Field wiring, Check out and start up, Refrigerant charging instructions – Heatcraft Refrigeration Products H-IM-FL1A User Manual
Page 12
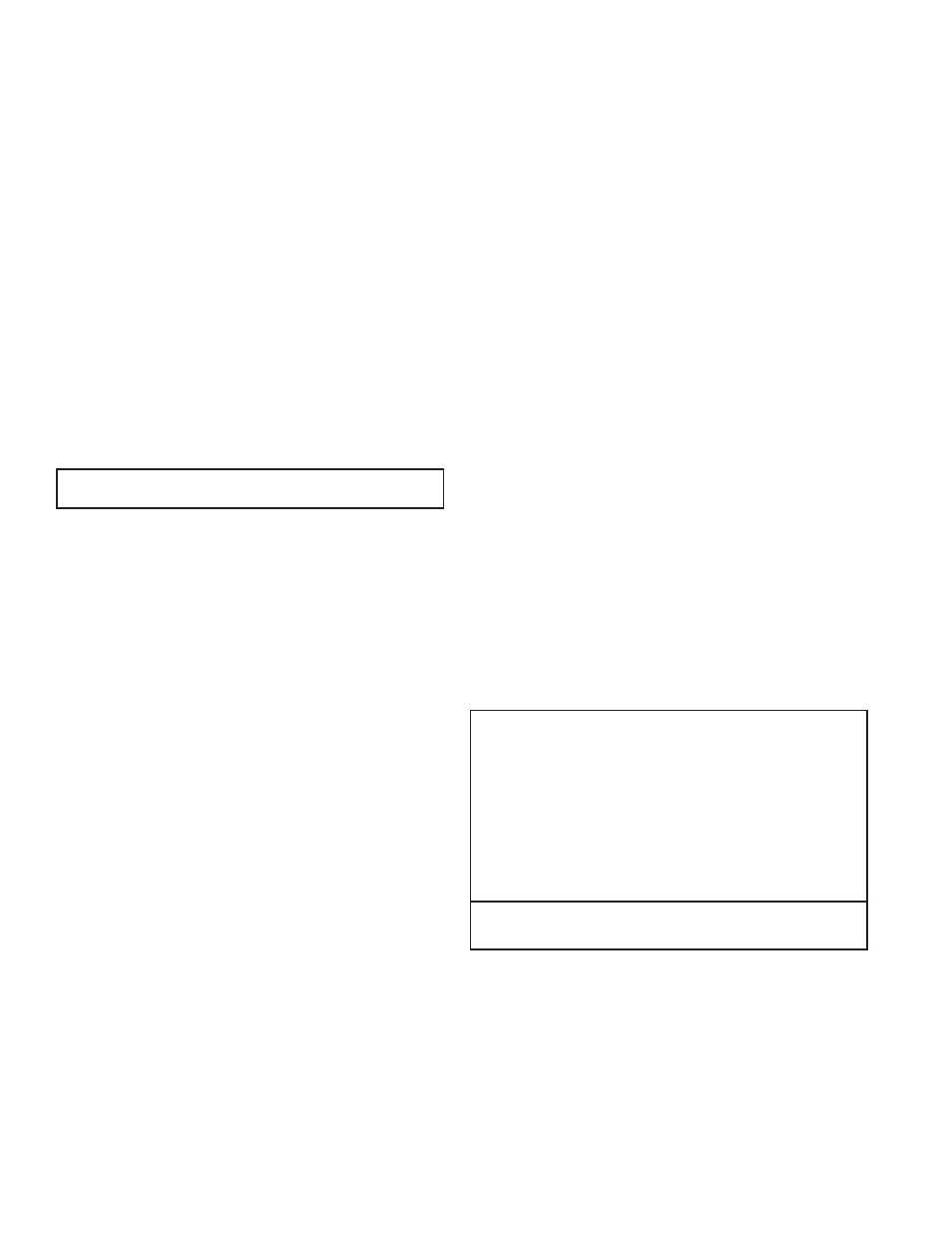
12
Field Wiring
WARNING: All wiring must be done in accordance with
applicable codes and local ordinances.
The field wiring should enter the areas as provided on the unit.
The wiring diagram for each unit is located on the inside of the
electrical panel door. All field wiring should be done in a profes-
sional manner and in accordance with all governing codes.
Before operating unit, double check all wiring connections,
including the factory terminals. Factory connections can vibrate
loose during shipment.
1. The nameplate on the unit is marked with the electrical
characteristic for wiring the unit.
2. Consult the wiring diagram in the unit cooler and in the
condensing unit for proper connections.
3. For air cooled condensers, due to multiple low amp motors,
we recommend using time delay fuse protection instead of
circuit breakers.
Check Out and Start Up
After the installation has been completed, the following points
should be covered before the system is placed in operation:
(a) Check all electrical and refrigerant connections. Be
sure they are all tight.
(b) Check high and low pressure controls, pressure
regulating valves, oil pressure safety controls, and all
other safety controls, and adjust if necessary.
(c) Check the room thermostat for normal operation
and adjust.
(d) Wiring diagrams, instruction bulletins, etc. attached
to the condensing units should be read and filed for
future reference.
(e) All fan motors on air cooled condensers, evaporators,
etc. should be checked for proper rotation. Fan motor
mounts should be carefully checked for tightness and
proper alignment.
(f) Electric and hot gas evaporator fan motors should be
temporarily wired for continuous operation until the room
temperature has stabilized.
(g) Observe system pressures during charging and initial
operation. Do not add oil while the system is short of
refrigerant unless oil level is dangerously low.
(h) Continue charging until system has sufficient refrigerant
for proper operation. Do not overcharge. Remember that
bubbles in a sight glass may be caused by a restriction
as well as a shortage of refrigerant.
(i) Do not leave unit unattended until the system has
reached normal operating conditions and the oil charge
has been properly adjusted to maintain the oil level at the
center of the sight glass.
CAUTION: Extreme care must be taken in starting compressors
for the first time after system charging. At this time,
all of the oil and most of the refrigerant might be in
the compressor creating a condition which could
cause compressor damage due to slugging.
Activating the crankcase heater for 24 hours prior
to start-up is required. If no crankcase heater is
present, then directing a 500 watt heat lamp or
other safe heat source on the lower shell of the
compressor for approximately thirty minutes will be
beneficial in eliminating this condition which might
never reoccur.
WARNING: Scroll compressor is directional dependent.
If noisy, change phase of input wiring.
Refrigerant Charging Instructions
1. Install a liquid line drier in the refrigerant supply line
between the service gauge and the liquid service port
of the receiver. This extra drier will insure that all refrigerant
supplied to the system is clean and dry.
2. When initially charging a system that is in a vacuum, liquid
refrigerant can be added directly into the receiver tank.
3. Check serial data tag attached to the unit for refrigerant
capacity. System refrigerant capacity is 90% of receiver
capacity. Do not add more refrigerant than the data tag
indicates. Weigh the refrigerant drum before charging so
an accurate record can be kept of the weight of refrigerant
put in the system.
4. Start the system and finish charging until the sight glass
indicates a full charge and the proper amount has been
weighed in. If the refrigerant must be added to the system
through the suction side of the compressor, charge in
vapor form only. Liquid charging must be done in the
high side only or with liquid metering devices to protect
the compressor.