MK Products DiamondBack Weldhead User Manual
Page 12
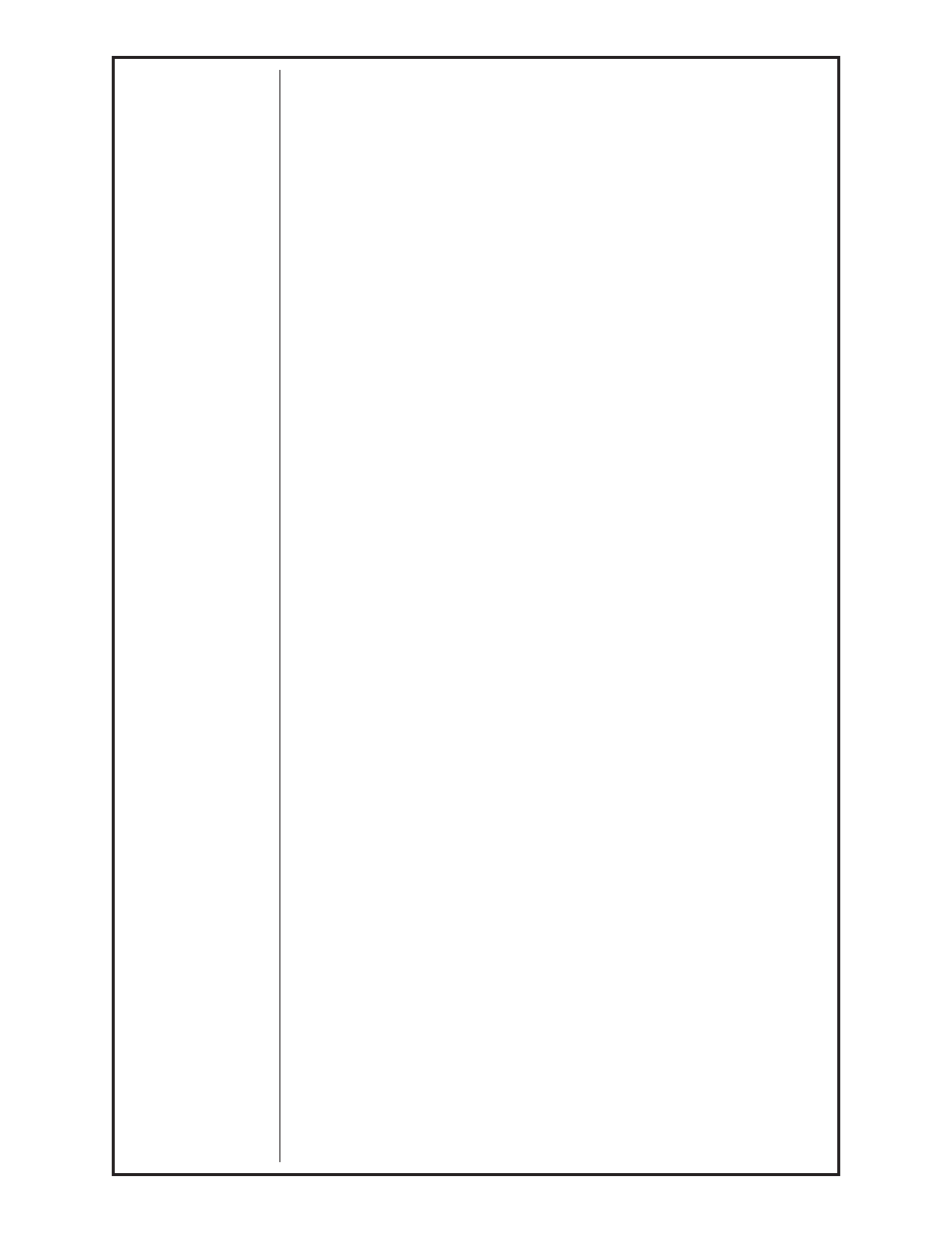
DiamondBack
™
Owner’s Manual - Page 4
Recommended Arc Gap
The proper arc gap is an important part of the proper use of your orbital
welding equipment. Improper arc gap can cause arc strikes to occur to your
Collets.
Be sure the arc gap is as short as possible, consistent with the process and
weld current level, but not so short as to ‘crash’ or touch the weld being
made.
If no arc gap is known when designing a weld procedure a good rule-of-
thumb is as follows:
Work Cell Apps: (Wall Thickness x 0.5) + 0.010”.
Field Apps: Match Arc Gap to Wall Thickness, up to max. gap of .070”*
* Some applications may require variance on this dimension depending
on pipe concentricity and ovality.
CAUTION
Do not over-tighten the tungsten set screw. Over-tightening the setscrew can
crack and splinter the tungsten causing errant starts and arc wander.
Be sure that the tungsten does not extend into the rotor teeth and that both
setscrews are flush with the rotors surface.
Any length of tungsten that is protruding out the back of the rotor will jam
with the meshing gears inside the weldhead. This will push the tungsten into
the weld being made and inevitably cause either an ARC FAULT or MOTOR
FAULT, or worse.
If the weldhead becomes jammed, a “Motor Stall” will result. Usually, some
foreign matter, or a piece of tungsten electrode has fallen within the gear
mechanism of the weldhead, hindering the rotation of the gears.
Clearing a Jammed Weldhead
In order to clear the jam, turn the weldhead upside-down and vigorously
shake the weldhead. Another way to attempt removal of the foreign matter is
to jog the rotor in the reverse direction.
This is accomplished by depressing the reverse direction button. Locate the
red button through the hole in the bottom of the handle. This is a momentary
reverse switch, which means the rotor will reverse momentarily when the
JOG button is pressed while holding the red button down.
Before turning the weldhead right side up, attempt to locate the foreign
object. If the jam cannot be cleared in this manner, the weldhead must be
returned to MK for disassembly to have the objects removed.
Gas Flow Rates
Recommended arc gas flow rate is 35 CFH at 50 PSI using the CobraTig
®
150
®
. Flow rates higher than 35 CFH can create turbulence within the
weldhead chamber and blow the arc about. If more gas coverage is
required, increase the pre-purge time on the CobraTig™.
Back-up gas flow rates are typically between 5 and 20 CFH, depending
on internal volume and component configuration. Typically, when welding
components with relatively large internal volumes, a separate source for
backup purge gas is recommended.
NOTE: Disassembly of weldhead will void the warranty.