Flowserve 510si Series Digital Positioner User Manual
Page 10
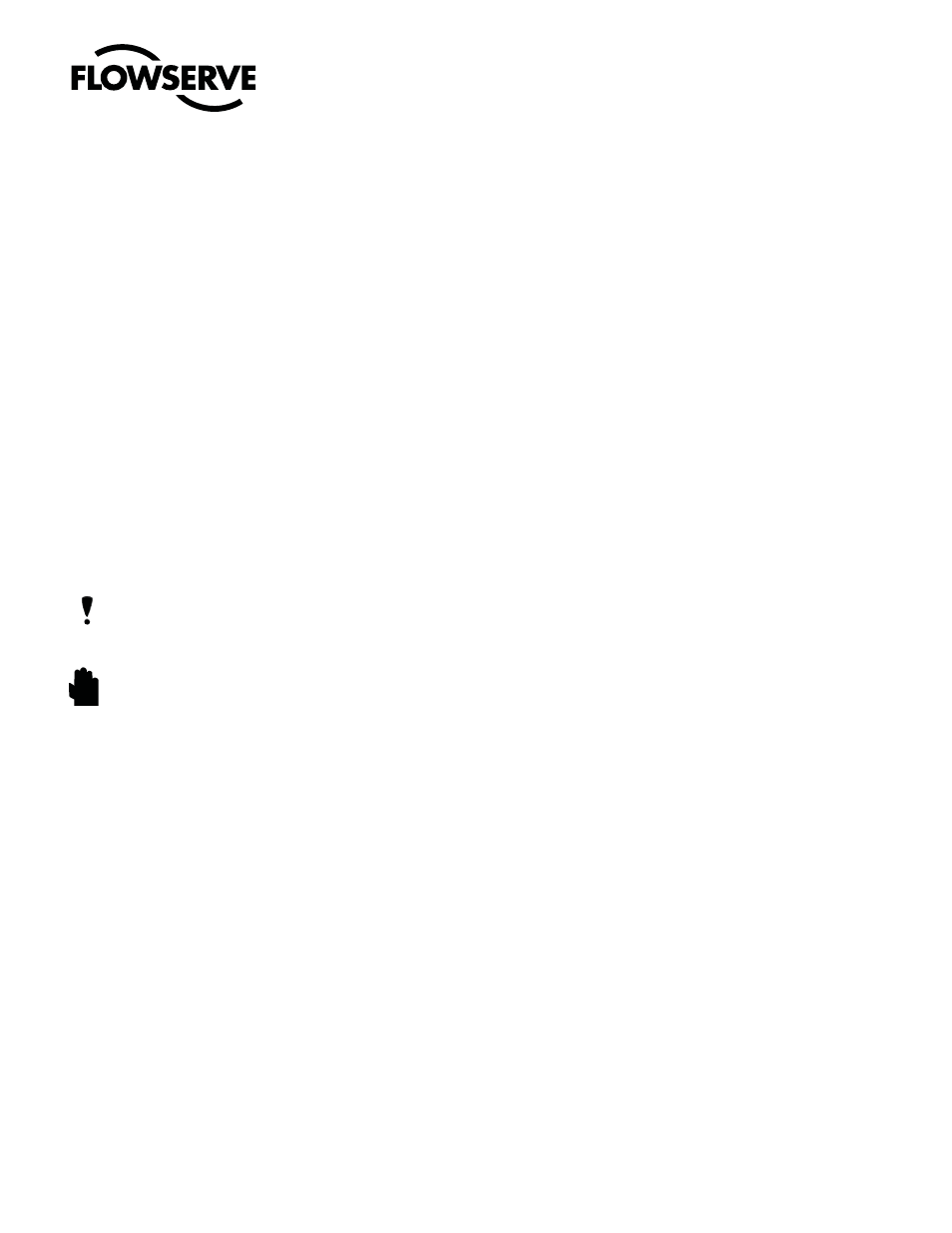
10
®
User Instructions Logix 510si - LGENIM0510-0
2 12/13
If the Quick calibration switch is set to Jog, the LED’s will
initially flash in a sequence of Y-R-R-G (yellow-red-red-
green) which indicates that the user must use the jog
keys to manually position the valve to 100%. When the
valve is approximately at the position desired for 100%
open, press both the D and — buttons simultaneously
to proceed to the next step. (Note that the Logix 510si
is only setting internal gain and direction of rotation
parameters at this point the actual span is set after
the zero is set.) The valve will then moved closed and
flash a Y-G-G-R sequence, allowing the user to adjust
the valve position to 0% using the jog buttons. When
the stem is properly positioned press both the D and
— buttons simultaneously again to register the 0%
position and to proceed. The valve will then stroke back
to the 100% open position and the calibration LED’s
will flash in a sequence of Y-R-R-G again and wait for
the user to make final adjustments. When the 100% is
correct press both the D and — buttons simultaneously
to continue. No more user actions are required while
the calibration process automatically finishes. When
the lights return to a sequence that starts with a green
light the calibration is complete. (see the appendix for
an explanation of the various light sequences)
NOTE: It is recommended that the first time a Logix
510si is installed on a new actuator a second QUICK-
CAL be performed.
WARNING: When operating using local control of the
valve, the valve will not respond to external commands.
Notify proper personnel that the valve will not respond
to remote command changes, and make sure the valve
is properly isolated.
8.5
Local control of valve position-Can be done from the
user interface by holding both jog buttons while then
simultaneously pressing the quick cal button for 3
seconds. When in this mode the position can be ad-
justed using the
Δ and ∇ buttons. While in this mode
the LED’s will flash a YGRR (yellow-green-red-red)
sequence. To exit the local control mode and return
to normal operation, briefly press the quick-Cal button.
8.6 Factory
reset - Hold Quick cal button while applying
power and all of the internal variables including calibra-
tion will be reset to factory defaults. The positioner
must be re-calibrated after a factory reset.
8.7 Loop
Calibration – Using a small pointed object push
and hold, the Loop Calibration button through the small
hole on the electronic cover for 3 seconds to initiate
calibration of either the 4-20 mA input or output current
loop as selected by the bottom Dip switch.
8.7.1 Input loop calibration - Note that the valve will be locked
at its position when an input loop calibration is initiated
until the calibration is completed. If a loop calibration
is started with the Input loop selected on the Loop
calibration Dip switch, the LED’s will flash a sequence
STOP!
of Y-G-G-Y indicating that it is waiting for the minimum
signal to be input to the positioner on terminals +11 and
–12 from an external 4-20 mA current source. Normally
this will be 4 mA, but if split range operation is required
use the minimum current for the desired operating
range. When the minimum signal value is set at the
desired value, press the
Δ and ∇ buttons simultane-
ously to proceed to the next step. The LED’s will now
flash a sequence of Y-G-Y-R indicating that it is waiting
for the maximum signal to be input to the positioner.
Normally this will be 20 mA, but if split range operation
is required use the maximum current for the desired
range. When the maximum signal value set at the de-
sired value, press the
Δ and ∇ buttons simultaneously
to set the span. The LED’s then will flash a sequence
of Y-Y-G-G indicating that the calibration is complete.
The signal can now be adjusted to the desired output
value without affecting the valve position. Press the
Δ
and
∇ buttons simultaneously to put the unit back in
operation. Note that the input calibration correlates the
signal to 0% and 100% signal. It does not affect the
position calibration at all since that calibration is done
separately with the Quick-Cal button.
8.7.2 Output
loop
calibration (optional) - If a loop calibration
is started with the Output loop selected on the Loop
calibration Dip switch, the LED’s will flash a sequence
of Y-G-G-G indicating that it is waiting for the 0% signal
to be adjusted using the
Δ and ∇ buttons for the output
current loop on positioner on terminals +31 and –32.
(Note that the loop must be externally powered with a
voltage between 12VDC and 40VDC and a current meter
used to measure the current in the loop). Normally this
will be 4 mA, but if split range operation is required
adjust to the minimum current for the desired range.
When the 0% signal value is set at the desired value,
press the
Δ and ∇ buttons simultaneously to proceed
to the next step. The LED’s will now flash a sequence
of Y-
G-Y-Y indicating that it is waiting for the 100%
signal to be adjusted using the
Δ and ∇ buttons for the
output current loop. Normally the 100% setting will be
20 mA, but if split range operation is required adjust
to the maximum current for the desired range. When
the 100% signal value is set at the desired value press
the
Δ and ∇ buttons simultaneously to complete the
calibration.
8.7.2.1 Logix 510 Binary / Linear Analog Output
Flowserve has added a Binary AO feature to the Logix
510 positioner. This feature will allow the standard
Analog 4-20mA current Output of the Logix 510 to
be used as a Position Deviation Alarm Indicator. One
distinct current level will be used to indicate the alarm
condition, and another distinct current level will be used
to indicate normal operation.