0 manufacturing process recommendations – Navman JUPITER LA000605D User Manual
Page 18
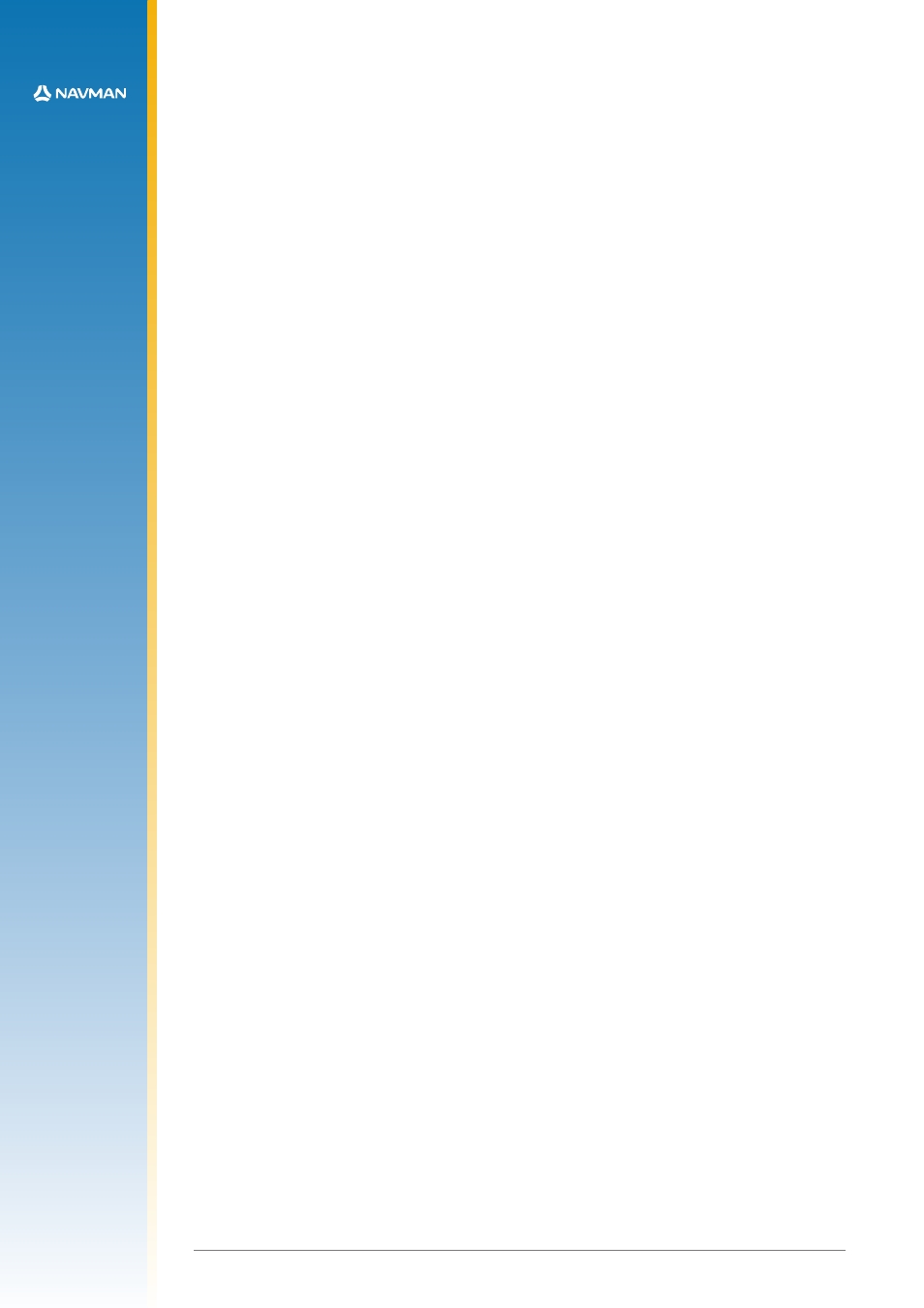
LA000605D © 2007 Navman New Zealand. All rights reserved. Proprietary information and specifications subject to change without notice.
4.0 Manufacturing process recommendations
The Jupiter 32 uses the latest Land Grid Array (LGA) technology. Solder interconnect is
formed solely by solder paste applied to the board assembly. This results in a low stand-off
height, depending on solder paste volume and Printed Circuit Board (PCB) geometry. This
makes LGA ideal for small form-factor applications. Solder joint reliability studies indicate that
LGA greatly exceed typical industry reliability.
4.1 Solder methods
The Jupiter 32 has 34 surface mount connection pads that have a base metal of copper
with an Electroless Nickel Immersion Gold (ENIG) finish. This is suitable for a lead free
manufacturing process. Critical factors to ensure successful circuit board assembly with LGA
devices include, the design of the solder paste stencil, the solder paste and reflow profile
used. Stencil attributes that have been shown to succeed in tests are solder stencil thickness,
aperture diameter, paste release characteristics, and practices to ensure consistent solder
paste volumes that exceed recommended minimums.
4.1.1 Solder paste type
The module will accept all commonly used solder pastes. The solder paste can be lead
based or lead-free. In all processes, factors such as circuit board thickness, fabrication
complexity, assembly process compatibility, and surface finish should be taken into
consideration. Also, due to the low standoff height of LGA devices and difficulty cleaning, a
no-clean paste is recommended.
4.1.2 Solder paste mask size
Solder paste mask size should be adjusted by experimentation according to the production
process requirements. As a starting point, a 0.75:1 (paste mask:pad size) ratio is
recommended.
4.1.3 Solder paste stencils
A 0.125 mm (5 mil) thick stencil is recommended with LGA.
4.1.4 Reflow profile recommendations
An optimal reflow profile depends on solder paste properties and should be optimised and
proven out as part of an overall process development. The following guidelines represent
good soldering practices to help yield high quality assemblies with minimum rework.
It is important to provide a solder reflow profile that matches the solder paste supplier’s
recommendations. Some fluxes need a long dwell time below the temperature of 180°C,
while others will be burned up in a long dwell. Temperatures out of bounds of the solder paste
flux recommendation could result in poor solderability of components on the board. Solder
paste suppliers can recommend an suitable reflow profile to give the best solderability. The
maximum reflow temperature is 260 °C for 10 seconds.
The typical reflow profile consists of four sections. In the preheat section, the PCB assembly
should be preheated at the maximum rate of 1° to 2° C/sec to start the solvent evaporation
and to avoid thermal shock. The assembly can then be heated for 60 to 120 seconds to
remove solder volatiles and activate the flux so the temperature of the package rises above
100° C. The reflow section of the profile, the time above liquidus (approx. 185° C), can be
between 45 to 60 seconds with a peak temperature in the range of 230° to 260° C. This
allows all solder joints on the assembly to fully reflow and a maximum peak temperature that
is below the maximum that the devices or solder material can tolerate. Finally, the assembly
can undergo cool-down in the fourth section of the liquidus point (approx. 185° C). The actual
profile parameters depends upon the recommendations of the solder paste supplier and
other reflow requirements of the customer’s PCB.
Refer to Figure 4-1 for sample lead and lead-free reflow profiles.