Groth 1400 User Manual
Page 13
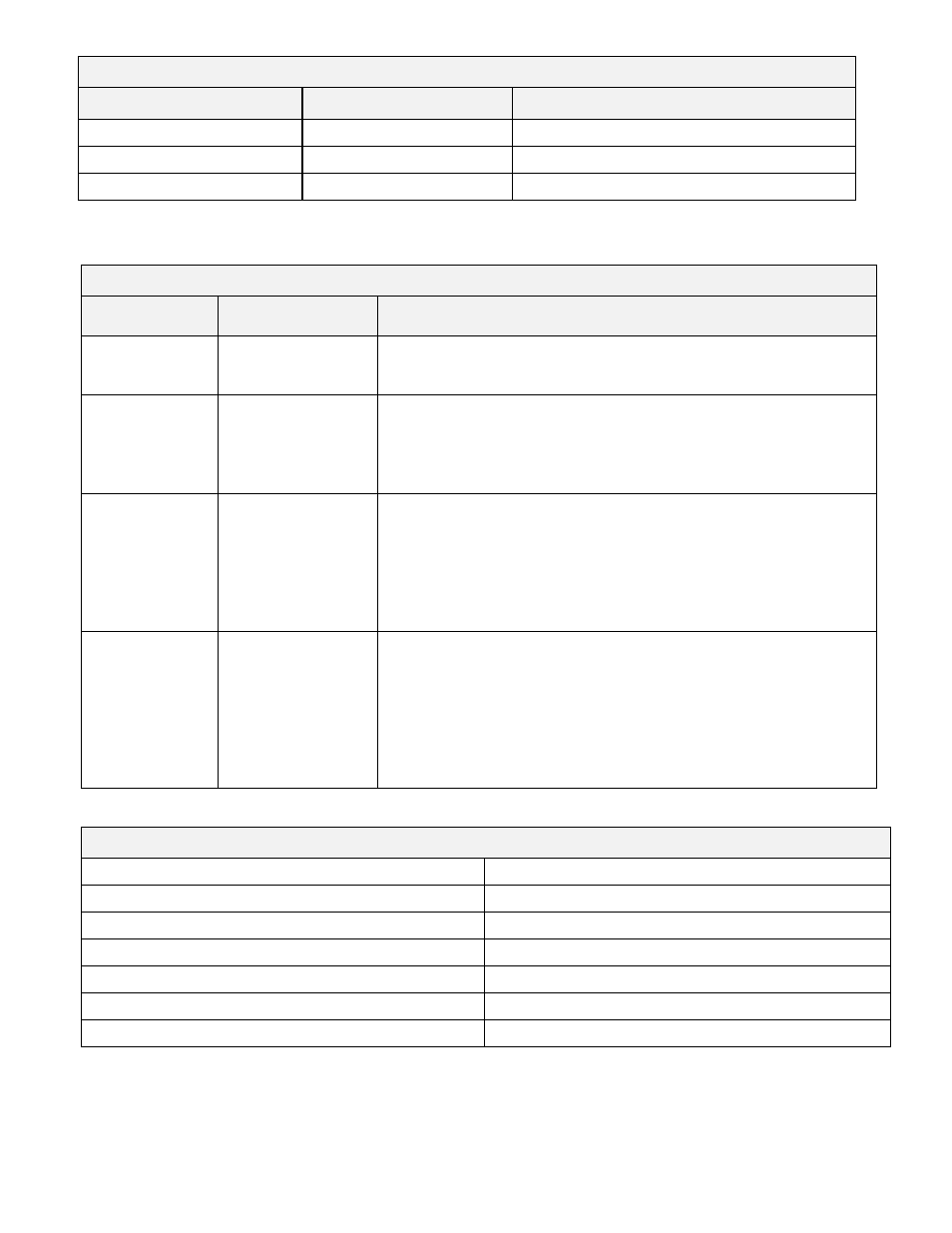
12
TABLE 6: LUBRICANTS – RECOMMENDATIONS
FASTENER LOCATION
LUBRICANT – SEALANT
MANUF. & PART NO.
Actuator Fastener
Dry Moly Film
Crown #6080 or equal
Stem Guide
MS2 Lubricant
Fel-Pro [Loctite] #51048 or equal
Stem/Swivel Fitting
Silicone Lubricant
Dow Corning #33 or equal
Note: Lubricant selection must consider process environment.
TABLE 7: TROUBLESHOOTING GUIDE
PROBLEM
INSPECTION
SUGGESTED CORRECTIVE ACTION
Pilot Valve
Leak
Visual, audible or
vapor detector
Consult troubleshooting guide in specific pilot valve manual
Main Valve
Actuator Leak
Visual, audible or
vapor detector
Leakage at the actuator flange may be corrected by tightening
the fasteners adjacent to the leak path. If this is not successful,
it will be necessary to install a new gasket. Refer to
instructions on page 6.
Vapor leakage
from the valve
body outlet.
Visual, audible or
vapor detector
Leakage can occur at the valve body seat - FEP film interface;
other leak paths are the swivel seal or a torn actuator
diaphragm. After removing the upper actuator housing, lift the
pallet assembly off the seat and inspect for damage to the film
or foreign debris buildup on the seat or film. Clean or replace
the pallet diaphragm as required. Refer to page 6.
Vapor leakage
between the
valve body and
tank nozzle
Visual, audible or
vapor detector
Leakage between the flanges may be corrected by tightening
the fasteners. Follow mounting instructions listed on page 4.
The gasket may have deteriorated due to the chemical
environment; replace if required. The tank nozzle may be
warped, corroded or scratched. This will require resurfacing of
the flange face; note that a flat faced flange is recommended to
avoid potential damage to an aluminum valve body.
TABLE 8: ABBREVIATIONS
ANSI American National Standards Institute
NPT
National Pipe Thread
API
American Petroleum Institute
POV
Pilot Operated Valve
BOM Bill of Materials
PSIG
Pounds/Sq. Inch – Gauge
DPHGM Diaphragm
PTFE
Fluoropolymer
FEP
Fluorocarbon Film (Fluoropolymer)
SS
Stainless Steel
MAWP Maximum Allowable Working Pressure
WC
Water Column
MS2
Moly – Disulfide