Stator protection, Repetitive starts, Start inhibit – Siemens MCC-3298 User Manual
Page 25: Cooling time constants, Ground fault protection, Class f insulation, 24 ground fault detection, 3 operating the samms-lv device
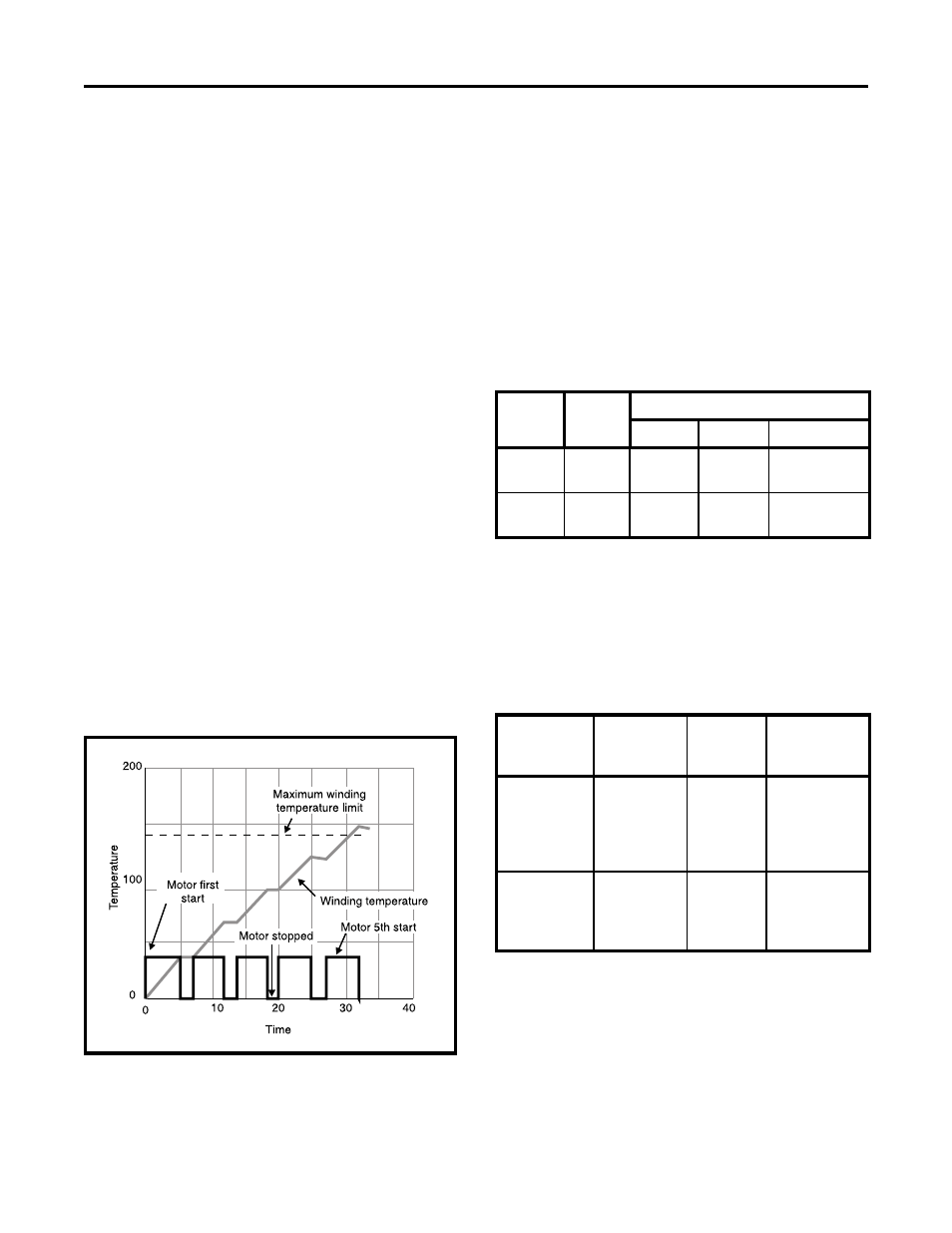
23
3 Operating the SAMMS-LV Device
3.19 Stator Protection
By selecting the overload class slightly greater than or equal to
the motors starting time, the motor model defines an energy I
2
t
value. In this value, I equals 600% of the motors full load current
and t equals the overload class selected.
If the amount of energy exerted by the motor during start, stall
or under locked rotor condition exceeds the amount of energy
defined by the overload class selected, the SAMMS-LV device
will trip. This protects the motors winding against excessive
heat build up. For example, a typical motor starts within 3 to 4
seconds. By selecting an overload class 4 or 5, you can safely
start the motor hot or cold and without nuisance tripping. This
also provides protection against stall time exceeding 4 or 5
seconds; assuming the locked rotor current equals 600% of the
motors full-load current (See Figure 3.10).
3.20 Repetitive Starts
The motor model allows repetitive starts without nuisance
tripping while protecting the motor against overload and stall
conditions. Repetitive starts can occur as long as the following
conditions are met:
1. The energy exerted by the motor during start does not
exceed the energy defined by the overload class selected.
2. The motor winding temperature does not exceed the maxi-
mum temperature allowed.
3. The SAMMS-LV is not in start inhibit (See Section 3.21).
For example, a motor starting from cold condition could have
4 or more typical starts of 5 seconds without nuisance tripping
and without damaging the motor insulation. Figure 3.11 shows
a multi-start scenario for an open drip-proof motor.
Figure 3.11 Multi-start scenario for an open drip-proof motor
3.21 Start Inhibit
When the motor temperature reaches the maximum values
allowed, the SAMMS-LV device trips. If you attempt a restart,
the overload LED flashes and the motor will not start until the
motor winding and rotor temperatures cool down to the full load
temperature. HHC function F25 displays the motor winding
temperature as a percentage of the full-load temperature. HHC
function F10 displays the time to enable restart in seconds.
3.22 Cooling Time Constants
The motor time constants vary based on whether the motor is
running idle or is stopped. The values listed in Table 3.4 are used
in the motor model.
Motor
Cond.
Delta
Temp.
Motor FLC
0.3-9.0A 9.1-65A
65.1-540A
Stopped 80º C to
29º C
1750 s
5500 s
9100 s
Running
Idle
80º C to
39.4º C
600 s
1800 s
2800 s
Table 3.4 Motor time constants
3.23 Normalized Temperature Rise for Class
B and Class F Insulation
Steady state and maximum winding temperature are functions
of the motors insulation class. In this motor model, normalized
temperature rise for both Class B and Class F insulation are
used. The motor winding temperature is displayed as a per-
centage of the steady-state full-load temperature rise as shown
in Table 3.5.
Boundary
Parameters
Class B
Insulation
Class F
Insulation
% Full Load
Temperature
Rise
Steady State
Temperature
rise at
full-load
current
80º C
105º C
100
Maximum
allowed
winding
temperature
140º C
185º C
175
Table 3.5 Steady state and maximum winding temperature rise
3.24 Ground Fault Detection
In SAMMS-LV devices, HHC function F12 selects ground fault
protection or warning.
•
protection = ON
•
warning = OFF
The device detects a ground fault if the fault current exceeds the
pickup level for 360 msec. If you have selected protection (ON),