Operation – Southbend SB1231 User Manual
Page 6
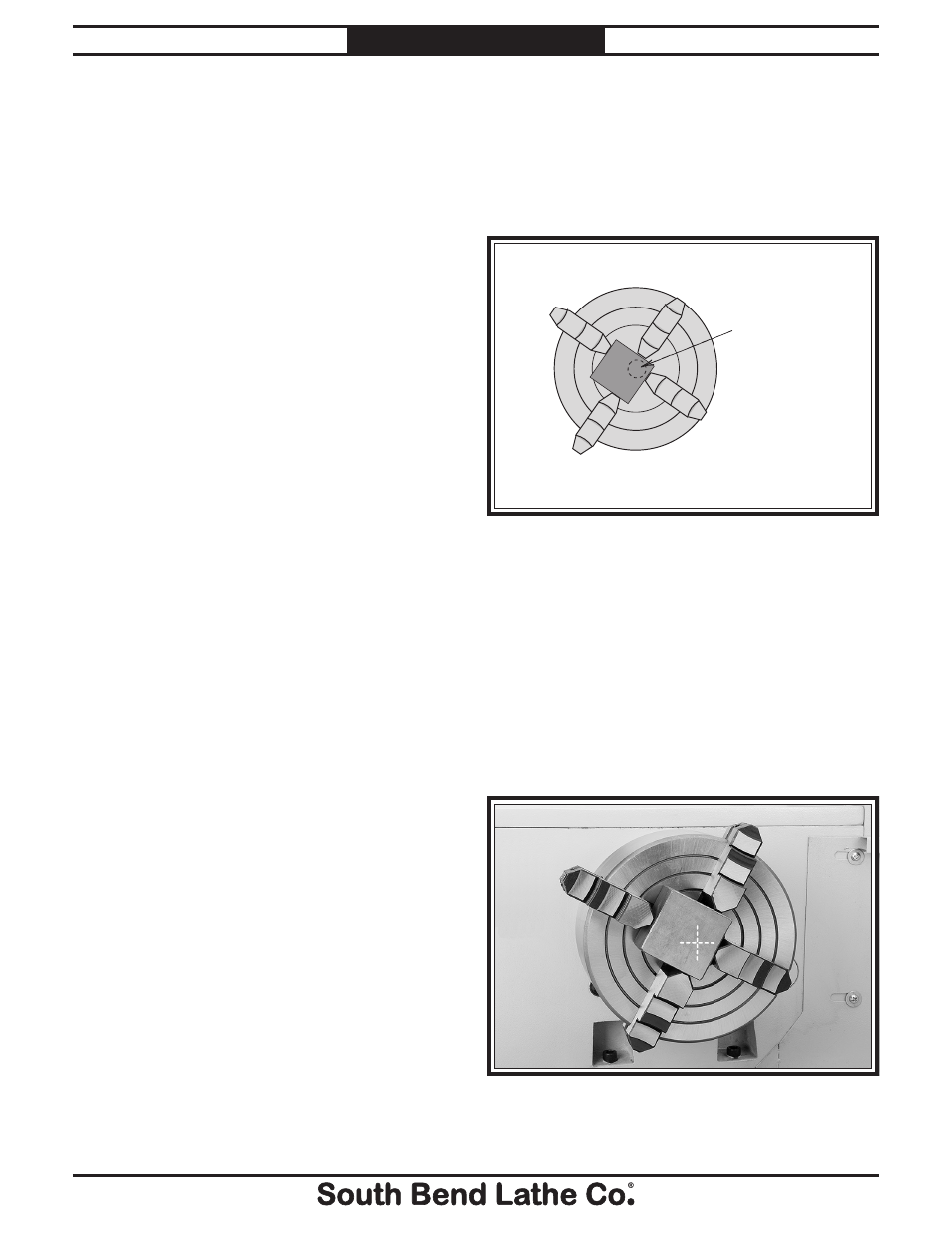
CAUTION: During the next step, the
chuck may come off suddenly, so it
is important that you are ready to
support its weight with a chuck cradle
to prevent crushing your fingers or
dropping the chuck.
4. Using a dead blow hammer or other
soft mallet, lightly tap around the outer
circumference of the chuck body to break the
chuck free from the camlocks and the spindle
nose taper.
5. Use a rocking motion to carefully remove the
chuck from the spindle.
— If the chuck does not immediately come
off, rotate the chuck approximately 60˚
and tap again. Make sure all the marks
on the cams and spindle are in proper
alignment for removal.
Operation
Non-cylindrical parts can be held and brought
into the spindle centerline for facing or boring
The other benefit is that the majority of
workpieces can be positioned out of the spindle
rotation axis if a bore (see Figure 9) or a step
needs to be cut into a workpiece on an outlying
edge. For the best grip possible on odd-shaped
workpieces, one or more jaws can also be rotated
180° to grab more surface area for clamping.
If all four jaws cannot be used to hold the
workpiece, you must use faceplate to reduce the
risk of a workpiece being thrown.
To clamp a workpiece in the chuck:
1. DISCONNECT LATHE FROM POWER!
2. Install a center in the tailstock.
3. Retract each jaw and place the workpiece
flat against the chuck face.
4. Slide the tailstock forward, so the tip of the
dead center applies enough pressure against
the workpiece to hold it in place, and then
lock the tailstock in position.
5. Move each jaw until it makes light contact
with the workpiece.
Figure 8. Tightening sequence.
7. After the workpiece is held in place by
the jaws, turn the chuck by hand and pay
attention to the workpiece alignment.
— If the workpiece is not correctly aligned
for your operation, turn the chuck and
make fine adjustments by slightly
loosening one jaw and tightening the
opposing jaw until the workpiece is
correctly aligned (see Figure 9 for an
example).
1
2
3
4
Hole to be
bored into
workpiece
Figure 9. Non-concentric workpiece correctly clamped
in the 4-jaw chuck.
6. Following the sequence shown in Figure 8,
tighten each jaw in small increments to move
the workpiece into the required position.
Check frequently to make sure the intended
center point of the workpiece has not
wandered away from the spindle centerline
while the jaws are being tightened.
-6-
Mfg. Since 5/10
Model SB1231
I N S T R U C T I O N S