TE Technology TC-24-10 User Manual
Page 9
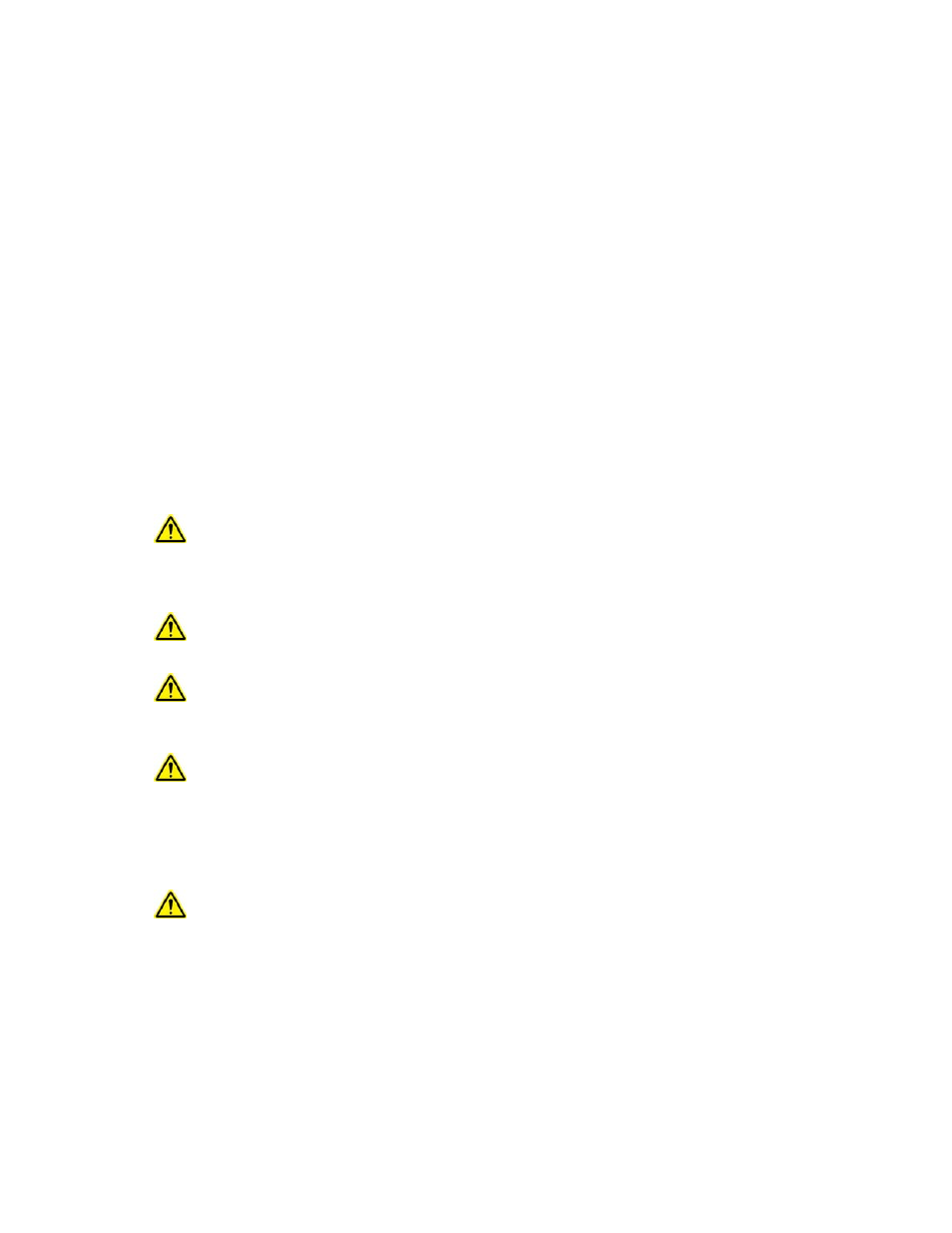
9
the region of the thermistor, making the temperature reading significantly less accurate and thermal
response time slower.
The TC‐24‐10 is supplied with the MP‐3238 thermistor. Other thermistor styles directly compatible with the
controller are available as options. See “Thermistor Styles for TC‐24‐10” for reference.
If you want to use a thermistor that has a different resistance‐temperature curve from the standard MP‐
3238 (See “Temperature versus Resistance for MP‐3238, MP‐2444, and MP‐2542 Thermistors” for
reference), it can be done as long as the operating resistance range is within that of the standard
thermistor. The thermistor must be a negative temperature coefficient device. Because the temperature
controller is really measuring the thermistor’s resistance and converting this to a temperature, the
temperature controller will be fooled into thinking that the thermistor is at a different temperature than it
really is, and the Set‐Temperature will be skewed accordingly. A loss of resolution and control stability may
occur as a result. The user assumes all risks associated with making any substitutions, and TE Technology
assumes no liability whatsoever for the operation of the controller when a non‐standard thermistor is used.
1.3
Connect the thermistor wire leads to WP3 and WP4.
1.4
The TC‐24‐10 can be used with two separate power supplies which allows for the control of TE devices
whose nominal operating voltage is less than 9 V. In this case, one power supply is for the TE device, and
the other power supply is for the controller itself (the microprocessor and associated electronics). Of
course, a single power supply can be used for powering both the controller and the TE device provided that
the TE device’s nominal operating voltage is ≥9 V and ≤26 V.
When using one power supply for powering the controller and the TE device together, the power
supply input voltage is passed directly through the controller to the TE device during the “ON”
pulse. The user should choose an input voltage that is required for the TE device and yet is also ≥9
V but ≤26 V. The controller could be damaged if operated outside this voltage range.
When using two power supplies, the controller input power supply must be ≥9 V and ≤26 V at 150
mA minimum current. The power supply input voltage for the TE device can be ≥0 V but ≤40 V.
The maximum allowable current through the controller is 10 A. The maximum allowable current
draw for the TE device must therefore also be less than 10 A. The 10 A limit applies regardless of
whether you are using one power supply or using two independent power supplies.
The controller does not have an internal fuse or circuitry to limit current. Therefore, an external
fuse, appropriately sized for protecting the controller/TE device, should be connected between the
power supply and the controller to prevent damage to the controller/TE device and to prevent
injury to the user should an over‐current condition occur. Alternately, a power supply with integral
over current protection can be used if it is appropriately sized for protecting the controller/TE
device.
When making a cooling system from a single TE device, the maximum operating voltage for that
system is usually no more than 75% of the rated Vmax of the TE module. The 75% rule is based on
the TE module being thermally connected to a “good” heat sink; system modeling should be done
to verify this rule is applicable though. If multiple TE modules are used in series or series‐parallel
combination, the Vmax of the system will be approximately 75% of the rated Vmax of each TE
module multiplied by the number of modules in series. Applying a voltage greater than the system
maximum will not necessarily damage the controller (unless voltage and/or current limits are
exceeded), but the TE device could be damaged by overheating as a result.