9 normal operation – Flowserve SLM-6000 User Manual
Page 11
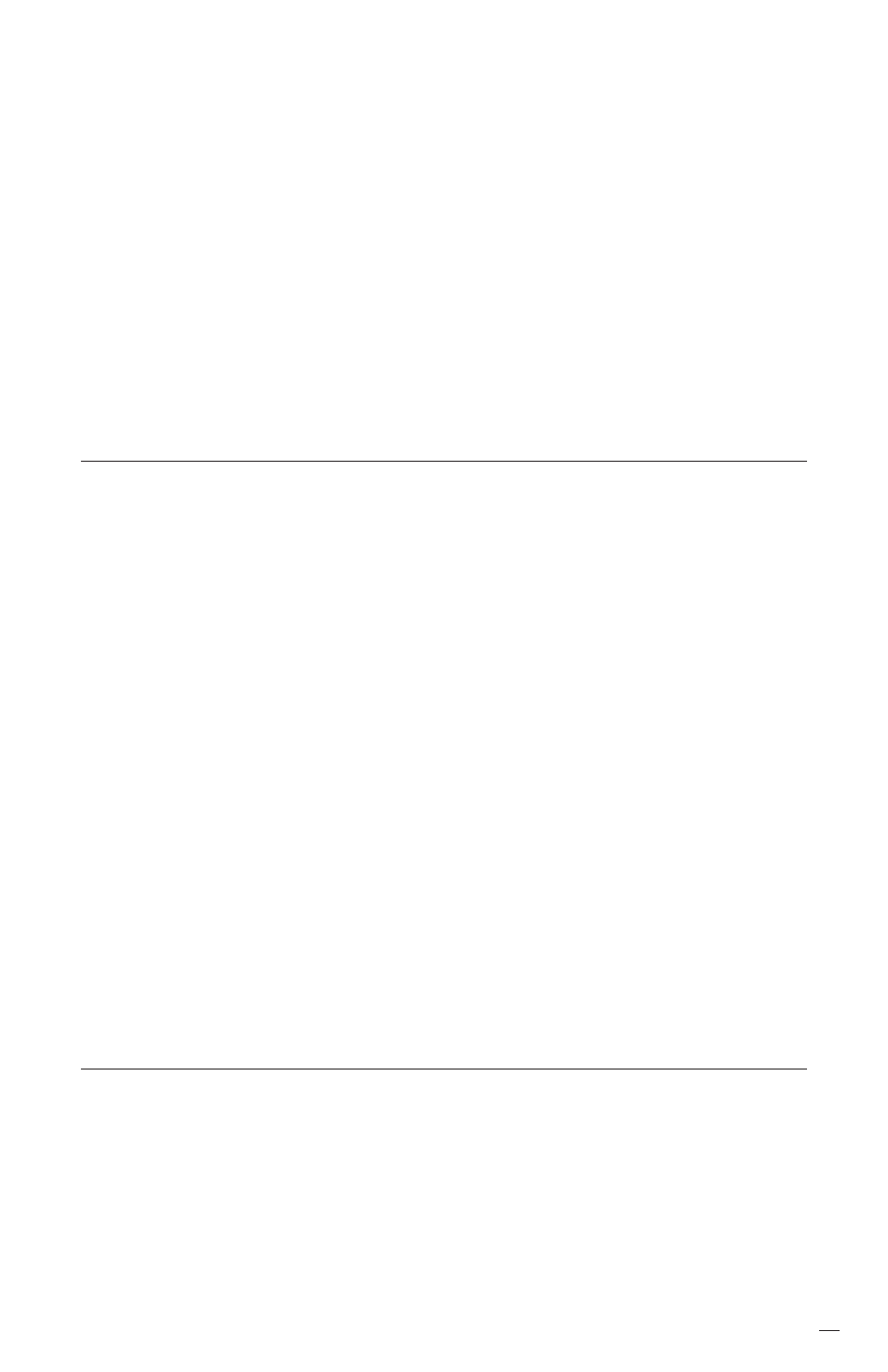
7.2.4 Supply tank “Buffer” fluid level must be maintained at all times when
equipment is pressurized and in operation. Fresh buffer fluid should be used
when it becomes cloudy or contaminated with process fluid. Quench supply
tank should have a drain connection located on the bottom and a fill
connection on the top that can be used when adding or exchanging buffer
fluid. Supply tanks may or may not also have cooling coil connections. Buffer
fluid flow is a function of the seal circulation device and thermosyphoning
created by proper location of supply tank. Buffer fluid must always be kept at
0-69 kPa maximum (0-1 psig maximum).
7.3 Your SLM-6000 Mechanical Seal is now ready for operation.
Warning: To ensure that the mechanical seal does not run dry, leave motor v-belts or
drive coupling off the pump until the motor has been tested for rotation.
Note: For any subsequent impeller or bearing adjustment, reverse steps 6.1, and 6.2.
8 Start Up and Shut Down Procedures for the SLM-6000
Slurry Seal
Because the seal has no flush and relies on the product for seal face lubrication, the pump
cavity must be completely full of liquid before start up. Take the following steps to ensure
dry running does not occur:
8.1 Pump Start-Up
8.1.1 Open the suction valve.
8.1.2 Open the discharge washout/bleed valve to release any air that may be
trapped in the piping. Close the valve after a steady stream of liquid flows
from it. If little or no liquid appears, do not start the pump. This means that
part of the piping system is blocked with product.
8.1.3 Partially open the discharge valve to ensure that water hammer or cavitation
does not occur at start up.
8.1.4 After start up, slowly open the discharge valve. This will keep a false head
on the pump until the line fills.
8.2 Pump Shut-Down
8.2.1 Stop the pump.
8.2.2 Close the discharge valve.
8.2.3 Close the suction valve.
8.2.4 Drain all product from the pump seal chamber or flush with clean water or
process fluid to prevent solids in the slurry (either free solids or dissolved
solids that will precipitate out when temperature is reduced during standby)
from setting in the seal chamber or volate.
9 Normal Operation
Never allow equipment to run dry during operation, as this will certainly result in premature
seal failure.
9.1 Do not allow equipment to cavitate, as this will shorten seal life.
9.2 Do not induce water hammer in the pipeline, as this can place undo strain on the
seal components.
9.3 Do not allow the seal chamber pressure to drop below 5 psi while equipment is in
operation as this may prevent lubrication from reaching the seal faces.
11