proper func-
tion, deterioration or leakage. Ensure that
condensate drain is inspected and ensure that
condensate is being directed to appropriate con-