Ion Science MiniPID User Manual
Page 11
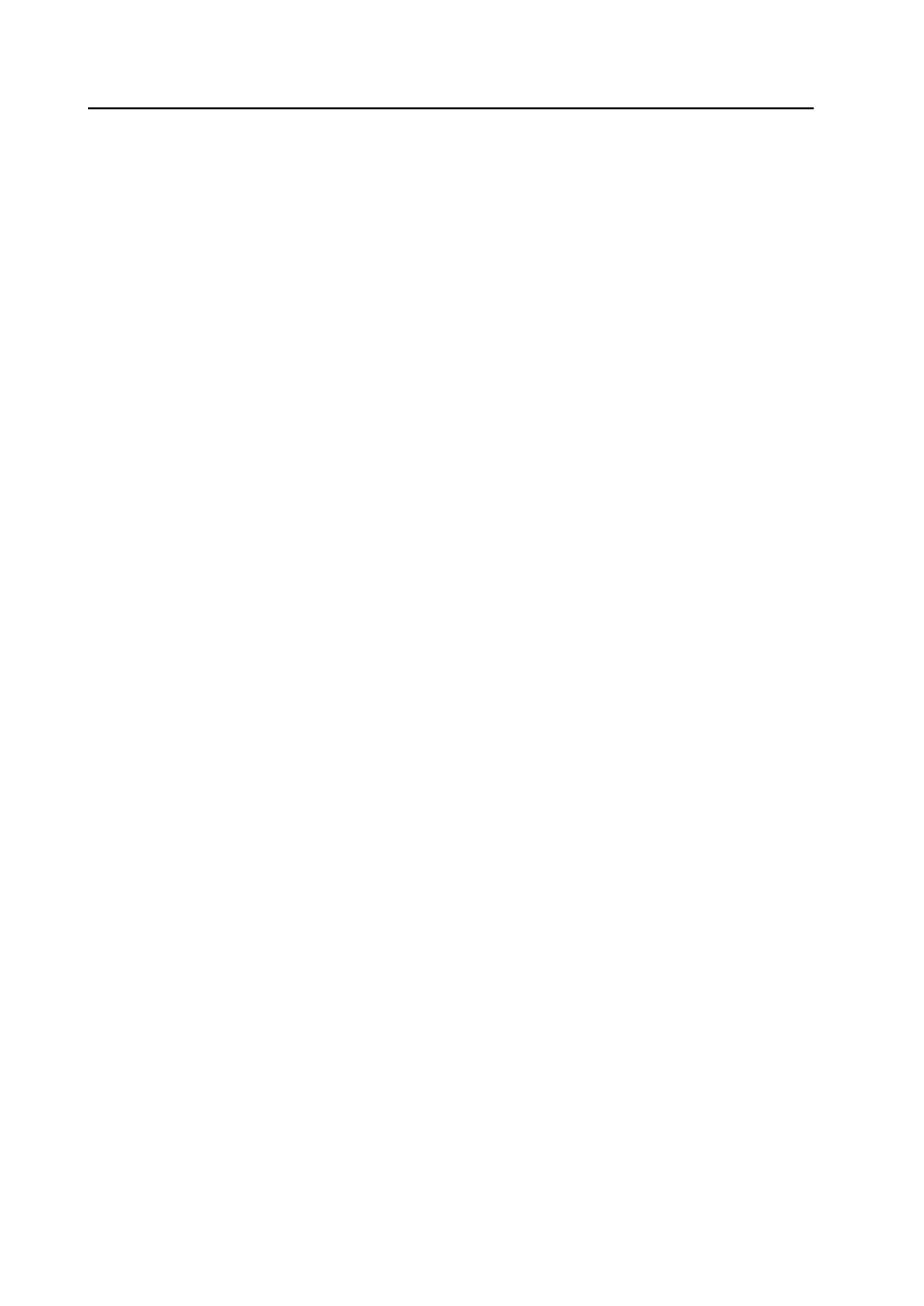
MINIPID 3PIN MANUAL
Ion Science Ltd
Page 11 of 27
Unrivalled Detection. www.ionscience.com
Instrument interfacing
– Best Practice
MiniPIDs have a very small sample volume, so this family of PIDs has fast response in both diffusion and
pumped gas modes. When designing the gasket between the PID and your gas sampling/diffusion access,
consider the following rules:
Diffusion mode is ideal for this sensor design.
Seal around the gas access port (with the white dust filter) using a gasket with an inner diameter of
6mm and an external diameter of 9.0mm. The inner diameter can be reduced to 4mm to further
increase response time, but careful alignment is required.
Use the correct sealing material: the gasket should be closed cell foam or moulded rubber which
does not adsorb the VOCs you will be measuring. Preferred materials are fluoroelastomers and
fluorosilicones (beware of outgassing if pellistors are nearby), but lower cost seals may be adequate.
Do not seal on the external diameter of the PID (20mm diameter). This gives water access to the
pellet electrode stack/ PID cell seal, encourages turbulence, increases gas volume (reducing
response time) and compresses the outside diameter of the PID, which is designed for compression
near the gas access, not at the external diameter.
Avoid pressure differentials. The PID allows clearance and gas access between the lamp and PID
cell, so if the sensing area above the cell is positively pressurised, then sampled gas will be forced
past the lamp, encouraging contaminant deposition on the outside of the lamp, reducing lamp
intensity and hence reducing sensitivity.
Since the gas access port is off-center and to avoid shear forces on the seal, do not seal using a
screw-down fitting which shears the gasket, but compress the gasket with a fitting and then use
screws to fix the fitting in place: keying of the fitting is good practice.
The white dust filter on the top of the PID allows maximum VOC access. If you will be operating in
atmospheres with high aerosol/ particulate concentration, then consider an additional filter.
For pumped systems (see page 10) flow rate should be 300 sccm (0.3 L/m). If there is no pressure
differential between ambient pressure and the pressure in the cell and the flow is across the sensor,
encouraging laminar flow, then flow rate can be increased to 500sccm (0.5 L/m).
If the pump is upstream of the PID, this will generate turbulent flow, which should be considered in
your design. Always try to achieve flow across the membrane to minimise shear velocity at the
membrane and maximise laminar flow.
Minimise the restriction between the PID and ambient gas.