Stem, disc & pin replacement, Packing, Motor replacement – Jordan Valve Mark 37 Series – Motor Operated Control Valve User Manual
Page 3: Seat adjustment, Trouble shooting
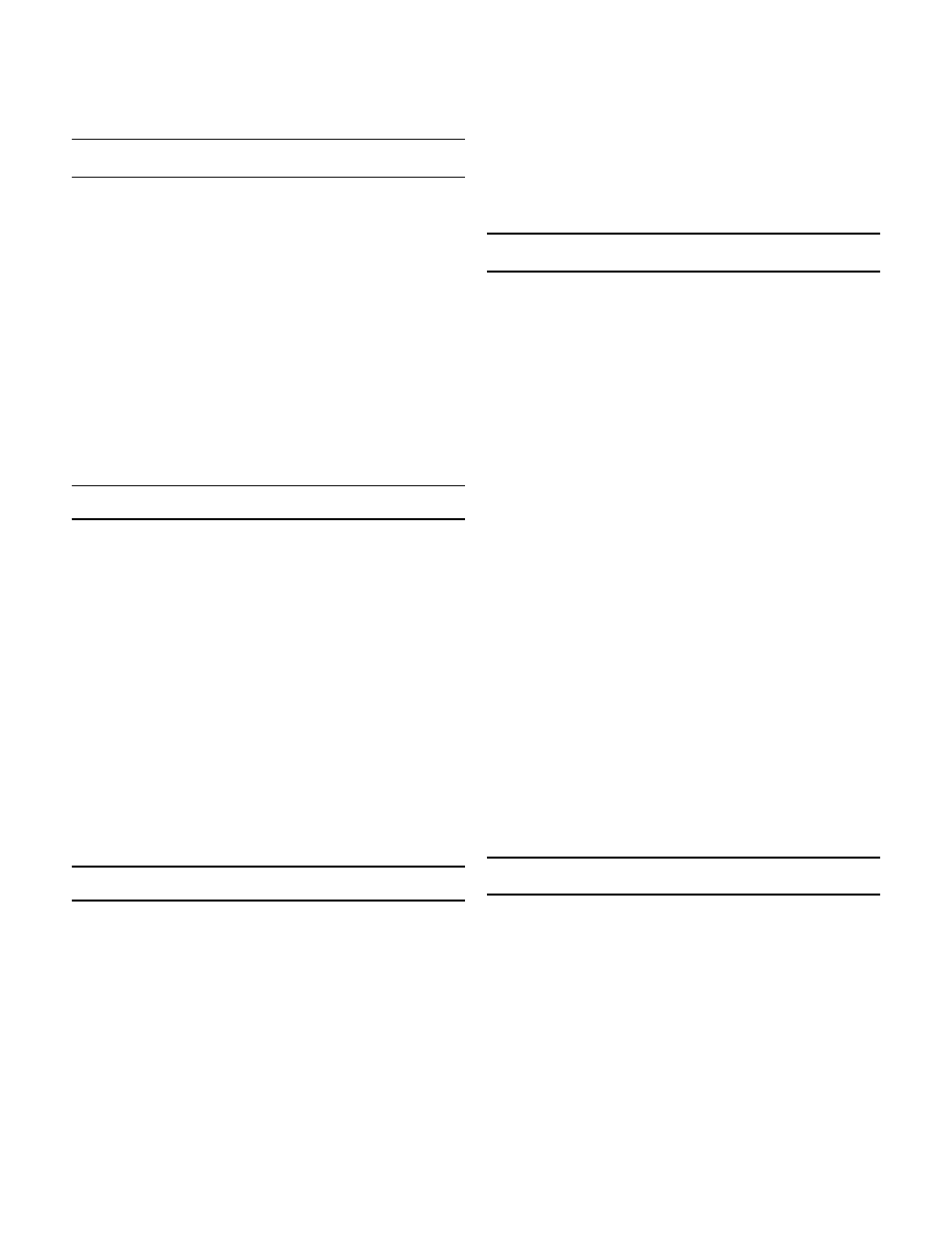
-3-
Install the nuts and cap bolts. Tighten uniformly.
5.
See back page for torque requirements and tight-
ening procedures.
Stem, Disc & Pin Replacement
Remove the valve disc and valve plate, following
1.
the procedure outlined under VALVE SEATS.
Remove motor following procedure outlined under
2.
MOTOR REPLACEMENT.
Loosen the lock nut and rotate the disc pin
3.
counterclockwise, pulling the valve stem upward
while doing so. Do not remove the valve stem
completely, but raise it sufficiently so that the
disc pin can be removed by pulling up and out. (If
replacing stem, remove packing first).
Reassemble the disc pin by threading it onto the
4.
stem until approximately half the thread length is
engaged in the disc pin.
Replace the motor assembly.
5.
Adjust the seats per SEAT ADJUSTMENT section.
6.
Packing
Remove the valve disc and plate following the pro-
1.
cedure outlined under VALVE SEATS.
Remove motor following procedure outlined under
2.
MOTOR REPLACEMENT.
Remove yoke by removing the set screws.
3.
Remove both packing flange nuts.
4.
Remove packing flange, packing follower, and
5.
packing.
Remove packing retainer and packing spring.
6.
Clean packing bore with solvent and blow out thor-
7.
oughly.
Assemble in reverse order and tighten packing nut
8.
so that the packing follower bottoms out on top of
the valve body.
Engage valve stem and actuator stem with connec-
9.
tor. Stroke adjustment is required as shown in SEAT
ADJUSTMENT.
Motor Replacement
Should a replacement motor be required, only a re-
placement motor from Jordan Valve can be used be-
cause they are factory set for the proper valve stroke.
The stroke is not field-adjustable.
Disconnect electrical power to valve, and relieve
1.
pressure in the valve. Caution: electric power must
be disconnected before wiring motor into circuit to
avoid electrical shock or possible damage to equip-
ment. Always disconnect power supply to motor
before attempting any wiring changes.
Remove the motor cover, mark the wires, and dis-
2.
connect wires from the motor.
Remove the valve from the line.
3.
Loosen stem connector lock nut.
4.
Loosen motor lock nut.
5.
Unscrew motor from yoke.
6.
Remove the valve seats (see VALVE SEATS section)
7.
to prevent damage to the seats while replacing
motor.
Adjust seats per SEAT ADJUSTMENT section.
8.
Seat Adjustment
Remove the seats per VALVE SEAT section and
1.
loosen the lock nut.
Rotate disc pin until it disengages from stem.
2.
For Direct Acting Valves (increase in signal closes
3.
seats): set command signal to minimum setting to
position motor at full up and limit switch tripped.
For Reverse Acting Valves (increase in signal opens
seats): set command signal to maximum setting to
position motor at full down and limit switch tripped.
Rotate disc pin onto stem until pin is at approxi-
4.
mate center position in body bore.
Replace the plate in the body seat recess with the
5.
index pin hole on the same side as the scribed
line on the body and with the disc pin protruding
through the center slot in the plate.
Place the valve disc on the plate, engaging the disc
6.
pin, and with the arrow stamped on the disc point-
ing to the scribed line on the body.
With stem connector nuts locked again the stem
7.
connector, rotate stem connector until plate and
disc slots are in perfect alignment.
Remove the seats and tighten the lock nut. Replace
8.
the seats.
Cycle the motor to closed position and back to
9.
open position. Recheck seat alignment and make
further adjustments as required.
After seats are properly aligned, replace disc guide
10.
and cap per VALVE SEATS section. Check to make
sure all bolts are tight.
Place valve back in service.
11.
Trouble Shooting
If You Experience Erratic Control:
Oversizing causes cycling and hunting, and reduc-
es the rangeability of the valve. Make certain that
your sizing is correct.
Steam traps downstream may require maintenance.
Safety valve may be defective and need repair.
There may be excessive foreign matter on the
seats, and seats should be removed and cleaned.
Valve stroke may need readjustment.
Valve disc may not be moving freely. Check disc
guide clearance and correct if needed.