Brooks, Model 5851e – Brooks Instrument 5851E User Manual
Page 27
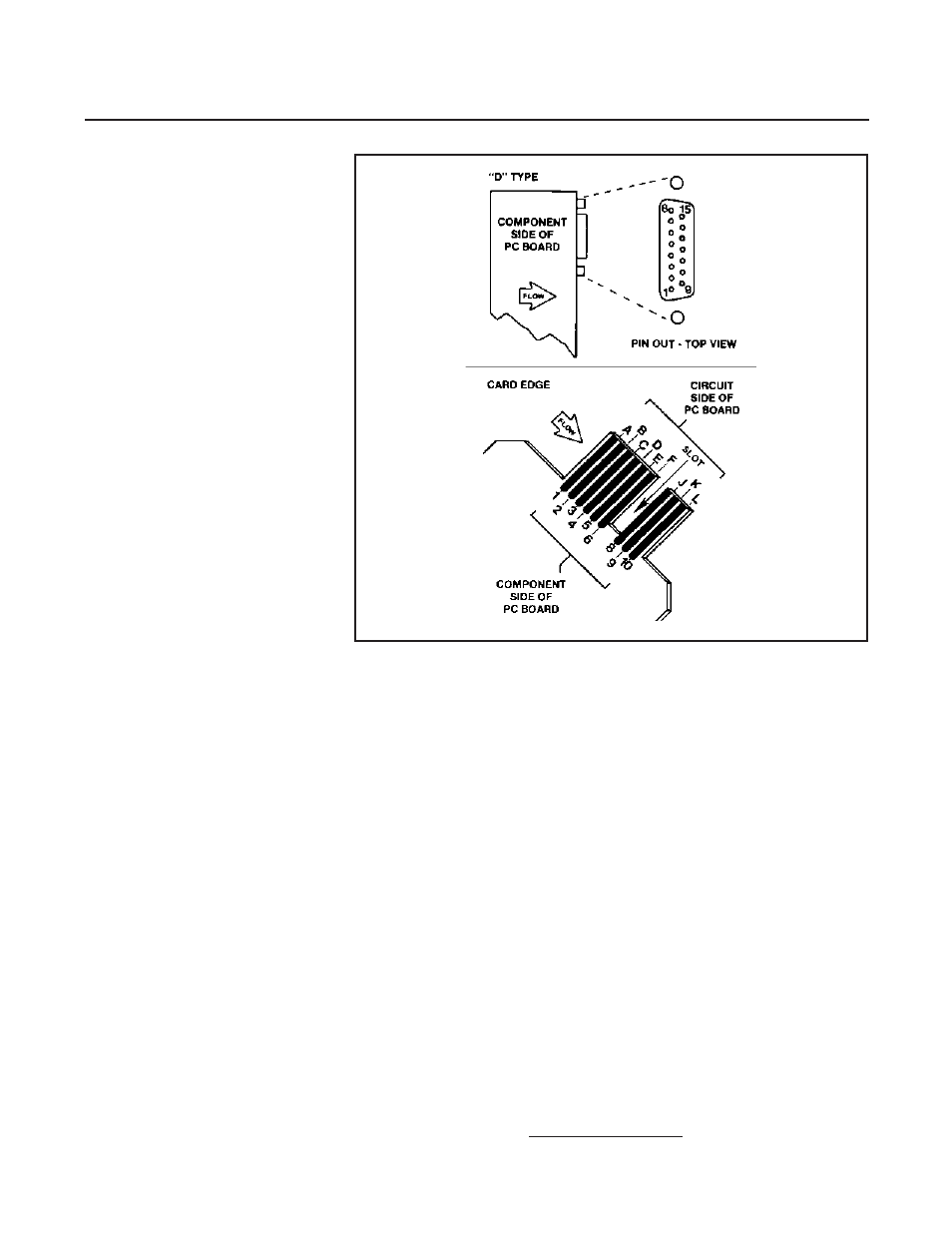
3-7
Brooks
®
Model 5851E
Section 3 Operation
Installation and Operation Manual
X-TMF-5851E-MFC-eng
Part Number: 541B104AAG
November, 2008
Figure 3-5 Model 5851E Calibration Connections
c. Connect the DVM positive lead to the 0-5 V signal output (Terminal 3
Card Edge, Pin 2 D-Connector) and the negative lead to signal com-
mon (TP4). Adjust the zero potentiometer for an output of 0 mV ±2 mV.
d. Apply pressure to the system and insure that the zero signal repeats
within 2 mV of the voltage set in Step c above. If the zero does not
repeat, check for leakage.
Note: Controllers supplied with all-metal valve seats do not provide tight
shut-off. A 0 to 3% leak through is typical. For metal seat controllers
close a downstream shut-off valve and observe the zero signal.
e. Set the command potentiometer (connected to Terminals A, B and 10
of the Card Edge connector and Terminals 8, 1 and 11 of the D-Con-
nector for 100% of flow (5.000 V). Connect the DVM positive lead to
TP2 (linearity voltage) and the negative lead to TP4 (signal common).
Adjust the linearity potentiometer for an output of 0.0 V (zero Volts).
f. Connect the DVM positive lead to TP1 (-100x sensor voltage) and the
negative lead to TP4 (circuit common). The command potentiometer
should still be set at 100% flow (5.000 V). Measure the flow rate using
suitable volumetric calibration equipment. To adjust the controller to the
proper full scale flow, calculate a new TP1 voltage using the following
equation.
measured TP1 voltage
New TP1 voltage=
x desired flow rate
measured flow rate