Fig.1, Fig.2, Introduction & specifications 3. preparation – Sealey SSC11003 User Manual
Page 3: Installation
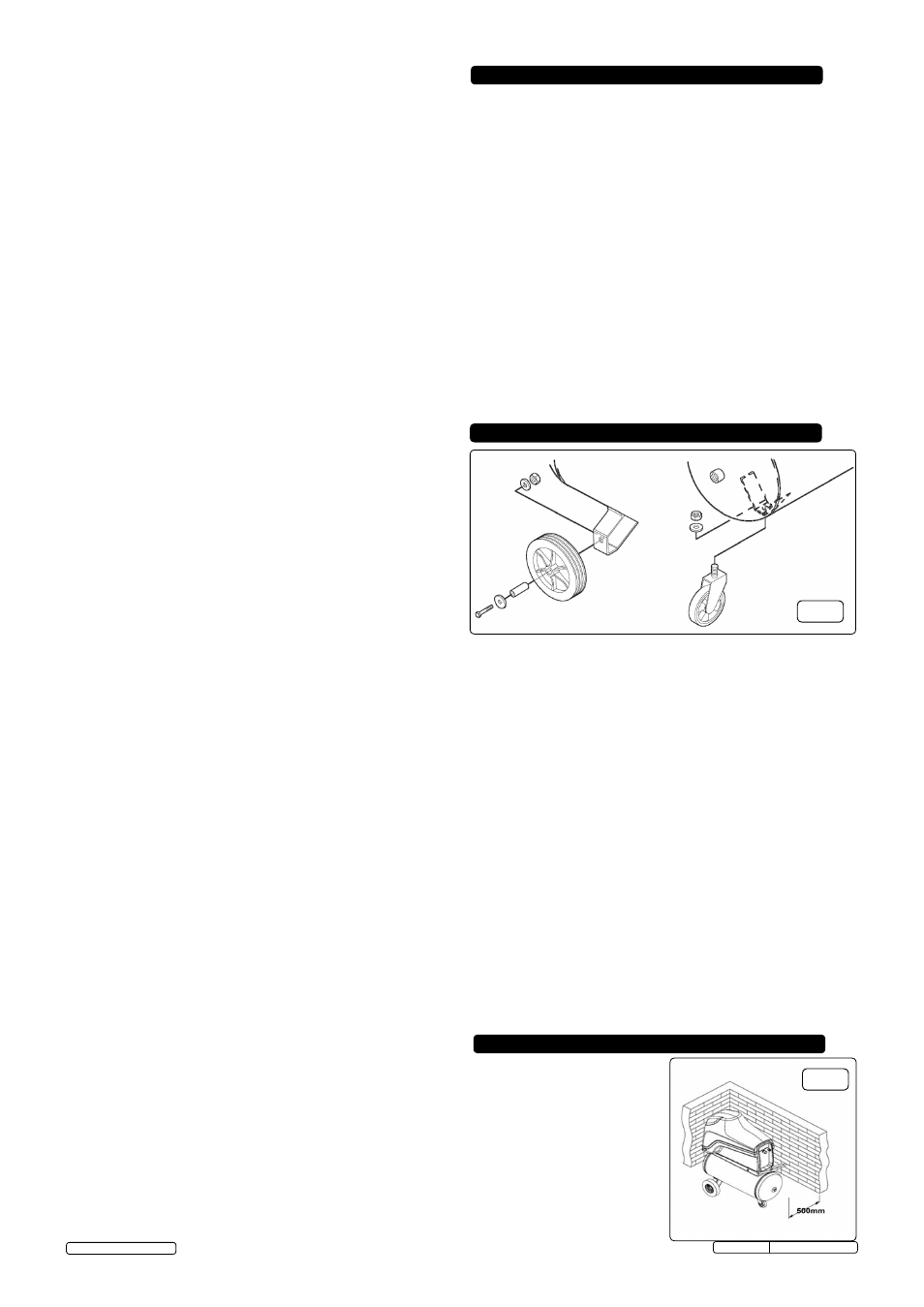
fig.1
2. INTRODUCTION & SPECIFICATIONS
3. PREPARATION
1.7. SAFETY (MAINTENANCE/PARTS).
WARNING! Compressor must only be serviced by an
authorised agent. DO NOT tamper with, or attempt to
adjust, pressure switch or safety valve.
3
sPArE PArts. use only original and identical spare parts to
replace worn or damaged ones. repairs must be made
exclusively by an authorised service agent.
3
mAIntEnAncE. regular maintenance of the compressor is
essential to ensure a long working life. follow the maintenance
schedule detailed in these instructions.
7
DO NOT disassemble compressor for any reason. the unit must
be checked by qualified personnel only.
3
dRAIN condensate from tank at least every week, inspect
inside walls for corrosion every three months and have a
detailed tank inspection carried out annually. Tank shell
must not fall below the certified thickness at any point.
3
When not in use, store the compressor carefully in a safe, dry,
childproof location.
3
KEEP tHE IntAKE GrILLs cLEAn. Keep the motor
ventilation grills clean. clean these grills regularly if the work
area is particularly dirty.
7
DO NOT cLEAn PLAstIc PArts usInG soLVEnts.
solvents such as petrol (gasoline) and thinners or other
compounds that contain hydrocarbons may damage the plastic
parts. clean them with a soft cloth and soapy water or other
suitable liquids.
3
usE orIGInAL sPArE PArts onLY. the use of non-original
spare parts will invalidate the warranty and could seriously
damage the compressor. original spare parts are available
from your local sealey dealer.
3 moVInG or mAIntAInInG tHE comPrEssor. Disconnect
the compressor from the electric power supply and completely
discharge the pressure from the tank before moving it or
carrying out any service, inspection, maintenance, cleaning,
replacing or inspection of parts.
WARNING! If an electrical fuse blows, ensure that it is
replaced with one of identical type and rating.
1.8. SAFETY (COMMON SENSE).
WARNINg: The warnings, cautions and instructions
discussed in this instruction manual cannot cover all
possible conditions and situations that may occur. It must
be understood that common sense and caution are factors
which cannot be built into this product, but must be
applied by the operator.
3
WArnInG. Pay attention to everything you do. use your
common sense.
DO NOT use the compressor if you are tired.
the compressor must never be used if you are under the
influence of alcohol, drugs or intoxicating medicines.
DANGER! DO NOT DIrEct tHE JEt of comPrEssED AIr
DIrEctLY toWArDs Your BoDY. to avoid all risks never
direct the jet of air towards other people or animals.
7
DO NOT stoP tHE comPrEssor BY PuLLInG on tHE
PoWEr suPPLY cABLE (unless in an emergency). use the
on/off buttons on the control panel to stop the compressor.
7
DO NOT moDIfY tHE comPrEssor In AnY WAY.
contact your local sealey dealer for all repairs required. Any
unauthorised modification may impair the efficiency of the
compressor and may also cause serious accidents for those
who do not have the technical skill required to make such
modifications.
3
WE rEsErVE tHE rIGHt to mAKE moDIfIcAtIons
WHErE nEcEssArY WItHout notIcE.
Original Language Version
compact high performance screw compressor providing high volume
and continuous output of air with low running costs. one of the most
economical ways to get compressed air 24/7 with minimal downtime.
Very few moving parts means servicing/maintenance is less frequent
and less expensive compared to equivalent piston compressor.
features an insulated class f 3hp motor with IP44 protected control
box and an insulated outer casing to minimise noise (59dB(A) at 1mtr)
and offers protection to inner components. All routine maintenance
functions are easily accessible and there is clear instrumentation
showing tank and line pressures separately. Also fitted with drain valve
tap at base of unit to ensure easy function tank drain when required.
Model No:. . . . . . . . . . . . . . . . . . . . . . . . . . . . . SSC11003
motor output: . . . . . . . . . . . . . . . . . . . . . . . . . . . . . . . . 3hp
Voltage/Phase: . . . . . . . . . . . . . . . . . . . . . . . . . 230V - 1ph
rated supply: . . . . . . . . . . . . . . . . . . . . . . . . . . . . . . . . 15A
noise Level: . . . . . . . . . . . . . . . . . . . . . . . . . . . . . 59dB(A)
maximum free Air Delivery: . . . . . . . .10.6cfm (300 ltr/min)
maximum Pressure: . . . . . . . . . . . . . . . . . . . . .131psi/9bar
receiver capacity: . . . . . . . . . . . . . . . . . . . . . . . . . . .100ltr
Dimensions (W x D x H):. . . . . . . . . . . 520 x 920 x1100mm
Weight: . . . . . . . . . . . . . . . . . . . . . . . . . . . . . . . . . . . . 88kg
Plug (not fitted):. . . . . . . . . . . . . . . . . . . . . . . . . . . . . . . 16A
3.1 remove compressor from packaging and inspect for any
shortages or damage. If anything is found to be missing or
damaged contact your supplier.
3.2 save the packing material for future transportation of the
compressor. We recommend that you store the packing in a
safe location, at least for the period of the guarantee. then, if
necessary, it will be easier to send the compressor to the
service centre.
3.3 Assemble the two fixed wheels and the castor wheel to the
SAC11003 as shown in fig.1.
3.4 confirm that the mains voltage corresponds with the voltage
shown on the compressor data plate.
3.5 site in a well ventilated place, protected against atmospheric
pollution and not in a place subject to explosion hazard. If the
surface is inclined and smooth, check if the compressor moves
while in operation – if it does, secure the wheels with two
wedges. If the surface is in a raised position, make sure it
cannot fall, securing it in a suitable way.
4. INSTALLATION
3.6. STORING THE PACKED AND UNPACKED COMPRESSOR.
.
If the compressor is not to be unpacked immediately store it in
a dry place at a temperature between +5°c and +40°c and
sheltered away from the weather. If the compressor is not
used immediately after unpacking it, place sheets over it to
protect it from dust, which may settle on the components.
the oil is to be replaced and the operational efficiency of the
compressor is to be checked if it is not used for long periods.
fig.2
4.1. to ensure good ventilation
and efficient cooling, the
compressor's air intake must
be at least 500mm from any
wall (fig.2)
ssc11003 Issue: 1 - 03/05/13
© Jack sealey Limited