0 trouble shooting guide continued, 3 power priming the high pressure pump, 4 connection of vacuum hoses – Sandia 12-Gallon, 1200 PSI Hard Surface Extractor User Manual
Page 13
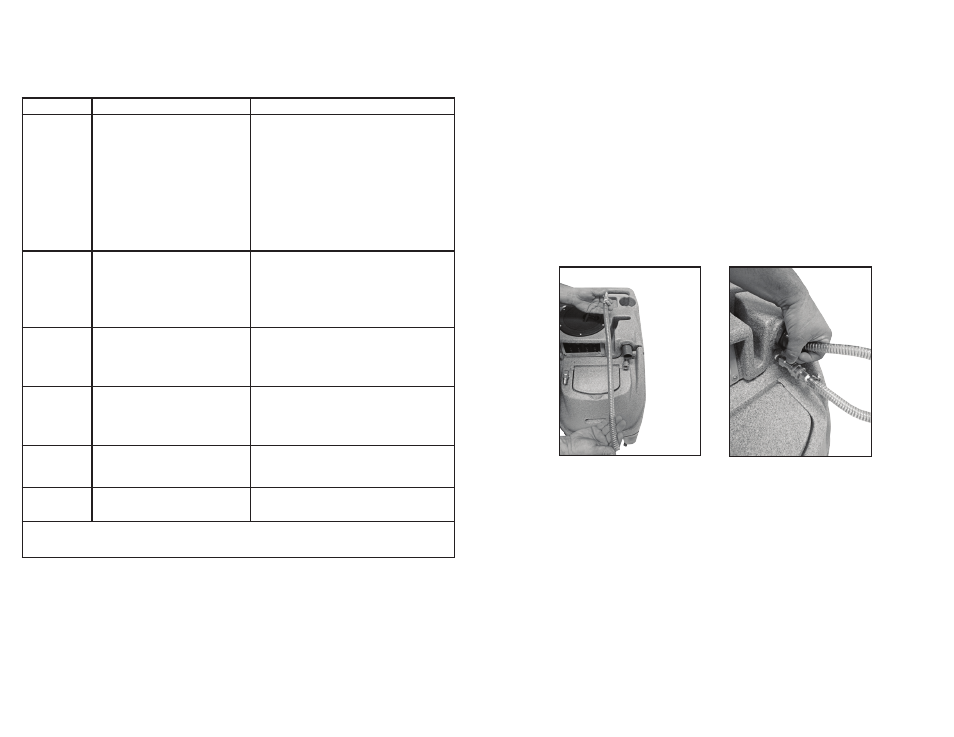
(28) 1200 PSI Hard Surface Extractor
1200 PSI Hard Surface Extractor (13)
4.3 Power Priming the High Pressure Pump
Once water is in the solution tank, the high pressure pump must be primed:
• Turn ON both vacuums then the solution pump. The vacuum will pull solution
through the pump and prime valve into the vacuum tank.
• Place the end of priming hose inside the vacuum hose barb.
• Cup a hand around the hose and barb to increase the vacuum suction on the hose.
When the pump is primed, you will hear the pulsation of the pump change.
• After priming, turn OFF the solution pump. If you have not yet connected your
solution hose or tool, you may have to relieve the pressure in the line so you can
connected your hose or tool.
If the pump still does not prime or if flow is low or unsteady, check the hose from the
solution tank to the pump (as well as the filter) for clogging, kinks or restrictions. Clean
or replace hose and/or filter and repeat the priming process.
If you are having trouble with the pump, refer to the “Trouble Shooting Guide” section or
contact your distributor for advice or assistance.
4.4 Connection of Vacuum Hoses
There are three (3) components used to connect the cleaning tool to the vacuums and
recovery tank:
1. 4-Foot Vacuum Hose: connected to the vacuum barb on the front of the machine and
to the outlet side of the clear view in-line filter.
2. Clear View In-Line Filter
3. 25-Foot Vacuum Hose: the 2” cuff on the 25-foot vacuum hose is connected to the
inlet side of the clear view in-line filter The other end with the 1-1/2” cuff is connected
to the cleaning tool.
When ready to being cleaning, turn both vacuum switches to the ON position. While
the Hard Surface Extractor can operate with only one (1) vacuum for cleaning delicate
fabrics, in most situations you will turn both vacuums switches to ON.
8.0 Trouble Shooting Guide Continued
Never operate the Hard Surface Extractor when the equipment is not performing as
expected or when any part is visibly damaged. When repair is needed, take the equipment
to an authorized service center.
Problem
Possible Cause
Remedy
Loss of Vacuum
1.
Vacuum motor faulty
2.
Vacuum motor gasket damaged
3.
Recovery tank lid gasket damaged
4.
Dump valve open
5.
Dump valve leaking
6.
Vacuum motor hoses loose/leaking
7.
Vacuum hose or tool clogged
8.
Vacuum hoses or cuffs leaking
9.
Recovery tank full
10.
Float shut-off filter clogged
11.
Ball stuck in float shut-off
12.
Auto-dump pump-out check valve
stuck open
13.
Recover tank damaged
1.
Replace vacuum motor
2.
Replace gasket
3.
Replace gasket
4.
Close valve
5.
Repair or replace dump valve
6.
Reconnect or replace vacuum motor hoses
7.
Clean out vacuum hoses and tool
8.
Replace vacuum hoses, cuffs and connectors as
needed
9.
Drain tank
10.
Clean float shut-off filter
11.
Repair or replace float shut-off
12.
Clean out or replace check valve
13.
Replace recovery tank
Chemical not
Feeding
1.
Solution tank not filling
2.
Chemical hose restricted
3.
Filter screen plugged
4.
Low incoming water pressure
5.
Wrong size metering tip
6.
Chemical proportioner faulty
7.
Check valve in filter faulty
1.
Check and repair auto fill assembly
2.
Un-kink, shorten, clean out or replace hose
3.
Clean or replace filter
4.
Set chemical bottle on top of machine – shorten
chemical hose – find other water source
5.
Change metering tip
6.
Replace chemical proportioner
7.
Replace filter
Tool won’t Spray
– Low or Uneven
Spray
1.
Jets clogged
2.
In-line filter clogged
3.
Jets worn
4.
Jets not aligned properly
5.
Tool valve faulty
6.
Quick disconnects or hoses restricted
1.
Clean out or replace jets
2.
Clean our or replace filter
3.
Replace jets
4.
Re-align jets
5.
Repair or replace valve
6.
Clean out or replace quick disconnects and/or hoses
Solution Tank not
Filling
1.
Water source turned off
2.
Float not on valve arm
3.
Float valve faulty
4.
Water hose restricted
5.
Quick disconnects faulty
1.
Turn on faucet or find other water source
2.
Reconnect float to valve arm – adjust to proper
height/level
3.
Repair or replace float valve
4.
Un-kink, clean out or replace hose
5.
Clean our or replace quick disconnects
Solution Tank
Overflowing
1.
Float too heavy/filled with water
2.
Float and chain tangled
3.
Float too high
4.
Float valve faulty
1.
Replace float
2.
Make sure float chain free and hanging properly
3.
Adjust chain to set float at proper level
4.
Repair or replace float valve
Chemical Jug
Filling with Water
– Overflowing
1.
Foot valve in filter stuck
2.
Foot valve in filter faulty
1.
Clean out foot valve and filter
2.
Replace foot valve and filter
To reduce the risk of fire, electrical shock or injury, repairs to wiring should only be performed by experienced service technicians. If
you are not experienced in checking electrical wiring, contact your nearest authorized service center to perform tests and repairs to
wiring and switches.
Contact your distributor for additional troubleshooting assistance, to order parts or for
advice and assistance in performing necessary repairs.