MK Products Cobramatic 120VAC User Manual
Page 14
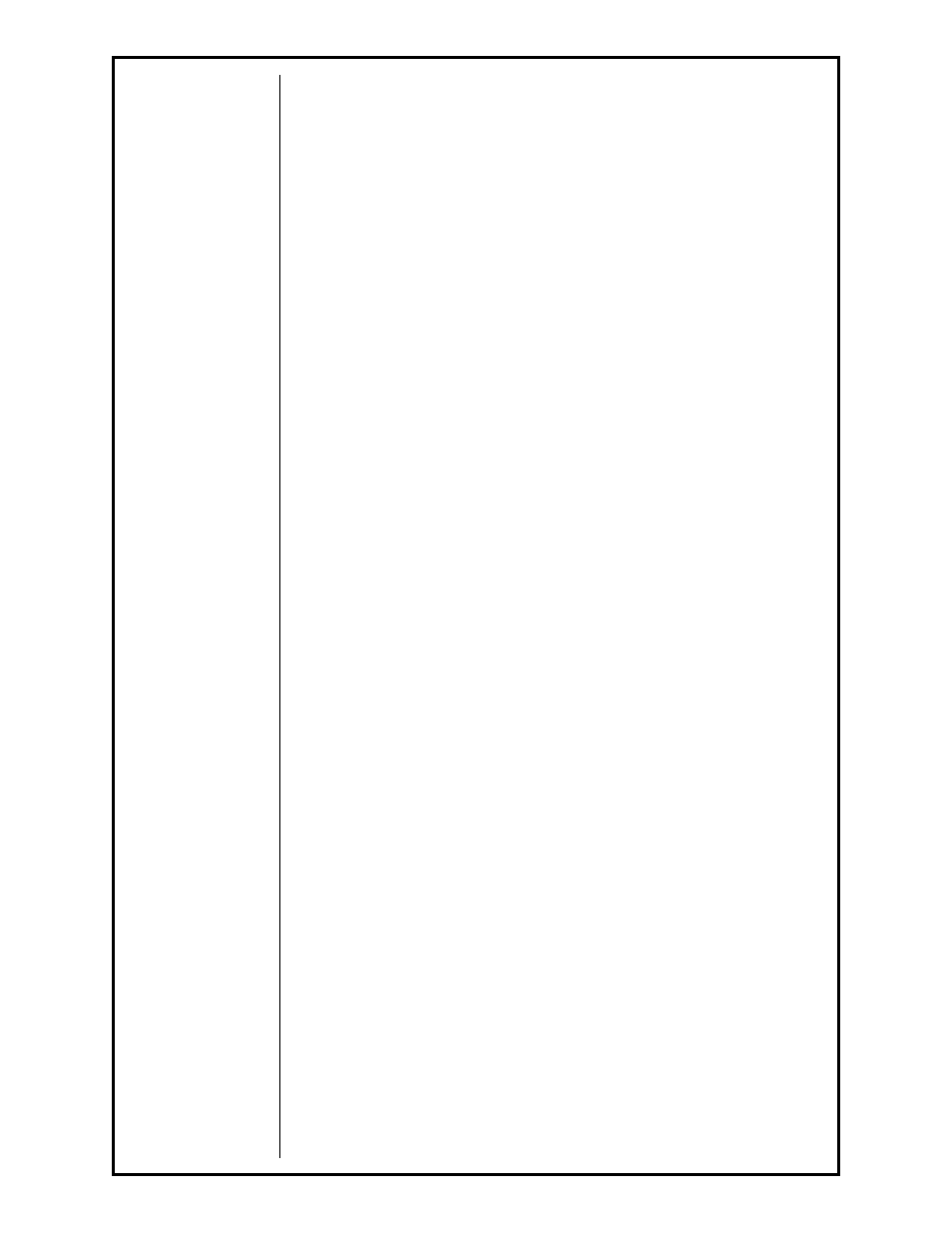
Cobramatic
®
Owner’s Manual - page 7
Section C
OPTIONAL KITS
The following is a list of Optional Kits available for the Cobramatic
®
Wire
Feeder.
A detailed description of each kit is given later in this section.
P/N Description
005-0316
8ft Interface Cable for Miller 14-Pin, 115VAC
005-0658
25ft Interface Cable for Miller 14-Pin, 115VAC
005-0608
8ft Interface Cable for Lincoln 14-Pin, 115VAC
005-0659
25ft Interface Cable for Lincoln 14-Pin, 115VAC
005-0674
Gas Purge/Trigger Latch Kit
005-0630
8ft Interface Cable for Thermal Arc 19-Pin, 1115VAC
005-0614
8ft Interface Cable for ESAB 19-Pin, 1115VAC
005-0316 8ft Interface Cable for Miller 14-Pin, 115VAC
005-0658 25ft Interface Cable for Miller 14-Pin, 115VAC
When properly connected, these interface cables will supply all the neces-
sary signals and power needed, from most Miller welding power supplies: a
Closing Contact signal and 115VAC input power.
005-0608 8ft Interface Cable for Lincoln 14-Pin, 115VAC
005-0659 25ft Interface Cable for Lincoln 14-Pin, 115VAC
When properly connected, these interface cables will supply all the neces-
sary signals and power needed, from most Lincoln Electric welding power
supplies: a Closing Contact signal, Posa-Start Voltage Sensing and 115VAC
input power.
005-0630 8ft Interface Cable for Thermal Arc 19-Pin, 1115VAC
When properly connected, these interface cables will supply all the neces-
sary signals and power needed, from most Miller welding power supplies: a
Closing Contact signal and 115VAC input power.
005-0614 8ft Interface Cable for ESAB 19-Pin, 1115VAC
When properly connected, these interface cables will supply all the neces-
sary signals and power needed, from most Lincoln Electric welding power
supplies: a Closing Contact signal, Posa-Start Voltage Sensing and 115VAC
input power.
005-0674 Gas Purge/Trigger Latch Kit
The Gas Purge/Trigger Latch Kit is a dual function kit. The kit includes an
easy to install interface control PC board, a 24VAC solenoid for pre and post
purge control, a modifi ed valve stem for the welding torch and, a front panel
switch for activating the Trigger Latch mechanism.
The gas control times have been preset to 0.5 seconds pre-purge and 1.0
seconds post-purge. This offers an optimum amount of inert gas shielding
prior to striking the arc and after the arc has been extinguished.
The Trigger Latch mechanism gives the operator the fl exibility of normal
trigger operation (pull trigger to weld - release trigger to stop). This also
offers the comfort of latched trigger operation (pull trigger once to latch and
weld - pull trigger again to unlatch and stop).
Section D
Maintenance
Routine Maintenance
Maintenance of the torch will normally consist of a general cleaning of the
wire guide system, including tubes, drive rolls, and conduits at regular inter-
vals.