Mineral insulated heating cable – Thermon MIQ Mineral Insulated Heating Cable v.2 User Manual
Page 10
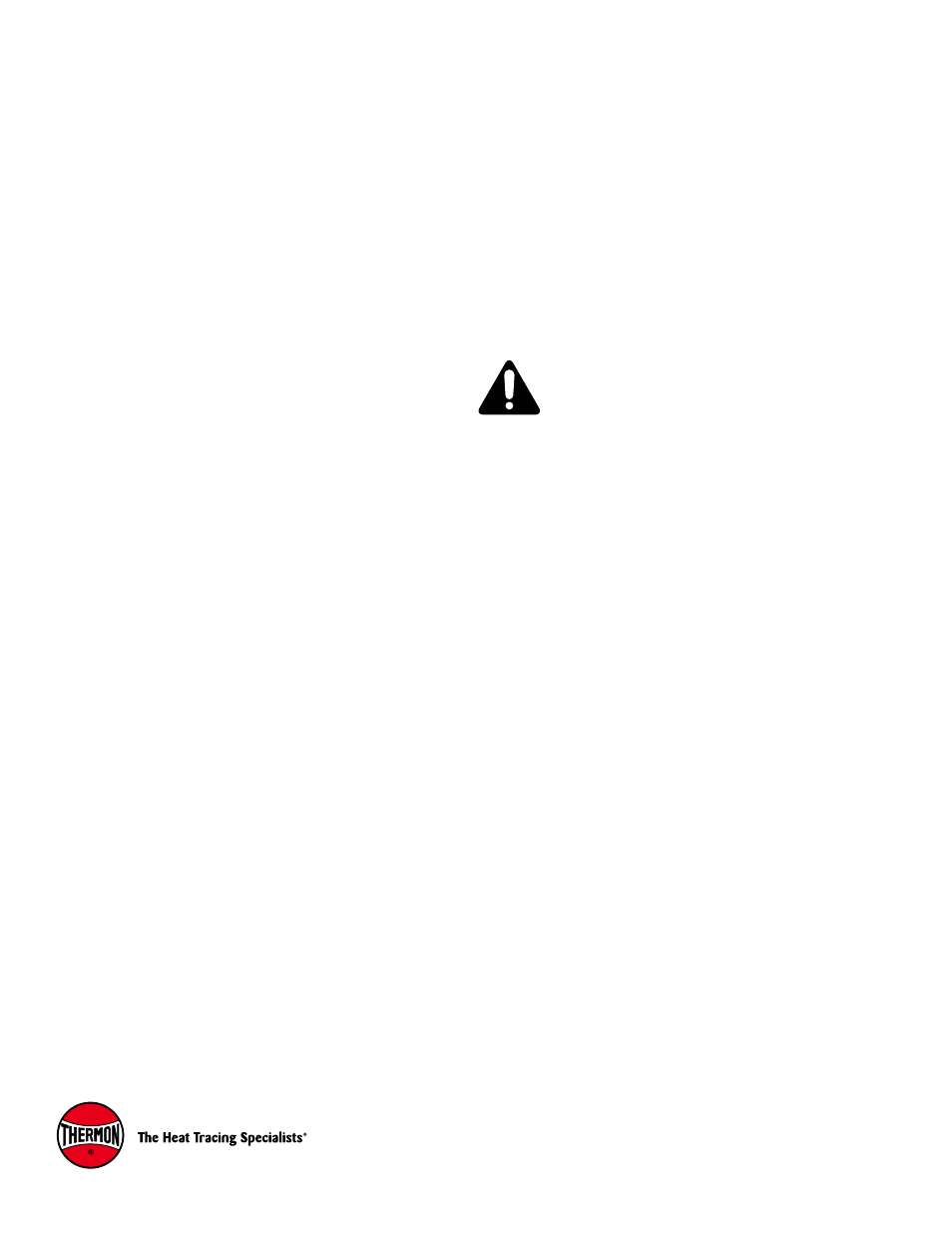
MIQ
TM
Mineral Insulated Heating Cable
Thermal Insulation . . .
1. The need for properly installed and well-maintained
thermal insulation cannot be overemphasized. Without
insulation, heat losses are generally too high to be offset
by a conventional heat tracing system.
2. In addition to piping and in-line equipment such as pumps
and valves, all heat sinks must be properly insulated. This
includes pipe supports, hangers, flanges and, in most
cases, valve bonnets.
3. Regardless of the type or thickness of insulation used, a
protective barrier should be installed. This protects the
insulation from moisture intrusion, physical damage and
helps ensure the proper performance of the heat tracing
system. Seal around all penetrations through the thermal
insulation.
4. After the installation of the thermal insulation and weather
barrier but BEFORE ENERGIZING THE HEATING CIRCUIT,
the megohmmeter test should be repeated. The measured
value should not be less than 5 megohms. This should
call attention to any damage to the heating cable that may
have occurred during the insulation installation.
5. Apply caution labels to insulation weather barrier at
required intervals along pipe.
The National Electric Code and Canadian Electrical
Code require ground-fault protection be provided
for branch circuits supplying electric heat tracing.
9
Final Inspection and Documentation . . .
1. It is recommended that the circuit be temporarily ener-
gized so that the volts, amps, pipe temperature and ambi-
ent temperature may be recorded. This information may
be of value for future reference and should be maintained
for the historical operating data log.
2. A sample historical operating data log form is included in
the Electric Heat Tracing Maintenance and Troubleshooting
Guide, Thermon Form TEP0066.