Yaskawa 2Y25-0423.pdf User Manual
Page 11
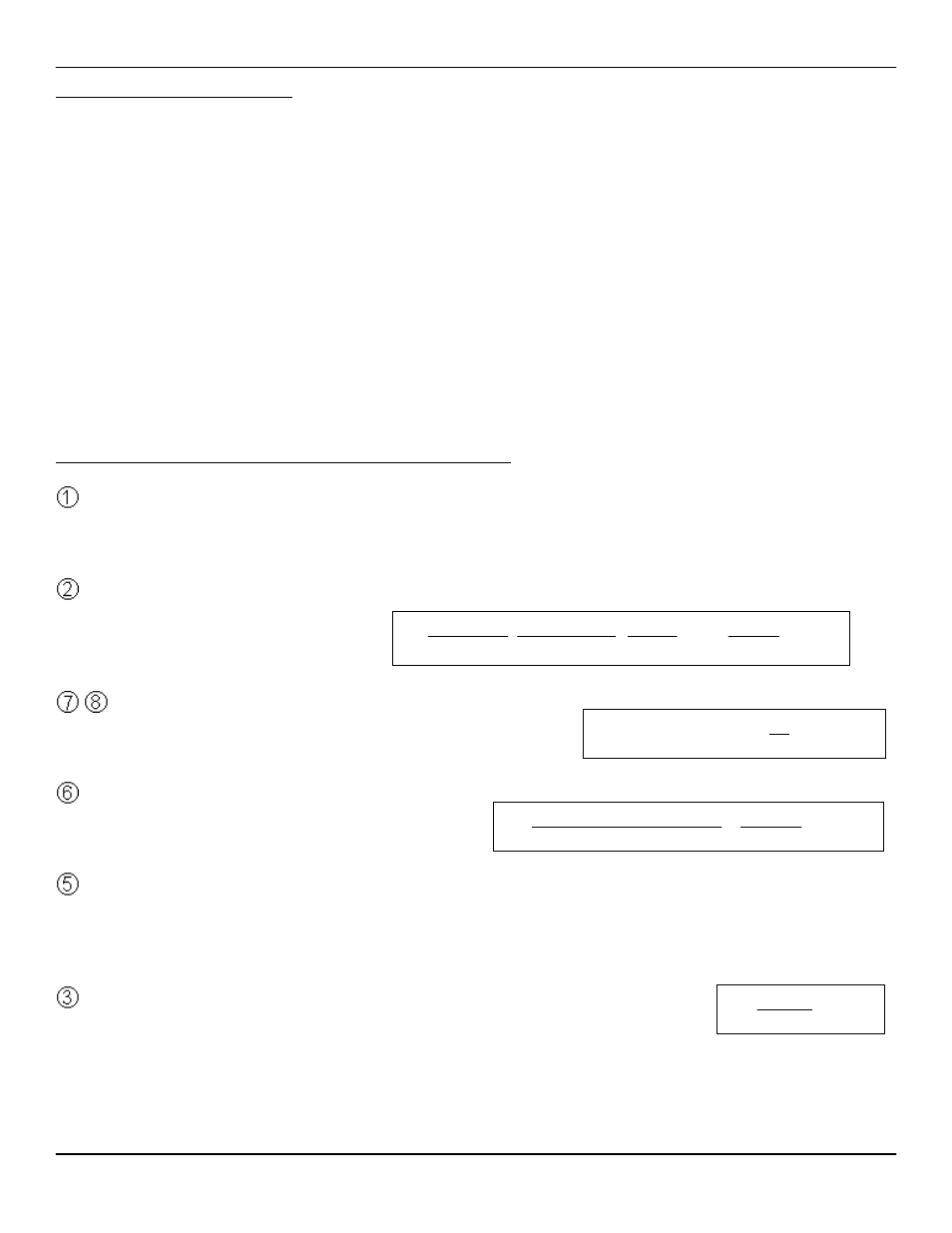
Rel. 09/15/2000 Page 11 of 13 Doc. No. 02Y00025-0423
PG-W2 Theory Of Operation
The PG-W2 card is a dual input encoder card. One input into the PG-W2 card can be used as a
frequency reference (terminals 10 - 13). The other input can be used as a speed feedback (terminals
3 - 6). There is one +12V power supply (terminals 1 and 2) capable of 200mA. Typically this power
supply can only provide enough current to power one encoder.
The frequency coming into the PG-W2 on terminals 10 - 13 is processed internally to come up with a
frequency reference. First, the incoming frequency is divided by 1000. Then it is multiplied by
parameter P1-01 then divided by parameter P1-02. The ratio of P1-01 over P1-02 is called the
frequency ratio. It allows the incoming frequency to be scaled to any application. Parameter P1-03
will increase or decrease the frequency reference by a set percentage.
In order to figure out the correct settings of P1-01 and P1-02, the frequency ratio needs to be
determined. When determining the frequency ratio, several pieces of information are required:
reference encoder speed (at a particular line speed), encoder output frequency, follower motor speed
(at a particular line speed), number of motor poles for the follower and follower motor frequency.
Determining Frequency Ratio For The Above Example (circled numbers correspond to
areas
in
the
above
drawing)
Encoder Speed:
The encoder attached to the line shaft turns one revolution for every widget produced. Therefore if
the line is running at 65 widgets / minute, the encoder is turning at 65 RPM.
Encoder output frequency (fe):
The encoder produces 360 pulses per
revolution. The encoder is turning at
65 RPM.
Motor Speed:
With a line speed of 65 widgets / minute, the output of the
gear reduction will be 65 RPM. The gear reduction is 25:1.
Motor Frequency:
Motor speed is 1625 RPM and there are four motor
poles
Frequency Reference:
If the GPD515 is in Flux Vector mode, Open Loop Vector Mode, or V/f with PG mode, or V/f mode
with slip comp enabled, the drive will automatically compensate for slip in the follower motor.
Therefore, calculated motor frequency should equal frequency reference.
Frequency Reference after encoder output frequency has been divided by
1000. Encoder frequency = 390Hz
fe
pulses
revolution
revolution
pulses
Hz
=
=
=
360
65
1
60
390
390
*
min
*
min
sec
sec
Motor Speed
RPM
RPM
=
=
65
25
1
1625
*
fm
motor poles motor RPM
Hz
=
=
=
*
*
.
120
4 1625
120
54 17
f
Hz
Hz
3
390
1000
0 39
=
= .