MK Products DiamondBack Weldhead User Manual
Page 10
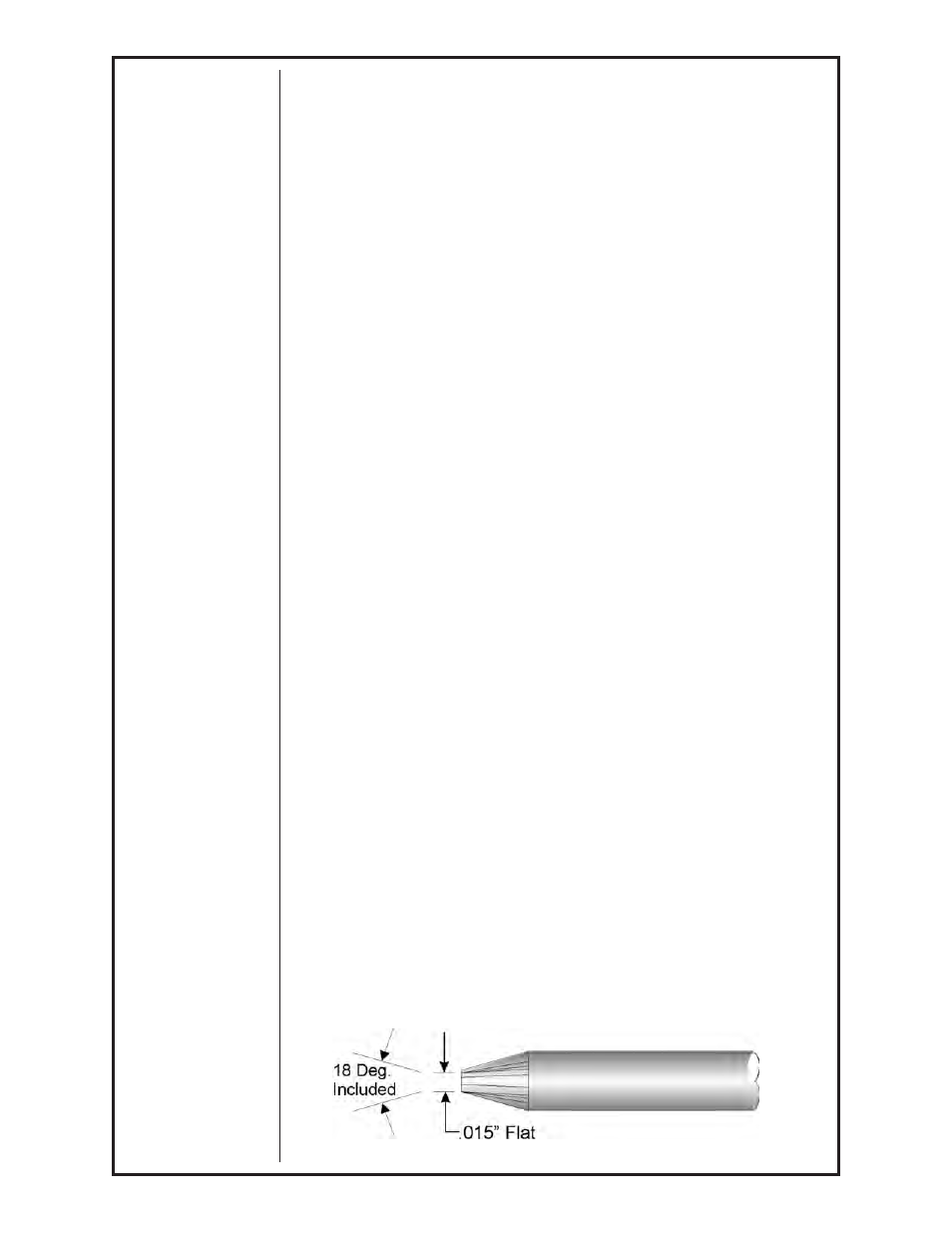
DiamondBack
™
Owner’s Manual - Page 2
Collet Selection
The three-piece collet assembly mounts to both the jaws and the bottom face
plate of the weldhead and maintains the weld joint alignment of the parts
to be welded. The collets are manufactured to correspond with the outside
diameter of the material to be welded. Each set of collets has three pieces;
two sides and one bottom. Two sets of collets are needed to weld two tubes
together. Appendix A lists collet part numbers for tube and pipe.
Collet Adjustment
The parts to be welded are held in place by the Collets. The tolerance of the
outside diameter of tubes and pipes vary, so these variations are handled
through the use of brass-tipped setscrews, referred to as plungers, in the
top Collet halves. These plungers not only make up the diameter difference
between the Collet and the part to be welded, but they also act as an aid in
the grounding path between the weldhead and the tube or pipe to be welded.
The tube or pipe is forced down into the bottom third of the collets, which are
screwed to a line-bored concentric face in the weldhead side-plates.
The plungers are adjusted as follows:
1. Back the plungers out until the brass tip is flush or below the surface of
the bored Collet surface.
2. Place the parts to be welded into the Collets and clamp down the latches.
Adjust the latching mechanism of the weldhead to ensure a tight, but not
overly-tight clamping of the Side Plate Jaws.
3. Alternately adjust the plungers on one side of the weldhead until contact
is made, and then add about 1/4 turn more.
4. At this point the tube should be firmly held in place. The tube should not
turn if attempting to rotate it by hand.
5. Repeat the process for the opposite side of the weldhead.
6. Once completed, check the alignment of the parts. A misalignment may
be corrected by moving the left or right plunger in or out by a fraction of
a turn and then repeating the opposite action to the opposing plunger on
the same Collet.
Tungsten Electrode Properties
The recommended tungsten type to be used in the DiamondBack™ and the
MK Orbital Welding System is 2% Ceriated, 3/32 inch diameter. 1/16 inch
diameter tungsten is also available for the DiamondBack™ orbital weldhead.
Appendix B gives the MK part numbers for pre-ground tungsten electrodes
and an illustrated formula to determine the length of tungsten electrode
required using a given weldhead size with a specified tube or pipe diameter.
These lengths of tungsten are long enough to allow the setscrew to securely
hold the tungsten while maintaining a relatively close arc gap, and keep the
tungsten from sticking out the back of the rotor while using a large arc gap.
Tungsten Geometry
The recommended grind angle and shape for tungsten is 18° included angle
and a .015 inch flat (Figure 3). Regardless of the electrode tip geometry
selected; it is important that consistent electrode geometry be used once a
welding procedure is established.
Figure 3