Figure 4 – MK Products DiamondBack Weldhead User Manual
Page 11
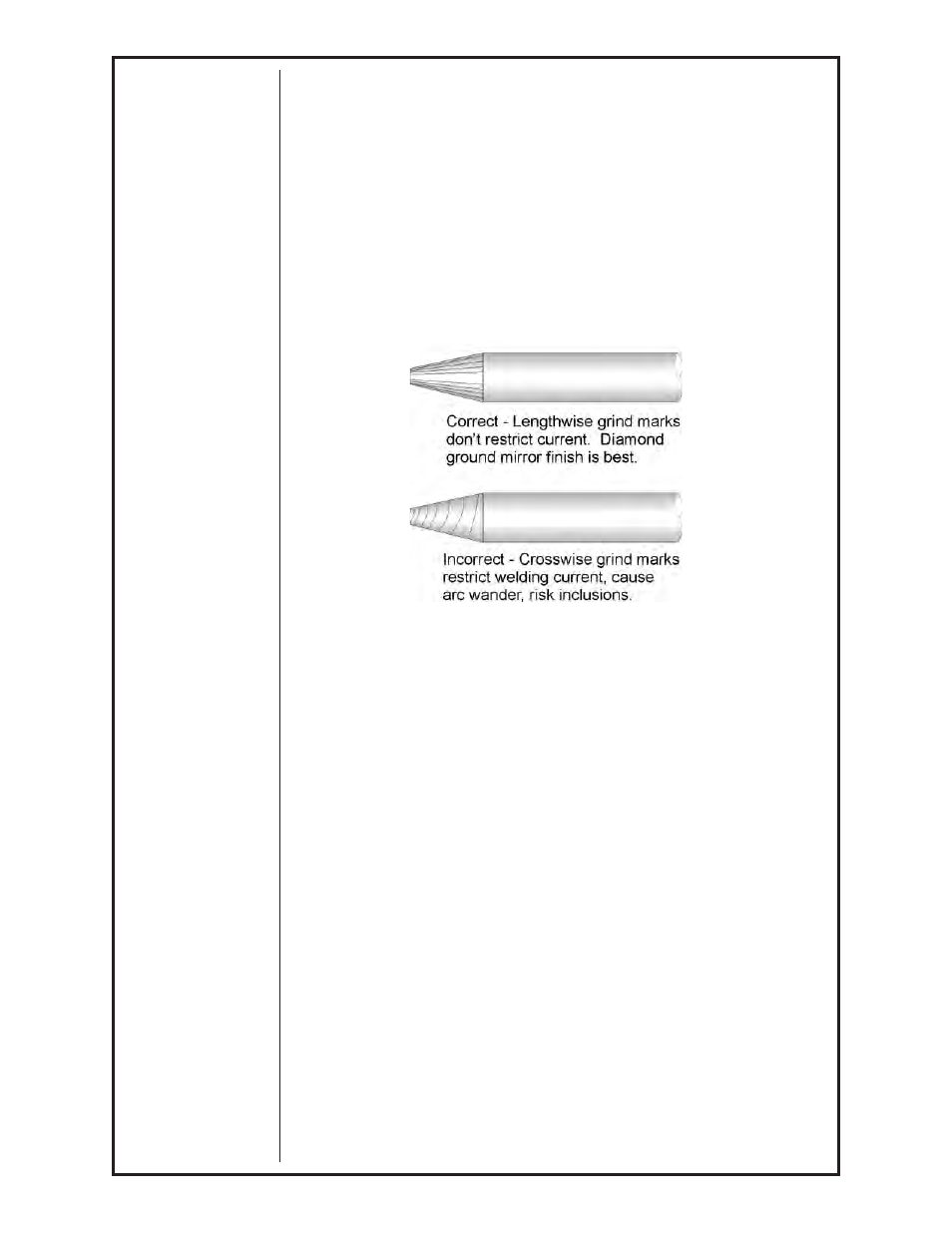
DiamondBack
™
Owner’s Manual - Page 3
Changes in electrode geometry can significantly influence the weld bead
shape and size; therefore, electrode tip configuration is a welding variable
that should be defined during procedure development.
Tungsten Preparation
Tungsten electrodes should be properly ground for consistent results. If
the electrode is to be hand ground, use a dedicated diamond wheel. The
grinding marks should be perpendicular to the tungsten electrode or poor arc
starts, arc wander and inclusions may occur (See Figure 4). No other parts
should be ground with these wheels, since contamination of the electrode
could result and create problems with arc initiation, arc wander during the
weld and tungsten inclusions in the weld bead.
All tungsten supplied by MK Products, Inc. is prepared using the latest
manufacturing techniques in order to meet the geometry specifications as
described above.
Installing the Tungsten Electrode
The electrode is mounted in the rotor and held in place with a setscrew.
To insert the electrode, jog the rotor around until the setscrew is exposed
(approximately at the twelve-o’clock position), and loosen the setscrew.
Insert a properly prepared electrode from the top of the rotor and tighten the
setscrew. Be sure to set the appropriate arc gap prior to welding.
Setting the Arc Gap
1. Place the part to be welded on the lower Collets with the clamps in the
upright open position.
2. Jog the rotor until the tungsten hole in the rotor is sitting directly over
the part with access to the tungsten set screw, approximately at twelve-
o’clock.
3. Prepare the tungsten electrode with the right length and shape as
explained in the Tungsten Geometry and Tungsten Preparation sections.
4. Put the tungsten electrode through the appropriate hole on the top of the
rotor.
5. Place the appropriate thickness gauge between the tungsten electrode
and the part to be welded so that the tungsten electrode is at the correct
gap.
Be certain the thickness gauge is perpendicular to the tungsten
electrode.
6. Tighten the setscrew to secure the tungsten electrode in the rotor.
Figure 4