Diagrams, Idealarc® dc-1000 – Lincoln Electric IDEALARC IM420-D User Manual
Page 25
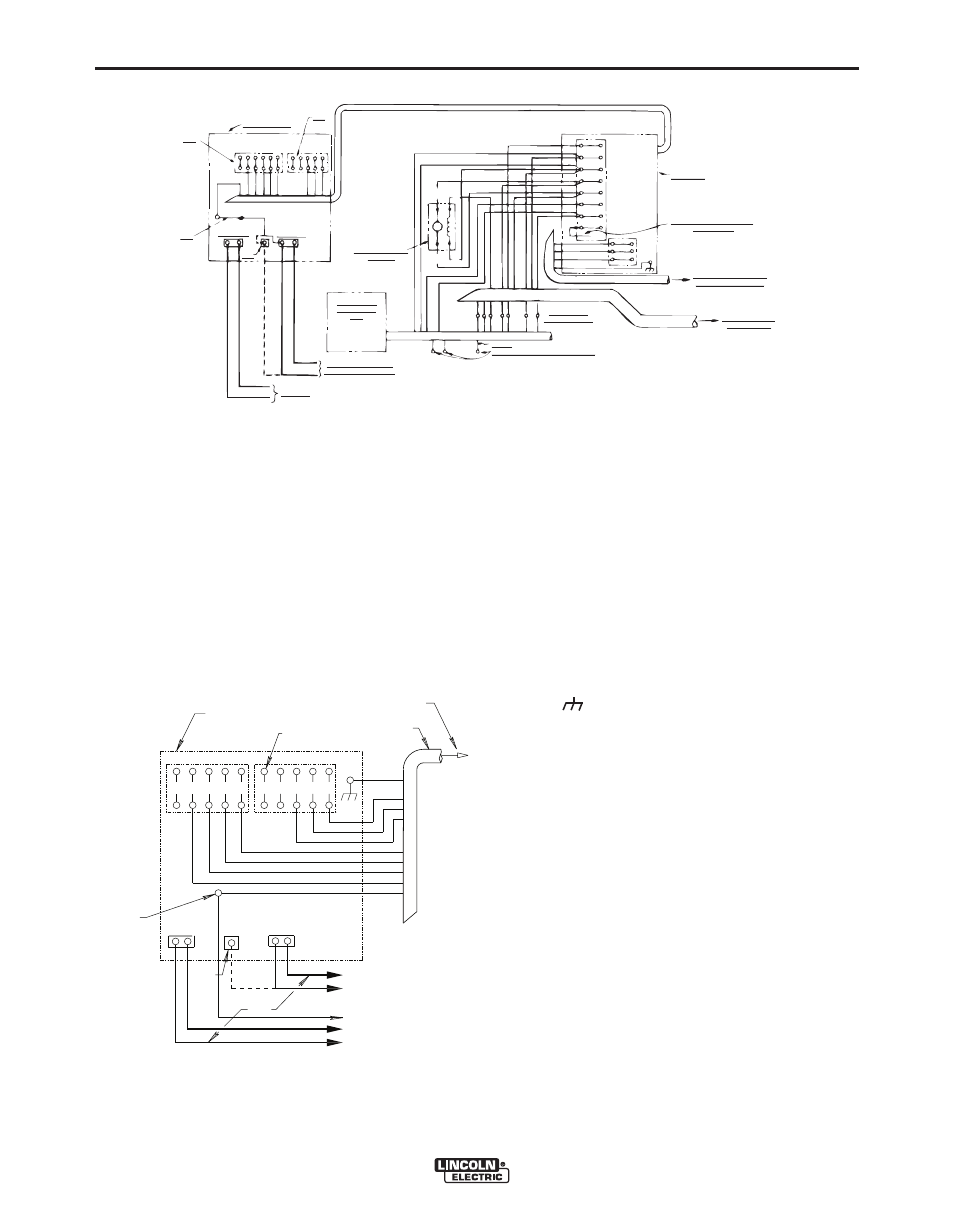
F-2
DIAGRAMS
F-2
IDEALARC® DC-1000
CONNECTION OF DC-1000 WITH NL OPTION KIT TO LT-3 or LT-34 (Obsolete)
N.A.
On all DC-1000 and DC-1500’s
above Code 8234 extend lead 67
and connect it to the electrode cable
going to the automatic equipment.
N.B.
On DC-1500 units below code 8234
this is #67 and the LT-3 or LT-34 #67
lead can be connected either to the
#67 or the electrode cable terminal
as shown. Terminal 82 not present
on later D.C. 1500’s and all DC-
1000’s.
N.C. Terminals 73 & 74 not present on
earlier DC-1500’s.
N.D. Alternative 500 amp positive terminal
connection provided on DC-1000
models above code 9500 only.
This diagram shows the electrode connect-
ed positive. To change polarity, turn power
source off, reverse the electrode and work
leads at the power source and position the
switch on the power source and NL Option
Kit to the proper polarity. Also reverse the
leads on the back of the ammeter and volt-
meter in the LT-3 control box.
Contactor drop out delay switch on the NL
Option Kit must be in the “On” position.
The 4/0 cables shown will handle up to
1000 amps at 80% duty cycle. For higher
currents or duty cycle add additional cables
to the power source output studs.
CONNECTION OF DC-1000 OR DC-1500 to NA-3, LT-5 or LT-7
Connect the control cable ground lead to the frame terminal
marked near the power source terminal strip. The
power source must be properly grounded.
*If using an older control cable: Connect lead #75 to #75 on termi-
nal strip, connect lead #76 to #76 on terminal strip, connect lead
#77 to #77 on terminal strip.
N.A.
Welding cables must be of proper capacity for the current
and duty cycle of immediate and future applications.
N.B.
Extend lead 21 using #14 or larger insulated wire physically
suitable for the installation. An S16586-[ ] remote voltage
sensing work lead is available for this purpose. Connect it
directly to the work piece keeping it electrically separate from
the welding work lead circuit and connection. For conve-
nience, this extended #21 lead should be taped to the weld-
ing work lead.
N.C. Tape up bolted connection.
N.D. Terminals 73 & 74 not present on earlier DC-1500.
N.E.
Alternative 500 amp positive terminal connection provided
on DC-1000 models above code 9500 only.
Above diagram shows electrode connected positive. To change
polarity, turn power source off, reverse the electrode and work
leads at the power source and position the switch on power
source to proper polarity. Also reverse the leads on the back of
the ammeter and voltmeter in the automatic control box.
TO WORK
LT-3 REMOTE
DC CONTROL
BOX
ELECTRODE CABLE TO
AUTOMATIC EQUIPMENT
N.D.
NEGATIVE
POSITIVE
N.A.
N.B.
POWER SOURCE
N.C.
73 74
75
76
77
82
21
4
2
31 32
67 21 4
2 31 32
75 76 77
35 VOLT CONTROL
EXCITER
21
1
C
F
E
D
10
6
75
76
77
GND
75
76
77
1
4
2
10
21
32
31
22
BOLT & TAPE
7 CONNECTIONS
41 42 43
44 58
59
61
6
10 4 21
1 2 31
SPARE
TAPE UP SPARE LEADS (NOT USED)
2 1 32
31
29
5
41 42 43
44 58
59
61
NL OPTION
CONNECT THE RED LEAD TO
TERMINAL 22
K-775 REMOTE CONTROL
MOUNTED AT TRACTOR
TO LT-3 TRACTOR
CONTROL BOX
2 1 4
2
3 1 3 2
7 3 7 4 7 5 7 6 7 7
4
G
N
D
P O W E R S O U R C E
N E G A T I V E
P O S I T I V E
2 1
N . A .
E L E C T R O D E C A B L E T O
T O W O R K
}
C O N T R O L C A B L E
3 2
3 1
2
C
B
A
}*
N . B . &
N . C .
T O A U T O M A T I C
C O N T R O L B O X
N . D .
N . E .
A U T O M A T I C E Q U I P M E N T
}
M13322
8-2-90F
S15534
8-2-90F