Navman JUPITER LA000605D User Manual
Page 19
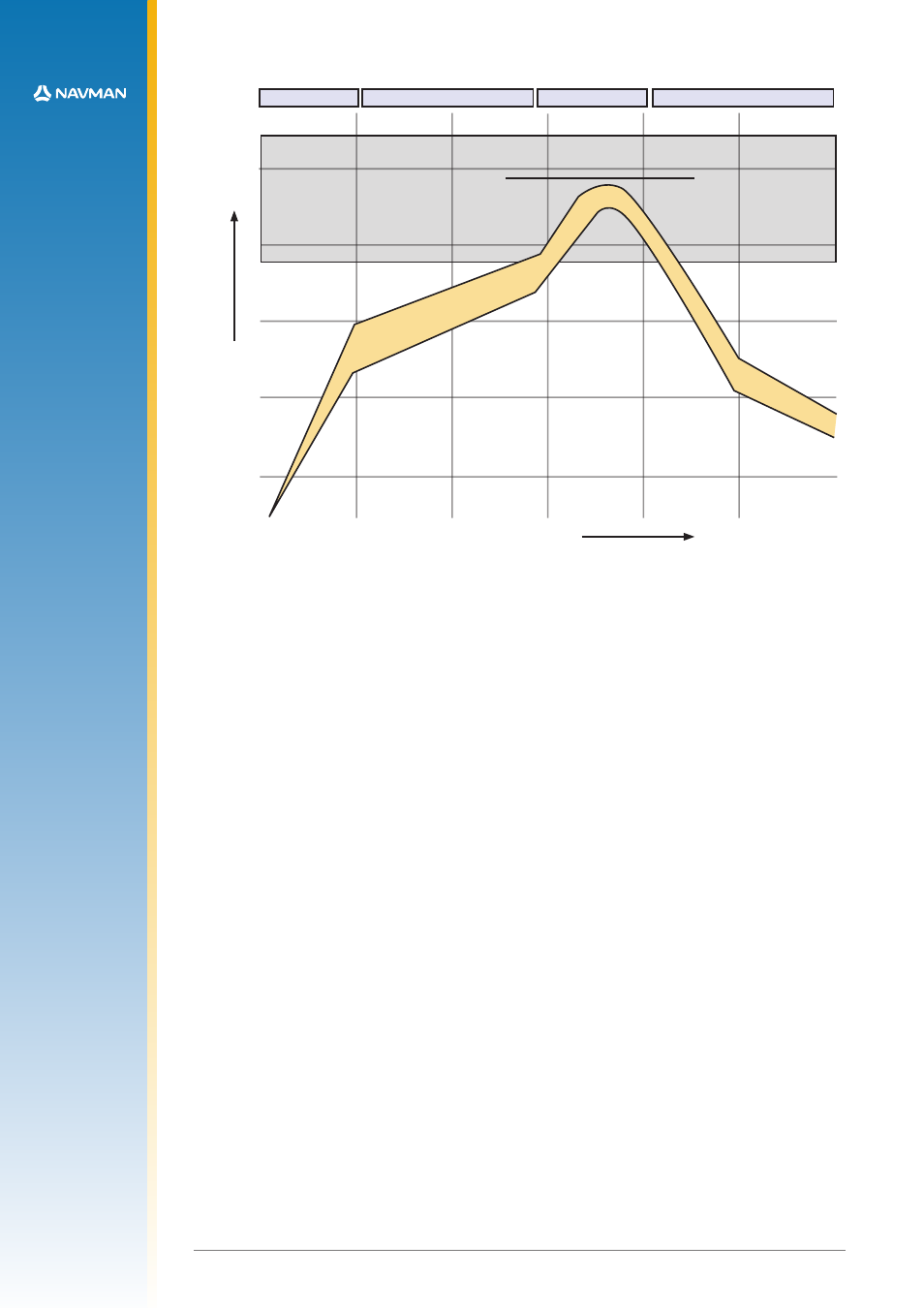
Te
m
pe
ra
tu
re
o
C
Time Sec
260
300
0
Pre-heat
Reflow
Cool-down
Liquidus Temp.
Peak Temp.
Pb Solder
Pb-free Solder
Heat
LA000605D © 2007 Navman New Zealand. All rights reserved. Proprietary information and specifications subject to change without notice.
Figure 4-1: Sample Lead and Lead free reflow profile
4.1.5 Coating
The final PCB may be selectively coated with an acrylic resin, air / oven cured conformal
coating, clear lacquer or corresponding method, which gives electrical insulation and
sufficient resistance to corrosion.
4.1.6 Post reflow washing
It is recommended that a low residue solder paste is used to prevent the need for post reflow
washing. If a washing process is used, an aqueous wash is not recommended due to the
long drying time required and danger of contaminating the fine pitch internal components.
4.1.7 Pre-baking
The modules will be delivered on a tape and reel package, and sealed in an airtight bag. The
MSR (Moisture Sensitivity Rating) is 3, therefore they should be loaded and reflowed within
168 hours (7 days). If the modules are in ambient humidity for longer than this, a pre-baking/
drying process will be required.
4.1.8 Rework
It is recommended that no more than 2 reflow cycles are performed and that the maximum
reflow temperature recommended by the solder paste manufacturer is not exceeded. The
maximum ramp-up rate of 3
o
C/sec for leaded solder or 4
o
C/sec for lead free solder should
not be exceeded.
Navman recommends that rework and repair is carried out in accordance with the following
guidelines:
• IPC-7711 Rework of Electronic Assemblies
• IPC-7721 Repair and Modification of Printed Boards and Electronic Assemblies
For proper removal of the part, special nozzles should be used for local heating of the part
to avoid reflow of adjacent parts. The PCB assembly should be preheated to about 75° C
from the bottom using convective pre-heaters and the preheated nozzle should be lowered