Crooked/wavy bead, Strike test, Excessive spatter – Harbor Freight Tools 55167 User Manual
Page 20: Porosity
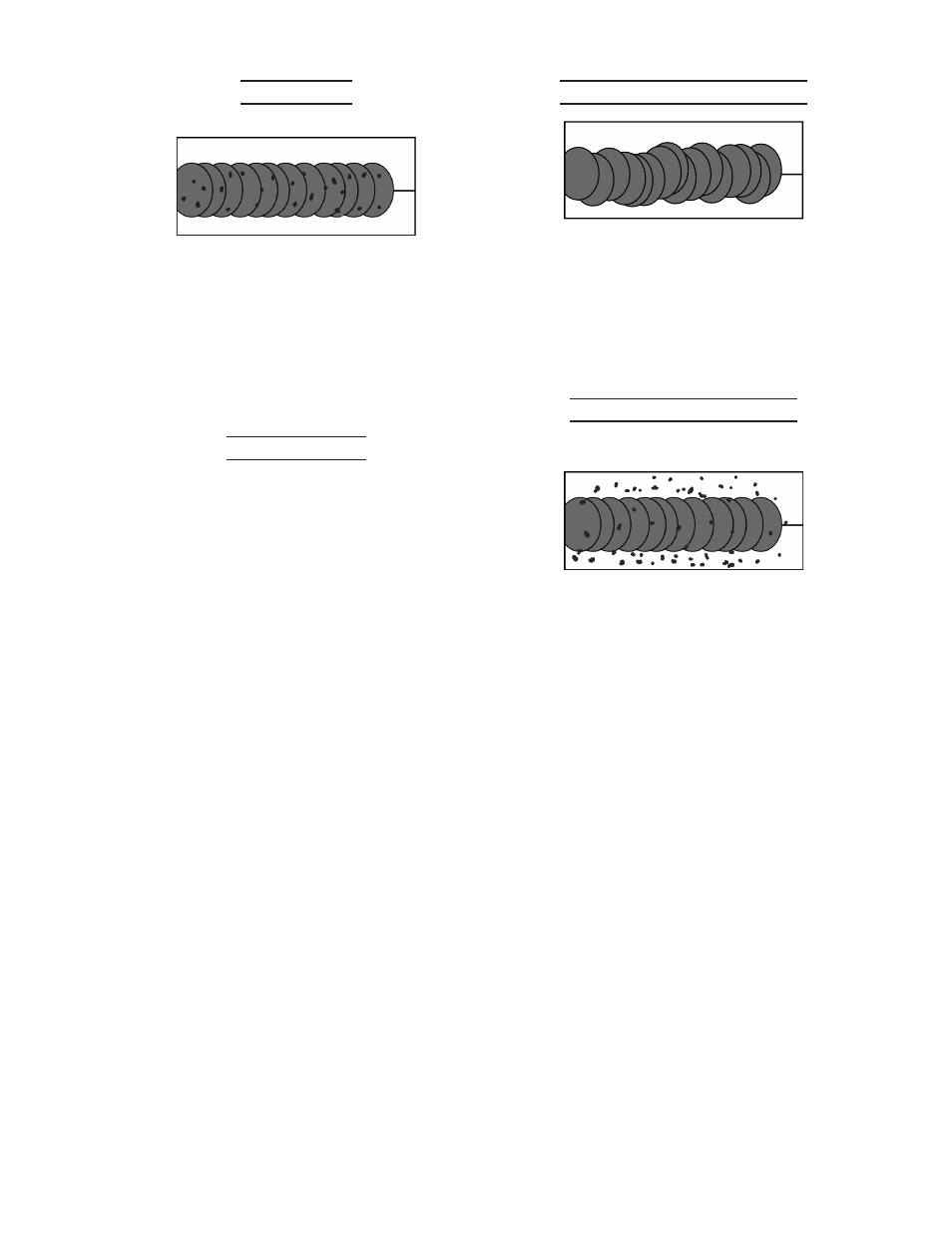
For technical questions, please call 1-800-444-3353;
Troubleshooting section at end of manual.
Page 20
SKU 55167
10.
When the weld is complete, lift the electrode wire clearly away from any grounded
object, set the Face Shield down, turn toward the Flux Wire Welder, and turn the Power
Switch to the OFF position.
11.
Unplug the Power Cord from the electrical outlet. Be sure to set the torch down
on a nonflammable, nonconductive surface.
12.
The Wire Brush/Hammer (39) can now be used to clean up the weld.
CAUTION: The weld may still be quite hot and sparks/chips may fly when cleaning.
Be certain to continue to wear ANSI approved safety goggles and protective wear
when cleaning a weld.
The Hammer can be used to knock off any excess spatter and to help knock down any
ridges. Be careful not to damage the weld or material when striking it.
The Wire Brush can then be used to help remove oxidation and some fine spatter.
CROOKED/WAVY BEAD
POSSIBLE CAUSES AND SOLUTIONS
1.
Stickout too long:
Reduce stickout.
2.
Inaccurate welding:
Use two hands or rest hand on steady
surface.
top
VIew
STRIKE TEST
A test weld on a PIECE OF SCRAP can be tested
by using the following procedure.
WEAR ANSI GOGGLES DURING THIS PROCEDURE.
1. After two scraps have been welded to-
gether and the weld has cooled, clamp one
scrap* in a sturdy vise.
2. Stay clear from underneath while you strike
the opposite scrap with a heavy hammer,
preferably a dead-blow hammer.
3. A good weld will deform but not break.
A poor weld will be brittle and snap at the
weld.
*This test WILL damage the weld it is performed
on. This test is ONLY an indicator of weld tech-
nique and is not intended to test working welds.
ExCESSIVE SPATTER
Spatter that is grainy and large.
Fine spatter is normal.
POSSIBLE CAUSES AND SOLUTIONS
1.
Wire feeding too fast:
Reduce wire feed speed.
2.
Stickout too long:
Reduce stickout.
3.
Dirty workpiece or welding wire:
Make certain that workpiece and wire are
both clean and free from oil, coatings, and
other residues.
top
VIew
POROSITY
Small cavities or holes in the bead.
POSSIBLE CAUSES AND SOLUTIONS
1.
Stickout too long:
Reduce stickout.
2.
Dirty workpiece or welding wire:
Make certain that workpiece and wire are
both clean and free from oil, coatings, and
other residues.
top
VIew