Mp920 module configuration – Yaskawa MP900 User Manual
Page 6
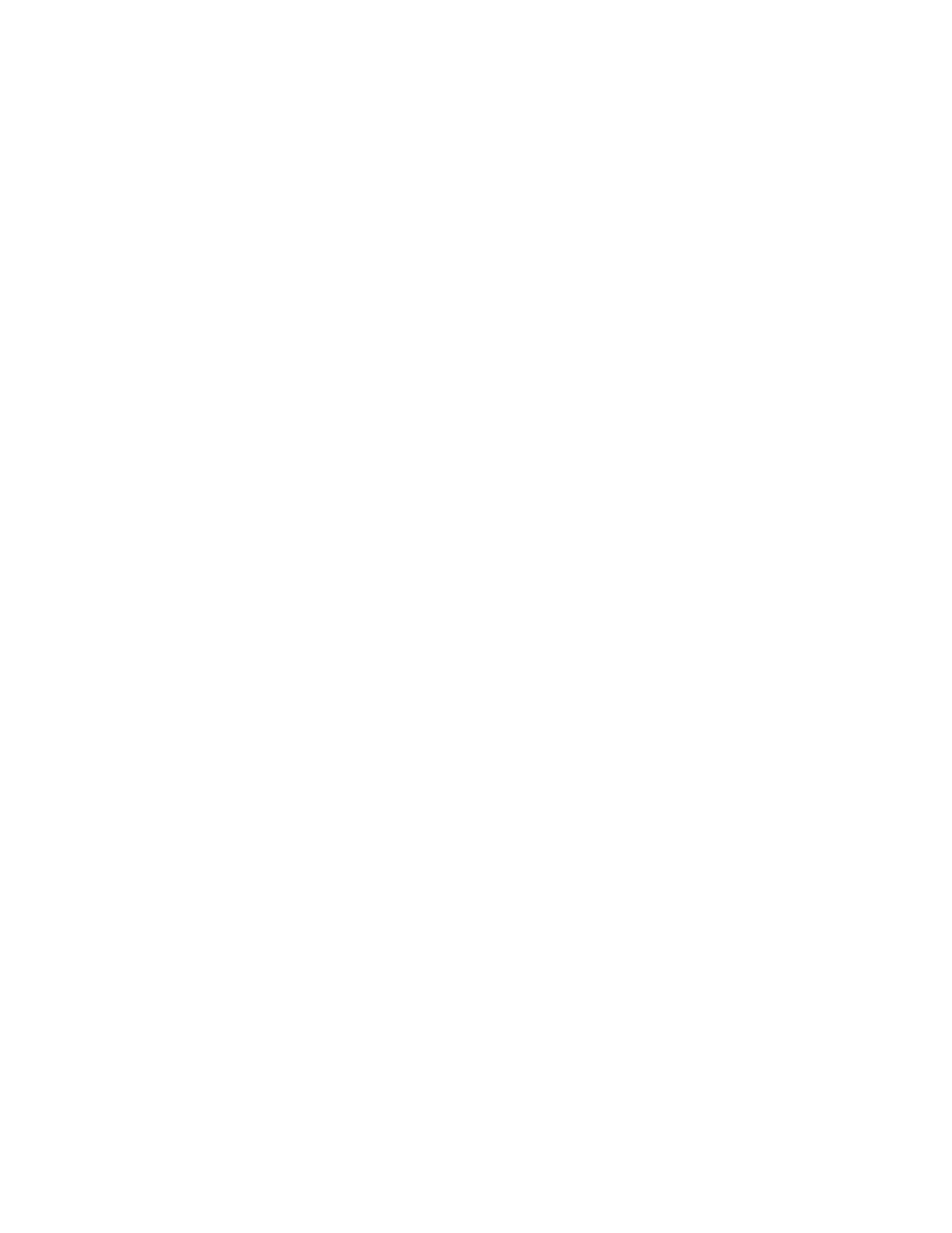
MP920 QRG Rev1.5
MP920 Module Configuration
In general, when you are prompted with "save ok" or "new file", just click OK.
Open Module configuration - maximize the window
Under Slot Number 00, select MP920 and click SAVE. The hardware will appear in the STATUS field according to the slot it is located at.
Setup SVB-01
Choose module type "SVB-01" at the corresponding slot number
Specify IO range: Use Memory Map conventions - start at 100
Double click "Mechatrolink" in Details field
Select "IO assignment" tab. Choose the correct hardware (type) according to its corresponding rotary
address switch (ST#), save and close
"Unsetting" appears in the SVB-01 Status. Save, cycle power, to clear. "Running" status appears
Open SVB - double click the SLOT NUMBER
Fixed Parameters Tab: Verify No.1, 3, 7. Save & Cycle power. Many of the other parameters only
apply when the programming unit is changed from encoder pulses.
SERVOPACK Tab: Edit Menu choose "default set" and save. Over-Travels ARE wired on the demo.
If they are not wired, disable them in Pn50A and Pn50B and cycle power.
Setup Parameters Tab: Turn on the servo with OWC001 to test the configuration. Don't save anything
here unless you want it to be the default on power-up. Use the Edit menu - Default Set and save to
restore defaults.
Monitor Tab: Look at "feedback position" (No. 9 in the list) and move motor by hand to verify motor
position
Repeat for each axis controlled by the SVB module. (select axis in upper left corner)
Setup LIO-01
Choose module type "LIO-01" at the corresponding slot number
Specify IO range: Use Memory Map conventions - start at 0
Open LIO - double click the SLOT NUMBER
Click "save" and the Current Value will update with the IO status. Test by monitoring inputs and
setting outputs from this screen.
Set Scan Time
Definition Folder - Scan time setting
High Scan setting = 2 ms, Low Scan settin = 30 ms
Save
Setup SVA
Connect cable from desired SVA output CNx to SDGH IO connecter CN1.
Wire overtravels or mask off with Pn50A.3 and Pn50B.0 using Digital Operator or SigmaWin+ & cycle power.
(On demo they are wired through the SVA cable)
Choose module type "SVA-01" at the corresponding slot number
Type a Circuit Number higher than any other SVA or SVB circuit
Save. "Unsetting" appears in SVA status. Save, cycle power and "running" status appears
Open SVA - doubleclick SLOT NUMBER
Check axis number and adjust according to number of connector used for servopack.
Fixed Parameters Tab: Check No.1, 3, 7. Many of the other parameters only apply when the
programming unit is changed from encoder pulses.
Setup Parameters Tab: Turn on the servo with OWC001 to test the configuration. Don't save anything
here unless you want it to be the default on power-up. Use the Edit menu - Default Set and save to
restore defaults.
Monitor Tab: Look at "feedback position" (No. 9 in the list) and move motor by hand to verify motor
position
Repeat for each axis under SVA control (select axis in upper left corner)
Power Off. Remove option card & clear A.E7 with Fn014. Reset parameters with Fn005 & cycle power. Absolute encoder unplugged will
produce A.81. Use Fn008, pressing ^(arrow) to select PGCL5 and press Mode/Set. Then cycle power to clear the A.81.
Page 6 of 15