Snowmelt install-2.ai – Infloor Snow Melt Heavy-Duty Cable User Manual
Page 2
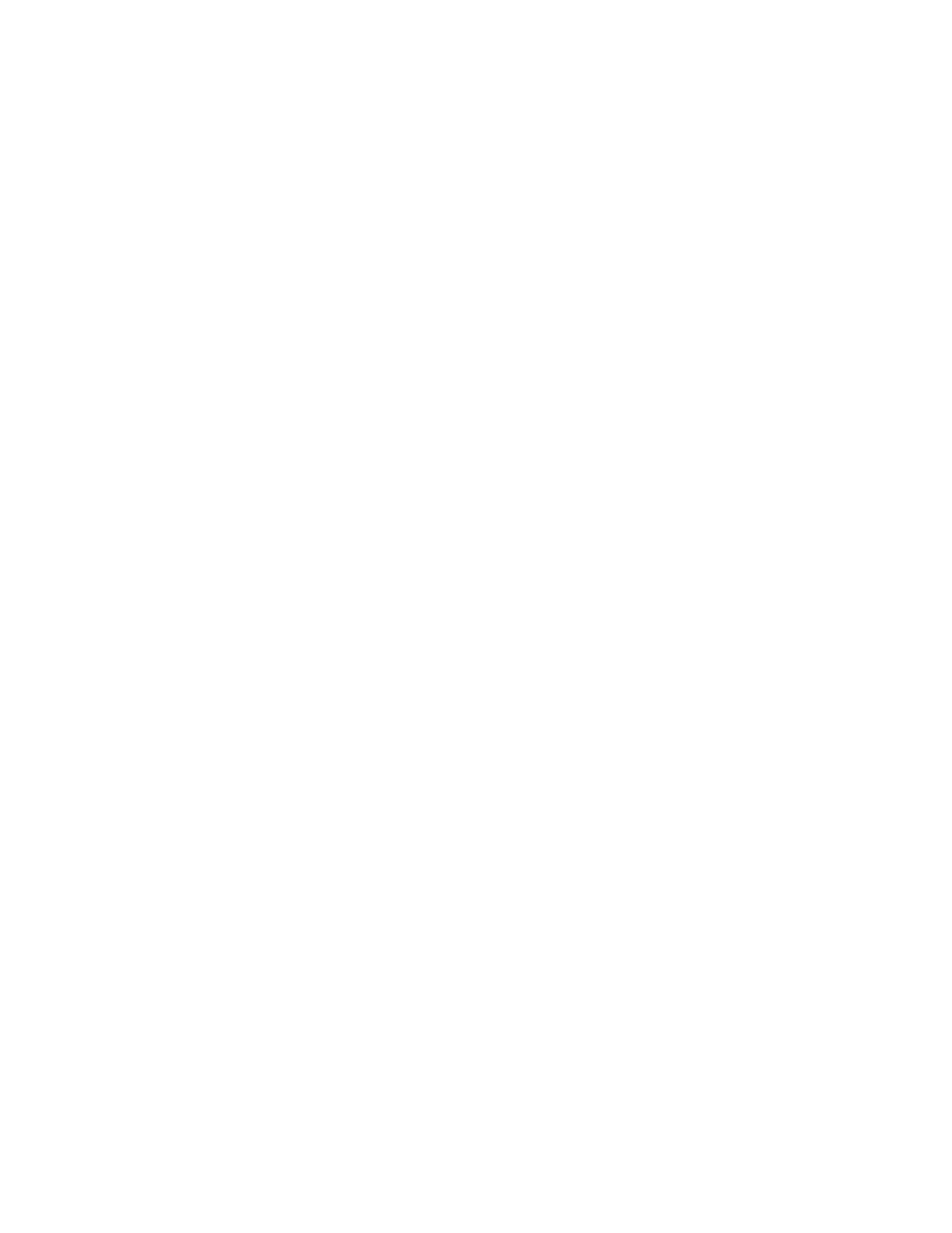
TESTING PROCEDURES FOR TXLP SNOW AND ICE MELTING CABLE
Cable Despription: 2 Black (non-heated power leads),
2 Green (ground wires) Spliced to the end of the blue heating cable.
1)
Verify the cable you ordered is the one that you received. Refer to the UL flag tag that is
attached to one of the black non-heated lead wires. This tag will list the following information:
Watts, Volts, Cable Length, Cable Spacing, Ohms and Amps.
2)
Visually check the cable for obvious flaws or breaks.
3)
With a digital ohm meter, check your resistance between the two block wires. Reading
should be between +/- 10% of the value listed on the UL tag. Record your readings for
warranty registration purposes.
4)
Again, using your digital ohm meter check the resistance between the black and the
green wires, the reading should be 1999, all blanks or infinity.
5)
Make sure all the blue heating cable and the splice are completely embedded in the
underlayment. Only the black and green lead wires are permitted to be out of the pour.
6)
During the installation of the topping, monitor the cable for any sudden changes in the
ohms.
7)
After the cable is installed, repeat steps 4 & 5.
8)
When performing an actual amperage test, never run the cable for more than 15 seconds.
9)
It’s very important to take a photo of the cable layout prior to the pour to avoid any
damage to the cable in the future.
GENERAL INFORMATION
TERMINAL INSULATION: Terminal insulation, if chosen or required, can be of a mineral wood or expanded polystrene. The
thickness depends on the local conditions, but normally 1-2 inches or R-12. When the heating cables are to be laid on top of
the insulation, cover the insulation with a wire mesh in order to prevent the cables from being pressed down into the insul-
ation during intallation.
VAPOR BARRIER: If a vapor barrier is required, it shall be of of non-metallic material such as plastic film. It must be located
so that no damage can occur due to mechanical causes or by overheating from the cables.
MECHANICAL INTERGRITY: When installing insulation and/or vapor barriers, it is important to make sure that the mech-
anical integrity of the pour is not compromised in anyway.
LAYOUT RESTRICTION: Heating cables must be installed in open areas only. The layout requires that the entire heating cable
be looped at even center spacing over the area that is to be heated. Both ends are terminated at a point where the power
connection is made. Details of cable length, on center spacing, loading, etc. are give on UL Tag. (MINIMUM DISTANCE BETWEEN
DISTANCE BETWEEN ADJACENT RUNS AND MININUM BENDING DIAMETER IS 2 INCHES).
When installing, it is important to remember that all of the heating cables, including splices to cold leads, must be embedded so
that only the non-heating leads are exposed outside the pour. By NEC standards a conduit is used to bring the leads out of the
pour. Minimum distance between the heating portion of the cable and any combustible surface shall be 1/32 inch. The heating
portion of the cable shall not touch, crossover, or overlap itself. As an option, measure and mark the center spacing within the
design area as a reference for cable layout. Lay the heating cable out starting and ending in the same location. The cable must be
laid at the calculated spacing. A template can be cut 1/4” less than the required center spacing. This will help insure the proper
layout of the heating cable. Cables should be secured using approved means (See Page 4) as noted within these instructions.
The cables should not be left unprotected for long periods of time or damage may occur. Concentrationof heating cables around
columns, drains, etc., may lead to overheating.
OUTDOOR COVERING MATERIALS: Asphalt, concrete or pavers (in sand or concrete) can be used as covering materials. The
coverings and bonding materials must be able to withstand a continuous temperature of 122 degress F (50 degrees C).
TEMPERATURE CONDITIONS: Heating cables should not be laid in temperatures below 25 F as the outer plastic jacket becomes
brittle at low temperatures and may crack as a result of an impact or jolt.