Conveyor-style metal detector typical applications, About cassel metal detectors – Magnetic Products Metal Detectors for Meat, Poultry and Seafood User Manual
Page 3
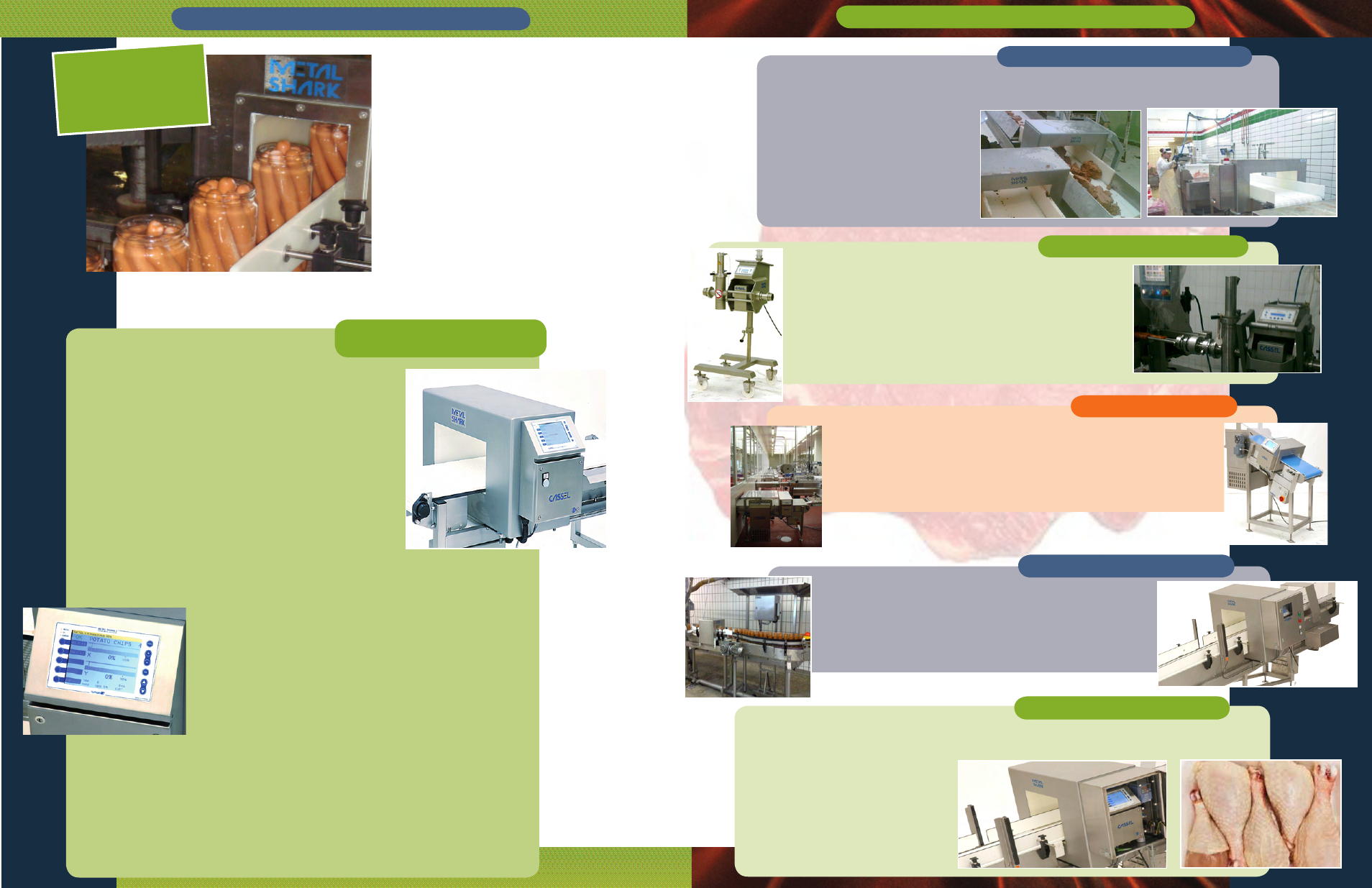
A Metal Detector identifies contaminants that have
a conductive quality (electrical conductivity or
electrical signal) differing from that of the product
being processed. A Metal Detector “reads” the
“signature” electronic signal of conductivity of
a product as it flows through a process. Each
product is catalogued as a specific “recipe”
of components. If the Metal Detector senses
something that falls outside of its programmed
recipe, an alarm is triggered. This tells the
operator that a foreign object is contained in that
product. The contaminated product can then be
removed and the source of the contamination can
be investigated.
METAL SHARK® BD (for Conveyor)
The Cassel′s METAL SHARK® BD Metal Detector is often used
to detect contaminants in meat, poultry and seafood. Typically
integrated onto a conveyor belt, the METAL SHARK® BD readily
adjusts settings to ensure extreme equipment sensitivity, stability
and reliability. A variety of reject mechanisms (pusher, belt stop
and alarm, etc.) are available to alert operators of a “find” or to
divert contaminated product. The conveyor belt, framing and
controls are available in sanitary design for food grade process
applications. Cassel Metal Detectors can be easily adjusted
to accommodate multi-system processing and environmental
product effect changes.
Features and benefits
HACCP and IFS compliance: Per HACCP principles, Metal Detectors are classified as
critical control points and continuous checking is required to meet standards. If requested,
Cassel can add a performance validation system (PVS) which automatically prompts the
operator to test Metal Detector performance at pre-set intervals.
Operational history: Metal contaminant detections, changes in
parameter settings and other events are recorded with the date and
time. Users can view the list of “incidents” on the control panel or
export the log via a serial port.
Ready for SHARKNET® software: To comply with HACCP and
IFS standards, SHARKNET® enables automatic downloading of
data documentation to a Windows-based PC.
LPW option for low pressure wash-up (IP66): To obtain the IP66 rating, the METAL
SHARK® controller can be housed in a double thick stainless steel enclosure. This upgrade
allow for wash-up with a non-pressure hose.
HPW option for high pressure wash-up (IP67): To obtain the IP67 rating, the aperture
can be specially sealed to prevent leaks and the METAL SHARK® controller can be housed
in a double thick stainless steel enclosure. Daily wash-ups with a steam hose at a maximum
pressure of 60 bar/900 psi can be conducted. Sausage processors as well as other
manufacturers who conduct frequent wash-ups have found this feature very beneficial.
Conveyor-style
Metal Detector
Typical applications
As raw materials arrive in the processing area, they must be examined for metal contaminants
(5 -10 mm) such as knife blades, metal gloves, meat hooks and others. Typically, a metal
detection system comprised of a Conveyor-
style Metal Detector with an upgraded HW
conveyor, and LPW or HPW option (see
column at left) would be selected. The HW
conveyor features an open stainless frame
without dirt traps, a waterproof stainless
drum motor, fully encapsulated sensor
head and an FDA/USDA-approved transfer
belt.
incoming raw material inspection
Cassel’s “IN MEAT” compact Metal Detector is designed for
sausage stuffers and is easily transportable via its wheeled-base.
An integrated gas spring provides for quick height adjustment
(33.5” - 47.2”), allowing installation between the stuffer and clip
machines. Links and adapters are available for nearly every type
of stuffer and clip machine. A variety of reject systems are offered.
sausage processing
Cassel has installed
over 5,000 Metal
Detectors worldwide
Cassel offers a variety of customized solutions for special applications such as an oversized “IN
MEAT” Metal Detector designed for shredding large pieces of pork. Cassel can also provide
automatic product selection to adjust for
product height. This is especially useful
for fresh meat packaged in styrofoam
trays which traditionally requires that the
Metal Detector be set to accommodate the
largest package. The Cassel option allows
the Metal Detector to adjust to various
product sizes, which means that sensitivity
remains consistent.
special applications
About Cassel Metal Detectors
A Conveyor-style Metal Detector with upgraded HW conveyor
would generally be installed after product passes through the roll
stock machine. Cassel offers a special flapping roller table that
moves contaminated product to a specified area without shutting
down production.
processed meats
A Conveyor-style Metal Detector with upgraded HW conveyor would generally
be installed on the production line after product passes through the roll stock
machine. Cassel offers a special flapping roller table that moves contaminated
product to a specified area without shutting down the Metal Detector.
packaged meats