1 general product information, 1 introduction, 2 multibus types – Bronkhorst EtherCAT User Manual
Page 4: Ntroduction, Ultibus types, 1general product information
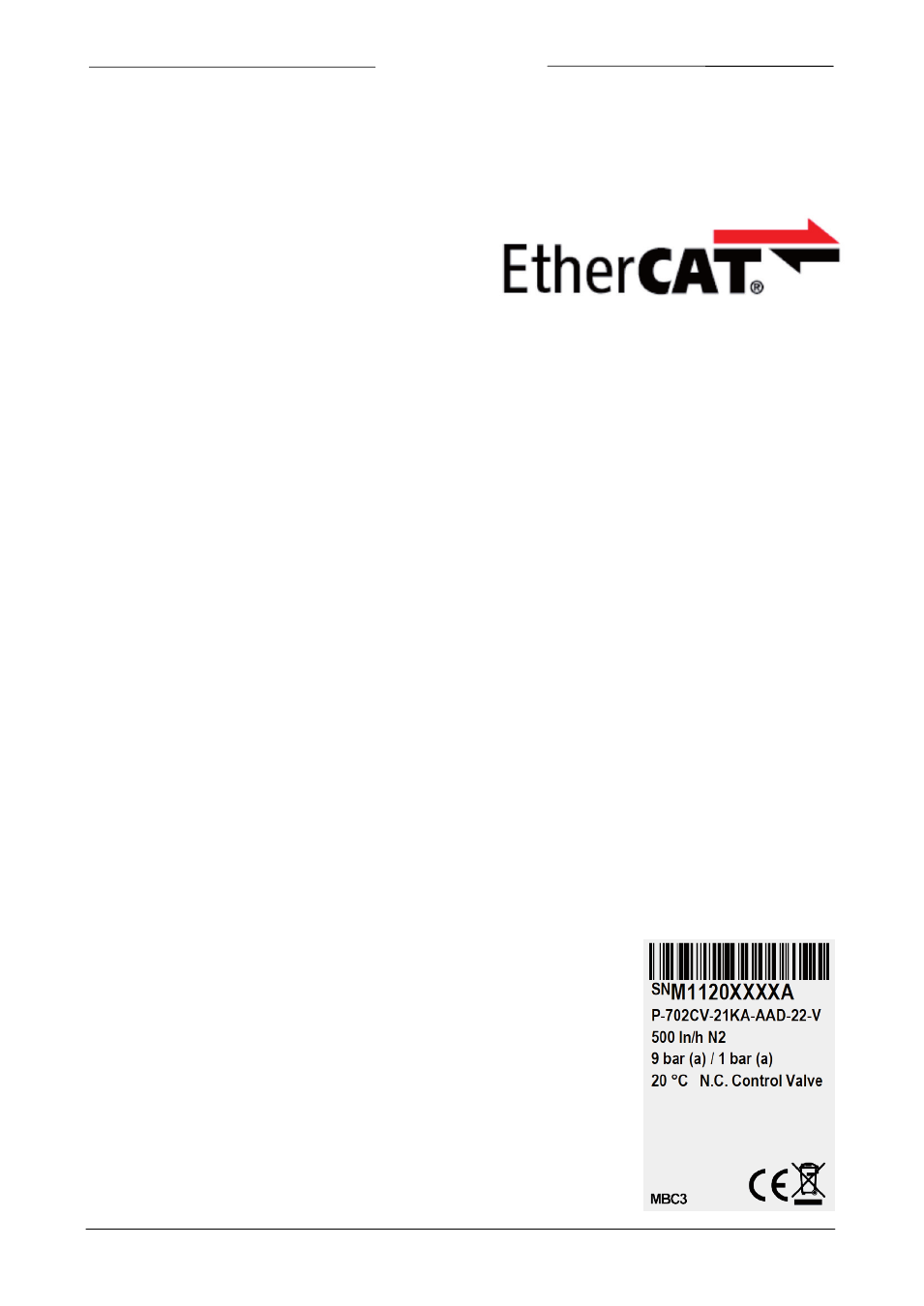
BRONKHORST
®
1
GENERAL PRODUCT INFORMATION
1.1
I
NTRODUCTION
Ethernet for Control Automation Technology (EtherCAT) is
an open high performance Ethernet-based field bus system.
The development goal of EtherCAT was to apply Ethernet to
automation applications which require short data update
times (also called cycle times) with low communication jitter
(for synchronization purposes) and low hardware costs.
Bronkhorst
1)
implemented EtherCAT
2)
on its instruments.
Typical automation networks are characterized by short data length per node, typically less than the minimum
payload of an Ethernet frame. Using one frame per node per cycle therefore leads to low bandwidth utilization and
thus to poor overall network performance. EtherCAT therefore takes a different approach, called "processing on the
fly".
With EtherCAT, the Ethernet packet or frame is no longer received, then interpreted and copied as process data at
every node. The EtherCAT slave devices read the data addressed to them while the telegram passes through the
device. Similarly, input data are inserted while the telegram passes through. The frames are only delayed by a fraction
of a microsecond in each node, and many nodes - typically the entire network - can be addressed with just one frame.
Short cycle times can be achieved since the host microprocessors in the slave devices are not involved in the
processing of the Ethernet packets to transfer the process images. All process data communication is handled in the
slave controller hardware. Combined with the functional principle this makes EtherCAT a high performance
distributed I/O system: Process data exchange with 1000 distributed digital I/O takes about 30 µs, which is typical for a
transfer of 125 byte over 100Mb/s Ethernet. Data for and from 100 servo axis can be updated with up to 10 kHz.
Typical network update rates are 1–30 kHz, but EtherCAT can be used with slower cycle times, too, if the DMA load is
too high on your PC.
1)
Bronkhorst:
This includes Bronkhorst High-Tech B.V. , Bronkhorst Cori-Tech B.V. and
M+W Instruments GmbH.
2)
EtherCAT®:
EtherCAT® is registered trademark and patented technology, licensed by Beckhoff Automation
GmbH, Germany.
1.2
M
ULTIBUS TYPES
In 2000 Bronkhorst developed their first digital instruments according to the “multibus” principle. The basic pc-board
on the instrument contained all of the general functions needed for measurement and control, including alarm,
totalizing and diagnostic functions. It had analog I/O-signals and also an RS232 connection as a standard feature. In
addition to this there is the possibility of integrating an interface board with DeviceNet™, Profibus-DP
®
, Modbus or
FLOW-BUS protocol. The first generation (MBC-I) was based on a 16 bit Fujitsu controller. It was superseded in 2003
by the Multibus type 2 (MBC-II). This version was also based on the 16 bit Fujitsu controller but it had several
improvements to the MBC-I. One of them is the current steering of the valve. It
reduced heat production and improved control characteristics. The latest version
Multibus controller type 3 (MBC3) is introduced in 2011. It is build around a 72MHz
32 bit NXP ARM controller. It has AD and DA controllers on board which makes it
possible to measure noise free and control valves without delays. The internal control
loop runs 6 times faster compared to the MBC-II therefore control stability has
improved significantly. It also has several improved functions like reverse voltage
protection, inrush current limitation and overvoltage protection.
MBC3 instruments can be recognised by the “MBC3” placed on lower left side
of the instrument label (see example).
Page 4
EtherCAT interface
9.17.063