619 chemical cleanload installation instructions, Trouble shooting, Accessories – Smithco Spray Star 1750D (sn 175D180 – Current) Parts & Service Manual User Manual
Page 87
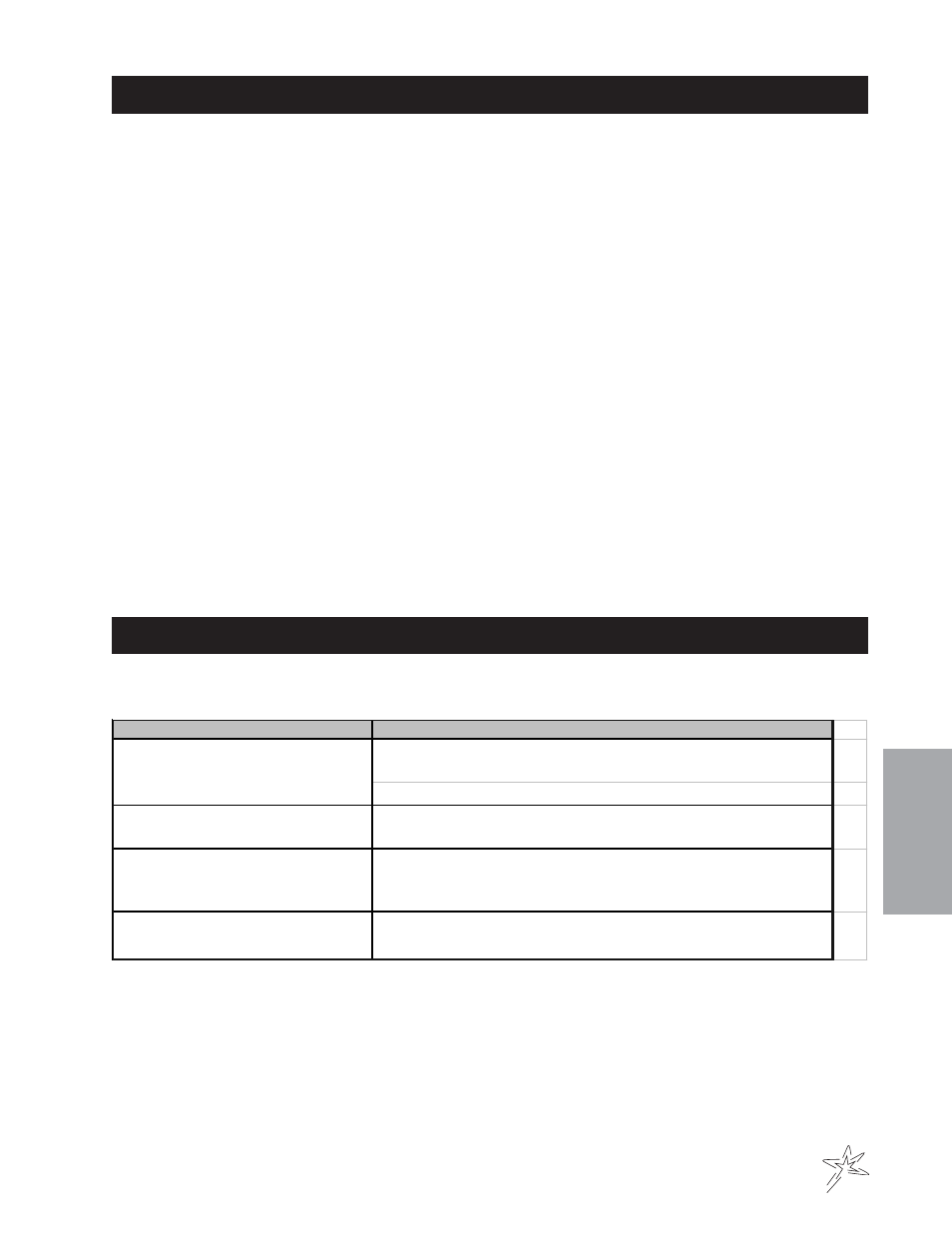
85
Accessories
15-619 CHEMICAL CLEANLOAD INSTALLATION INSTRUCTIONS
1. Make sure sprayer tank is empty and flush all chemical residue from sprayer. Always wear protective
clothing, goggles and gloves.
2. Remove plug from tee on spray pump (Ref A).
3. Install one of the 90° fittings, should point to the back of the machine.
4. Install 88" of 1
1
/
4
" discharge hose onto the elbow on the pump that points back and tighten hose clamp.
5. Route the 88" hose to the back of the sprayer so it connects over the top of the left boom support tube.
6. Install Mixer Mount (Ref 7) onto the left hand side of the center boom section. The Mount will slide over
the 2" tube under the actuator. Secure Mixer Mount with
3
/
8
x 3 bolt and lock nut. Tighten.
7. Mount Cleanload Assembly onto mixer mount using
5
/
16
x
3
/
4
flange bolts and flange nuts. Tighten.
8. Install 18-391 reducer coupling (Ref 4) onto outlet side. Then a 16-156 90° elbow (Ref 3) into the coupling
pointing up and one into valve with yellow handle. Tighten fittings so that the elbow in the valve is pointing
up and forward. The outlet fitting should be pointing up.
9. Remove the plug from the top back of the spray tank and install 16-972 45° fitting and 16-159 hose barb
and tighten. Now the 25" hose can be installed from the tank to the outlet fitting and tighten with clamps.
10. The hose from the spray pump can be connected to the inlet fitting and tightened with clamps.
11. Make sure all hardware, fittings and clamps are tight. Add about 25 gallons of water to the spray tank.
Start sprayer and circulate water through system to check for leaks.
12. Be sure to read start up, loading and shutdown instructions for Cleanload Assembly before using with
chemicals. When working with chemicals Always wear protective clothing, goggles and gloves.
TROUBLE SHOOTING
Symptom
Corrective Action
Check pump pressure and flow. Cleanload Eductor performance is based on
flow and pressure to the system. Note requirements for high eduction rates.
Increase outlet hose size back to tank.
Plugged or clogged bottle rinse nozzle
Disassemble rotary portion of nozzle from lower valve assembly and back
flush until nozzle ports are clear of debris.
Plugged or clogged tank rinse nozzle
Disassemble rotary portion of nozzle from NPT hose barb and back flush until
nozzle ports are clear of debris. Remove screen and flush with water to clear
away foreign material.
Fitting leaks
Check for cracks in fitting. Replace fitting if necessary. Disassemble and add
more joint seal in compound if leak occurs on threads.
Low eduction rate