Quickdraw, Steam heater – PVI Industries PV500-25 User Manual
Page 10
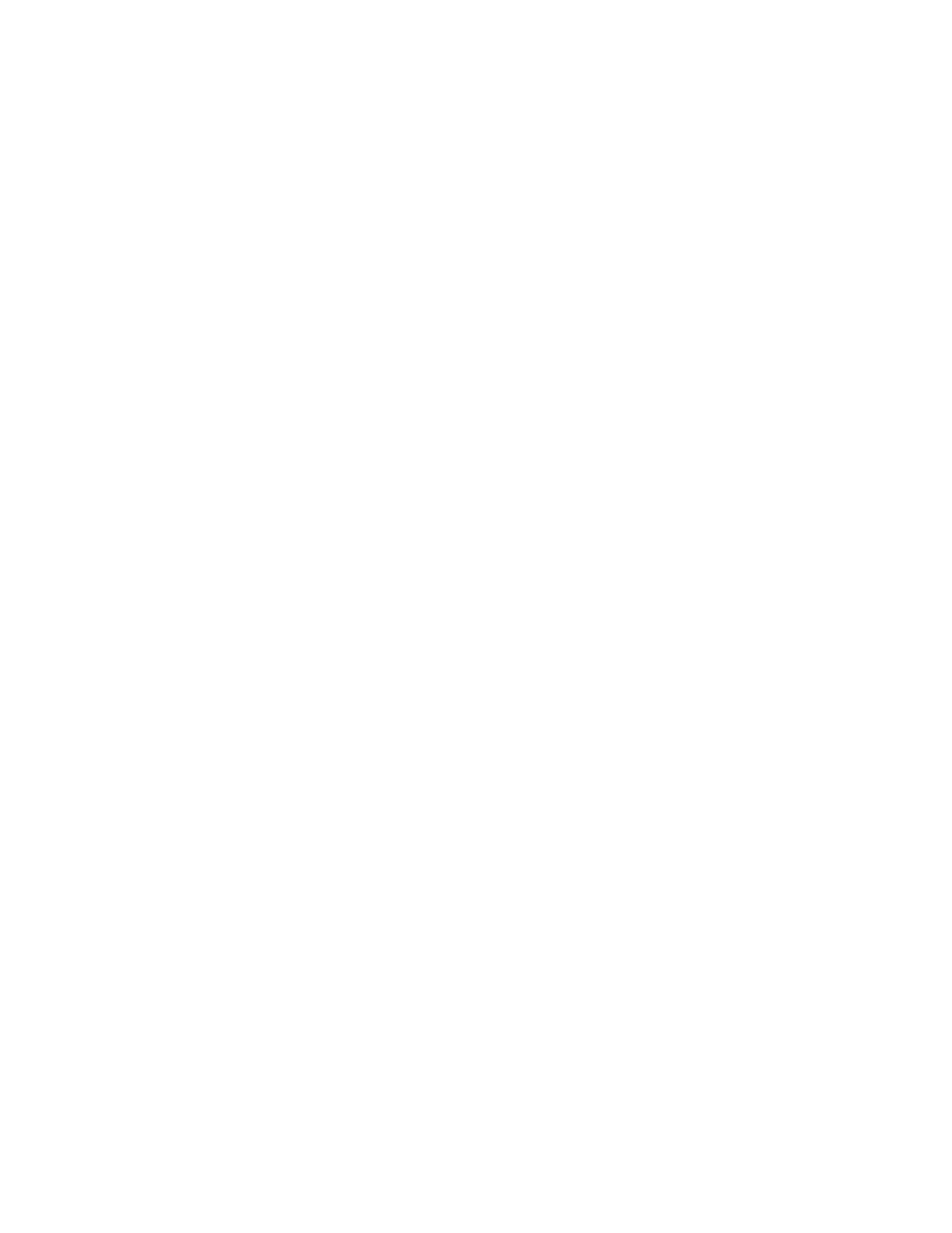
QUICKDRAW
Steam Heater
10
PV500-25 06/12
4. Push control switch, located on the control box, to activate the steam valve and thermostats. Check steam
valve for operation; the valve solenoid should “click” to open valves when operating switch is pushed “on”. The
tank-circulating pump should also operate. Check thermostat settings. The temperature-limiting device is set at
200
F.
Temperature Setting: The operating thermostat is set at the factory at approximately 120°F and the upper
operating thermostat is set at approximately 130°F. Make adjustments by turning the thermostat dial to the
desired temperature.
5. Push the operating switch, located on the control box, to “off” before opening manual main steam supply valve.
This will allow condensate that has collected in the supply line to drain through the trap installed in front of the
steam valve. When the steam supply line is free of condensate, push operating switch to “on”, opening the
electric on-off steam valves allowing steam to flow through the heat exchanger.
WARNING: Do not operate unit under conditions in excess of those specified on nameplate. Failure to
operate the heat exchanger within the design pressure and temperature on the nameplate may result in
damage to the heat exchanger and potential injury to adjacent personnel.
6. Open nearby hot water tap to maintain a flow of water through the tank when starting up units. Regulate flow of
water through the tank to allow the steam valve(s) to cycle off and on. Open nearby hot water tap to maintain a
flow of water through the tank when starting up units. Observe condensate flow at the receiver or other
collection sight to verify satisfactory flow. Check operation of all safety and operating controls.
7. In all installations, there should be no pulsation or water hammer since this causes vibration and strain with
resulting leaks.
8. Retighten bolting on all gasketed joints after the heat exchanger has reached temperature to prevent leaks and
gasket failures. Retightening should be done uniformly and in a diametrically staggered pattern (see
“Maintenance”). On high pressure and high temperature applications or any application where spiral wound
gaskets are required, it is recommended that the gasketed joints of the heat exchanger be retightened to the
required torque (see “Maintenance”) after 24 hours at operating pressures and temperatures to compensate for
any relaxation or creep that may have occurred.
9. In shutting down, remove all power from the system. Close all steam and cold water supply valves to the unit.
10. If the unit is removed from service for an extended period, it must be drained to eliminate the possibility of
freezing and corrosion from stagnant water conditions.
7 MAINTENANCE
WARNING: Turn off all electrical service to the appliance when accessing the remote connections located
inside the control cabinet. These terminals are High Voltage. If the electrical service is not turned off and
these terminals are touched, a dangerous shock causing personal injury or loss of life could occur. Close
and fasten the control cabinet cover before restoring electrical service to the appliance.
7.1
Temperature and Pressure Relief Valve
Operate the temperature and pressure relief valve at least once a year by lifting the lever briefly. If the valve does
not open and close properly when testing, it must be replaced with a like relief valve.
7.2
Thermostats and Temperature Limiting Device
The temperature limiting device and thermostat temperature sensors extend into the water in the tank. Depending
on the water conditions in your area, scale may coat the sensors. This coating will affect accuracy of sensors and
can allow water temperature to exceed the desired limits. Remove and inspect these controls at necessary
intervals. Remove scale if present.
7.3
Steam Valve Actuator
The steam valve actuator (if applicable) is sealed and requires no maintenance. Durability of valve stems and
packing is dependent upon maintaining non-damaging water conditions. Inadequate water treatment or filtration can
result in corrosion, scale, and abrasive particle formation. Scale and particulates can result in stem and packing
scratches and can adversely affect packing life and other parts of the Hydronic system. Contact the manufacturer
for replacement packing and stem & plug assembly.