Technical specifications, Figure 1, Figure 2 – MK Products DiamondBack Weldhead User Manual
Page 9
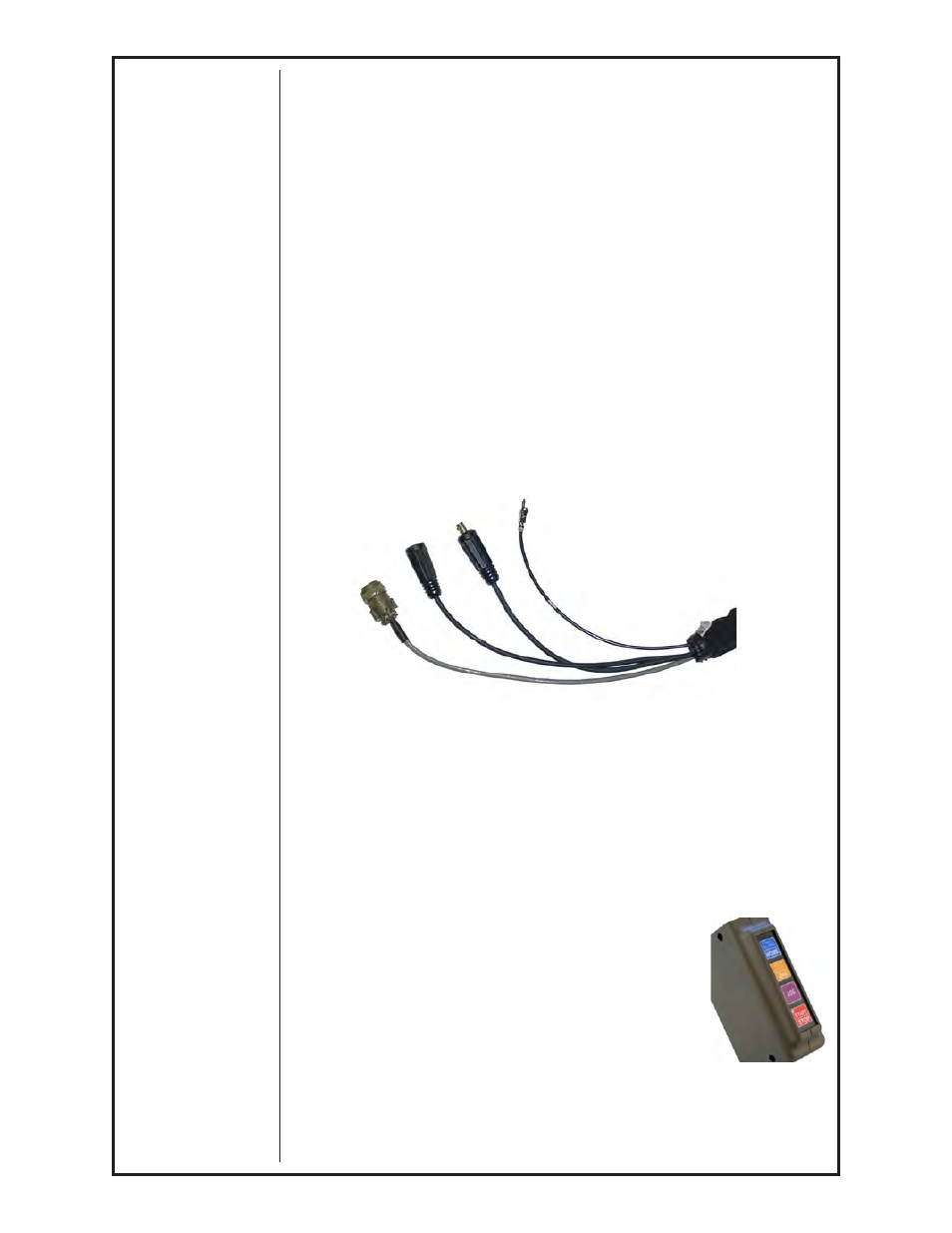
DiamondBack
™
Owner’s Manual - Page 1
Section A
Installation
Technical Specifications
The DiamondBack™ weldhead was designed for process piping and
manufacturing work-cell applications. The DiamondBack™ weldhead is
capable of welding 2” Tube OD to 6” Nominal Pipe and associated fittings.
Electrical
The DiamondBack™ uses a 24VDC motor with TACH feedback. It is
controlled by an orbital power-supply motor-control circuit to turn the rotor at
the precise speed to create a near perfect weld.
Mechanical
Power Cable Size: .................. #6, 75A, 600V.
Twist-lock cable-end connectors.
Gas/Water Hose Size: ............ Nylon Tube, ¼” OD x 0.17 ID
Double-end shut-off coupler
Control Cable Specification: ...20AWG, 12 conductor
Weldhead Connections
The DiamondBack™ comes equipped with an integrated 25 foot cable, which
connects to the CobraTig
®
150 orbital power-supply. The cable assembly
provides a path for weld power, operator control and motor signals and inert
gas flow (see Figure 1).
Figure 1
Connecting to the CobraTig
®
150
The DiamondBack™ connects directly to the CobraTig
®
150 orbital power
supply.
Welding Leads
The two welding Power Leads use a twist-lock type of power connector.
These are designed to attach directly to the rear panel of the CobraTig
®
150.
The male connector connects to the receptacle labeled “ELECTRODE”. The
female connector connects to the receptacle labeled “GROUND”.
Control Cable
The 24 MS-type pin connector attaches to the mating
receptacle on the rear panel of the orbital welding power-
supply. All of the Control, Feedback and Welding functions
of the weldhead transfer through this connector.
The operator controls are on the weldhead handle. They
include: JOG, GAS/NEXT LEVEL, FINAL SLOPE and
START/STOP (Figure 2).
Gas Hose
The gas connector is a double-end shut-off type valve that prevents flow or
leakage out of either the unit or the gas hose if the connection is broken.
The gas hose connector from the weldhead plugs into the “GAS OUT”
receptacle.
Figure 2