Sheave and belt alignment, Checking spindle play, Sheave/drive belt replacement – Powermatic 3520B User Manual
Page 18
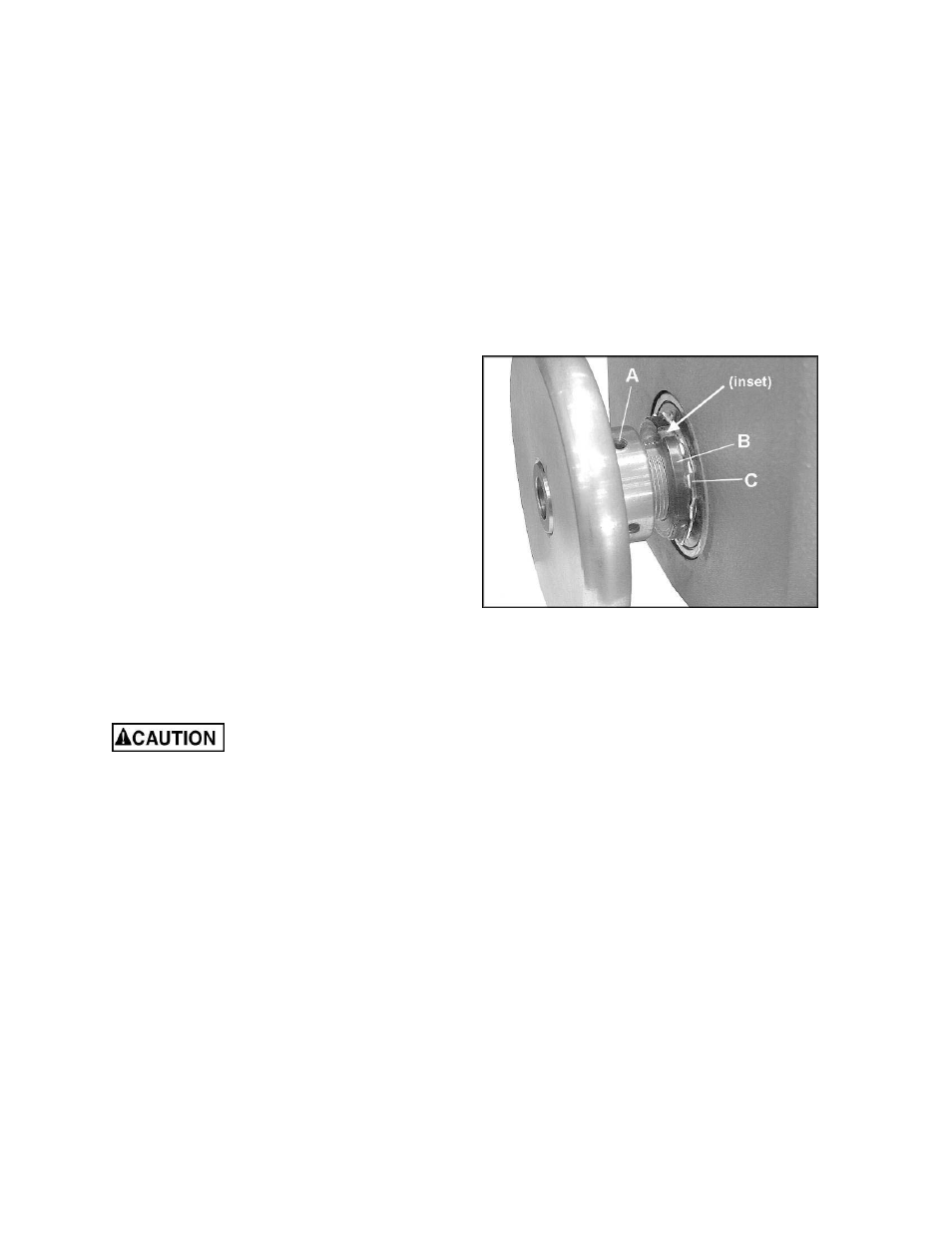
18
Sheave and Belt Alignment
The motor and spindle sheaves are aligned with
each other at the factory, but if any service is
performed that affects their alignment it is very
important that they be realigned. To realign
them, loosen the two set screws on the spindle
sheave (C, Figure 25) with a hex wrench, and
slide the spindle sheave into the proper position.
Re-tighten set screws.
When sheaves and belt are properly aligned,
there should be no unusual pulsing sounds or
noise coming from the belt.
Checking Spindle Play
The spindle bearing has been set at the factory
for general turning applications. There should be
no "end play" or looseness along the spindle’s
axis. If any looseness should ever occur, it may
be rectified by carefully tightening the bearing
lock nut on the spindle, as follows. (See Figure
26).
1. Use a screwdriver to carefully bend back
any tabs on the tabbed lock washer (C,
Figure 26) that interfere with the insets on
the bearing lock nut (B, Figure 26).
2. Place the end of a flat head screwdriver
down against one of the insets of the
bearing lock nut (B, Figure 26).
3. Tap the handle of the screwdriver with a
mallet so that it turns the bearing lock nut
(B, Figure 26) tighter in a clockwise
direction. Rotate the bearing lock nut only
about 1/16” at a time.
Do not over tighten the
bearing lock nut or the spindle bearings will
overheat.
4. The bearing lock nut should be tightened
just enough to remove the end play and the
spindle should still rotate very freely. Run
the lathe for a time, and check for heat from
the spindle bearings. If the bearings are
running hot, the bearing lock nut is too tight
and should be loosened slightly.
5. After the bearing lock nut (B, Figure 26) has
been properly adjusted, carefully bend back
into place any tabs on the tabbed lock
washer (C, Figure 26).
Sheave/Drive Belt Replacement
Replacing the spindle sheave can be a difficult
procedure; it is recommended that the
headstock be taken to an authorized service
center for this.
Figure 26