Electric heat tracing, Completing the installation – Thermon Electric Heat Tracing User Manual
Page 7
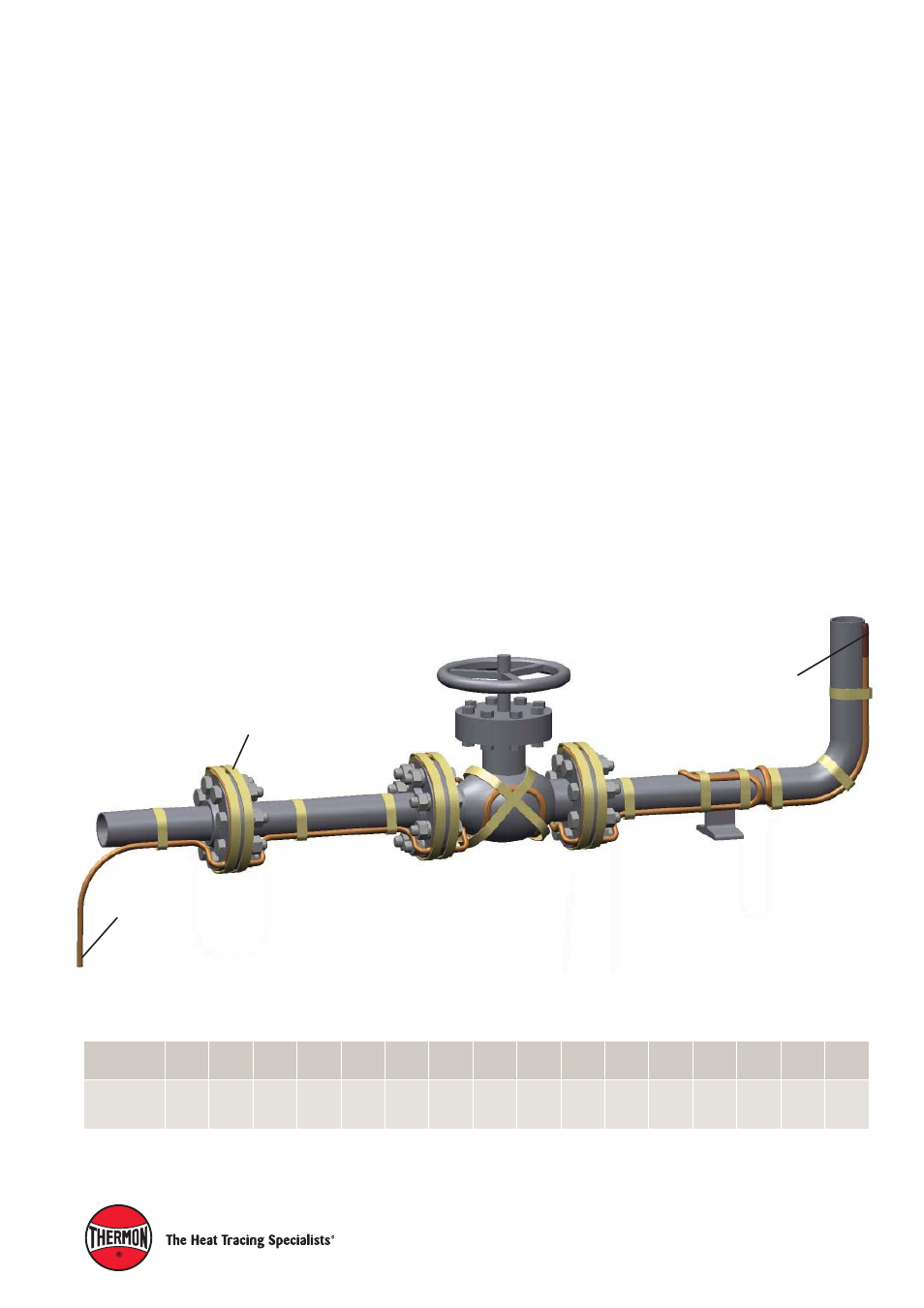
Electric Heat Tracing
6
Completing the Installation . . .
1. Begin fi nal cable attachment by securing the end-of-circuit
termination kit and working back toward the power supply.
Refer to Illustration I.
• Flexible heating cables are to be installed using attachment
tape. Circumferential bands of tape should be installed at
30 cm intervals to keep the cable in good contact with
the pipe. Refer to Table 2 below to calculate the number
of rolls of attachment tape required based on the pipe
diameter
1
.
• Avoid crossing series constant watt heating cables.
• If applicable, refer to installation details provided with
the project drawings or contact Thermon for additional
information regarding installation.
2. In addition to the circumferential tape requirements, a
continuous covering of aluminum foil tape may be required
when:
• Spray or foam
2
thermal insulation is applied.
• Heat tracing nonmetallic piping.
• Design requirements dictate the use of aluminum tape.
Table 2: Attachment Tape (Value Represents Approximate Linear Pipe Length Allowance Per Roll)
3. Complete splice connections (if required) in accordance with
the installation instructions provided with the splice kit.
4. Before making power connections, The heating cable
should be tested to ensure electrical integrity with at
least a 500 Vdc megger between the heating cable
bus wires and the heating cable metallic braid. IEEE
515 and EN-IEC 60079-30 recommend that the test
voltage for polymer insulated heating cables be 2500
Vdc. Minimum resistance should be 20 megohms.
(Record 2 on Insulation Resistance Test Page 9 and 10)
5. Install power connection kit in accordance to the detailed
installation instructions provided with the kit.
6. Secure temperature sensor (if required) to pipe utilizing
attachment tape.
Notes . . .
1. Table 2 assumes circumferential bands every 30 cm along the length of the process
piping.
2. Verify exposure temperature of heating cable versus curing temperature of
insulation.
Illustration I: Final Cable Attachment
Proposed End of Circuit
Attachment Tape
Proposed Power Supply
Pipe Size
mm
12-25
32
40
50
80
100
150
200
250
300
350
400
450
500
600
750
Length of Pipe/
Roll of Tape
m
109.7
79.2
67.0
54.9
45.7
36.6
27.4
21.3
18.2
15.2
12.2
10.7
9.1
7.6
6.0
4.6