Automax logix 3200iq digital positioner – Flowserve Logix 3200IQ Digital Positioner User Manual
Page 21
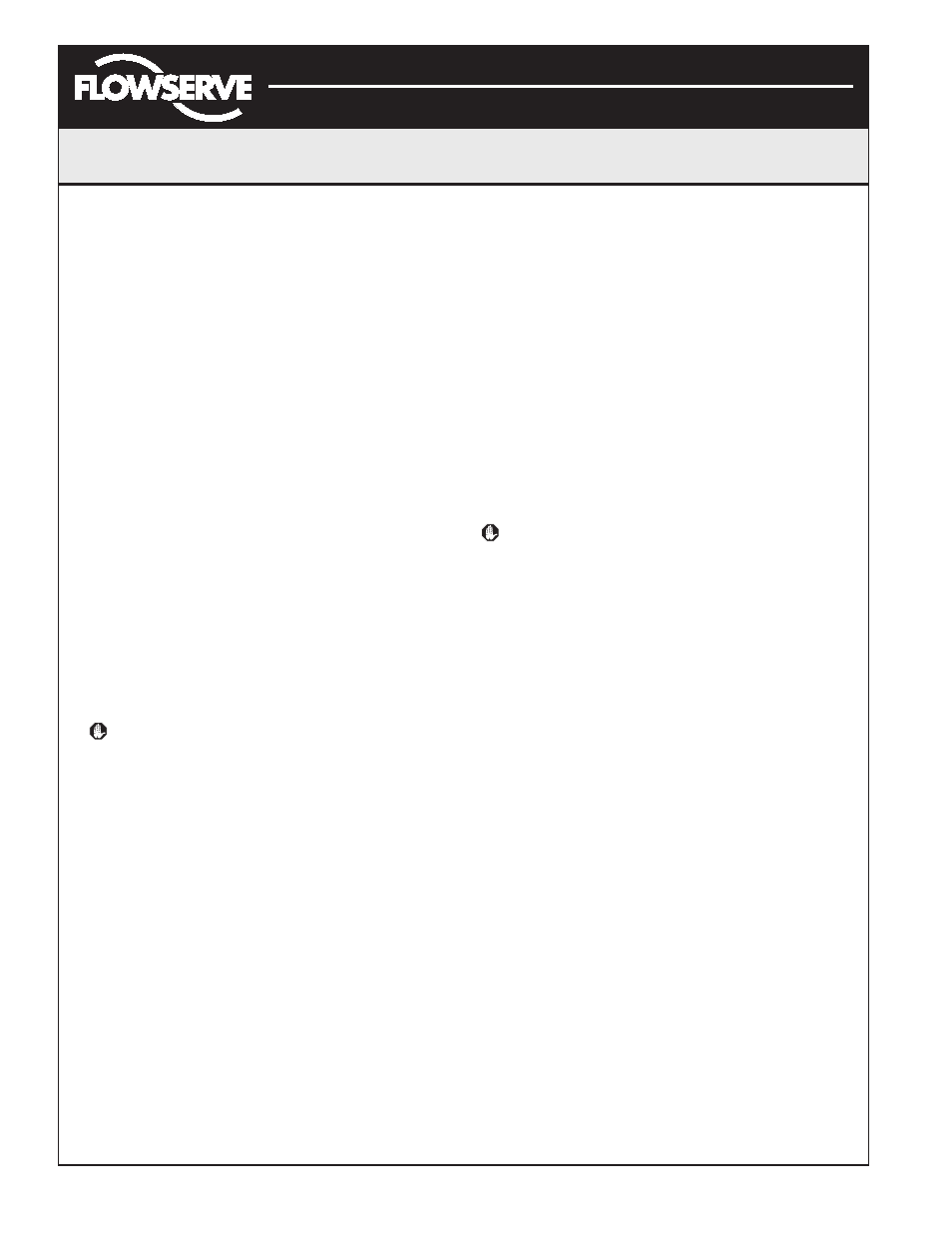
Flowserve Corporation
1350 N. Mountain Springs Parkway
1978 Foreman Dr.
Flow Control Division
Springville, Utah 84663-3004
Cookville, TN 38501
www.flowserve.com
Phone: 801 489 2233
Phone: 931 432 4021
FCD AXAIM3200-00 9/04
Page: 21 of 32
© 2004, Flowserve Corporation, Printed in USA
Automax Logix 3200IQ Digital Positioner
Installation, Operation and Maintenance Instructions
sensor calibration is performed using a HART 275/375
Handheld Communicator or configuration software
such as SoftTools. To upgrade a standard model to an
advanced model, refer to Figures 14, 18 and 28 and
proceed as outlined below. The following tools are
required:
• Phillips screwdriver
1. Make sure the valve is bypassed or in a safe condition.
2. Disconnect the power and air supply to the unit.
3. Remove the main cover.
4. Remove the plastic board cover by removing the three
retaining screws (see Figure 18).
5. Remove the two screws holding the pressure sensor
plug plate to the housing. Lift the metal stiffener plate
off the pressure sensor plug plate and set aside for
future use.
6. Remove the pressure sensor plug plate and discard.
Installing the Pressure Sensor Board (Advanced Model)
The pressure sensor board is installed on the advanced
model only. To install the pressure sensor board, refer to
Figures 14, 18 and 28 and proceed as outlined below.
The following tools are required:
• Phillips screwdriver
• Torque wrench
WARNING: Observe precautions for handling
electrostatic sensitive devices.
1. Verify that the two pressure sensor O-rings (item 15)
are in place in the housing.
2. Set the pressure sensor board assembly in place so
that the O-rings make contact with the faces of the
pressure sensors.
3. Place the metal stiffener plate (item 12) on top of the
pressure sensor board over the pressure sensors and
align the two holes in the pressure sensor plate with
the threaded bosses in the housing.
4. Insert two screws through the stiffener plate and
pressure sensor board into the threaded holes in the
housing and tighten evenly, to 8 in-lb.
5. Connect the ribbon cable on the pressure sensor board
to the main PCB assembly.
6. Install the plastic board cover. Insert the three retaining
screws through the plastic cover into the threaded
boss and tighten evenly, using a Phillips screwdriver.
Do not overtighten.
7. Reinstall all covers.
8. Reconnect power and air supply to the positioner.
Use SoftTools or a handheld communicator to perform
a pressure sensor calibration.
Customer Interface Board
The customer interface board provides a connection
point inside the explosion-proof housing for all hookups
to the positioner. Calibration of the loop current and the
analog output current (optional) are performed using a
HART 275/375 Handheld Communicator or configuration
software such as SoftTools.
Replacing the Customer Interface Board
To replace the customer interface board, refer to
Figures 9, 14, 18 and 28 and proceed as outlined below.
The following tools are required:
• Phillips screwdriver
WARNING: Observe precautions for handling
electrostatic sensitive devices.
1. Make sure the valve is bypassed or in a safe condition.
2. Disconnect the power and air supply to the unit.
3. Remove the main cover.
4. Remove the plastic board cover by removing the three
retaining screws (see Figure 18).
5. Remove the five wire connections from the main
PCB assembly (six wire connections if the unit is
equipped with the 4-20 mA analog output option)
(see Figure 14).
6. Remove the retaining screw from the main PCB
assembly and lift the main PCB out of the housing
(see Figure 18).
7. Remove the user interface cover.
8. Disconnect the field wiring from the customer interface
board terminals and remove the three screws that
hold the customer interface board in the housing
(see Figure 9).
9. Remove the customer interface board, carefully pulling
the wiring through the bore.
10. Verify that the O-ring is in place in the counterbore in
the positioner housing.
11. Feed the wires on the back of the new customer user
interface board through the passageway into the main
chamber of the housing.
12. Set the customer interface board in place and secure
with three screws (see Figure 9).
13. Reconnect the field wiring to the customer interface
board terminals.