Bearing replacement, Maintenance – Siemens 680 User Manual
Page 23
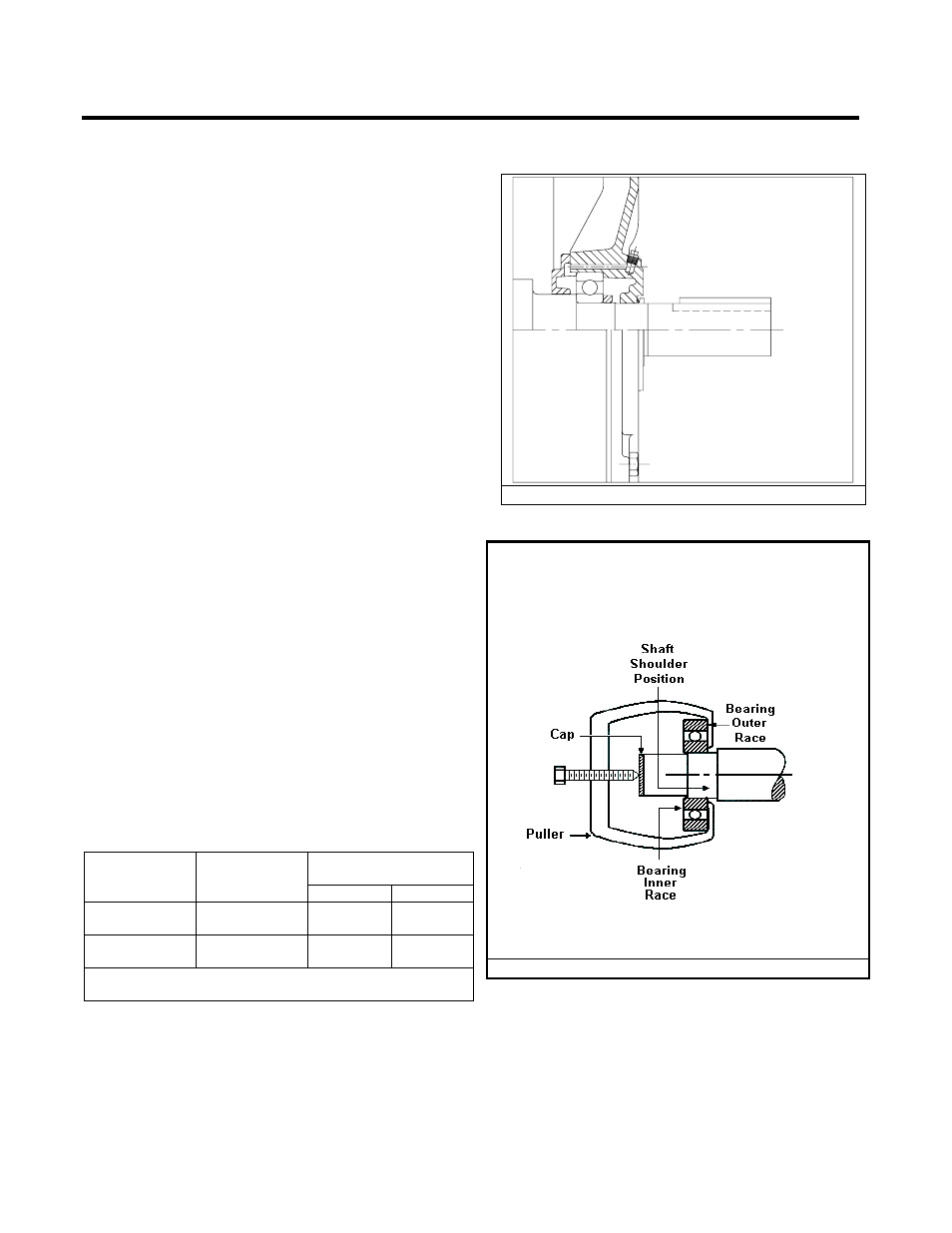
- 22 -
Maintenance
Bearing Replacement
Antifriction Bearings
For typical antifriction bearing configuration, see
Figure 3.
Replacement bearings may be of a different
manufacturer but must be equal to the originals used in
the motor. When ordering bearings specify as follows:
1. The complete A.F.B.M.A. (Anti-Friction Bearing
Manufacturers’ Association) bearing number from
the motor nameplate.
2. Identifying numerals and manufacturer stamped on
the bearing.
3. Bearing tolerance class, i.e. - A.B.E.C.-1 (Annular
Bearing Engineers’ Committee Tolerance Class
One).
4. Internal radial clearance, i.e. – A.F.B.M.A.-3
(Clearance Class Three).
5. Electric motor quality.
To Replace Antifriction Bearings
1. Remove bolts holding end caps to housings.
2. Remove bolts holding bearing housings to yoke.
3. Remove bearing housings.
4. Remove the bearing with a puller. See Figure 4.
5. Check shaft and housing diameter for proper size
with micrometer.
6. Heat the new bearing in an oven (200°F). While
it is hot, slide the bearing onto shaft – make
certain that the inner race makes a firm even
contact with shaft shoulder. Do not subject
bearing to impact.
7. Let bearing cool - pack bearing caps with the
proper grease.
8. Reassemble end caps and housings.
The amount of grease to be used when repacking a
bearing after cleaning or replacement is shown in the
table below.
Grease Quantity*
(End Caps)
Type
Bearing
Operating
Bearing
(Shaft)
Outer Inner
Deep Groove
Ball
Horizontal
2/3 Full
1/3 Full
Roller
Horizontal
1/3 Full
1/3 Full
*
Pack all open bearings full between balls or roller but remove
excess grease on outside of retainers.
Figure 3. Ball Bearing Construction
Protect the shaft end with a cap. If bearing is reusable,
make certain the puller applies pressure against the
bearing inner race only. If puller will not hook the bearing
inner race, fabricate a split bushing and install it between
the bearing and the puller hooks.
Figure 4. Removing Bearing with a Puller