4 start-up, 5 operating conditions, 6 instrument performance – Bronkhorst IN-FLOW User Manual
Page 26: 1 sensors, 2 controllers, 7 manual operation
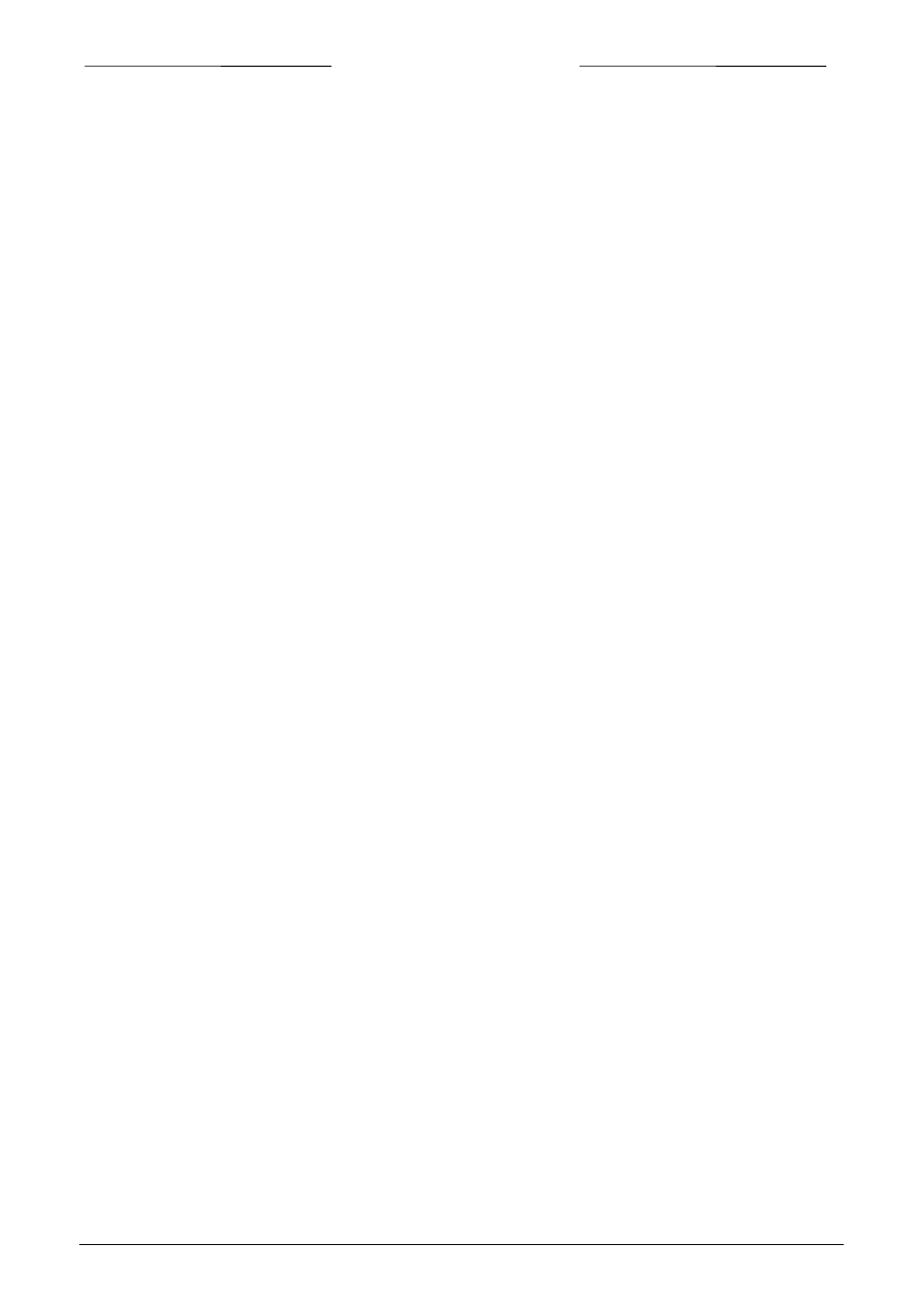
BRONKHORST HIGH-TECH B.V.
page 26
9.17.022
3.4
Start-up
Turn on fluid supply gently. Avoid pressure shocks, and bring the instrument gradually up to the level of the
actual operating conditions. Also switch off fluid supply gently. In case of liquid control be sure to remove all
trapped gas bubbles from the system. The purge connection on top of the control valve can be used for this
purpose.
3.5
Operating conditions
Each instrument has been calibrated and adjusted for customer process conditions.
Controllers or valves may not operate correctly, if process conditions vary too much, because of the
restriction of the orifice in the valve.
For flowmeters performance and accuracy may be affected tremendously if physical fluid properties such as
heat capacity and viscosity change due to changing process conditions.
3.6
Instrument performance
3.6.1 Sensors
Assuming that the transfer function of a system is an exponential shaped curve, the time constant is defined
as follows:
time constant = time for the signal to reach 63.2 % of its final output value. Approx. five time constants is the
time to reach the final value.
The time constant of flowsensors depends on the type of instrument and settings.
Pressure sensors have a time constant of some milliseconds. However the actual response is determined by
the pneumatic response of the system which the pressure meter is part of.
3.6.2 Controllers
The dynamic response of a controller is factory set. Standard settling time is defined as the time to reach the
setpoint (and stay) within ± 2% of the initial setpoint.
The control mode is factory set in such a way that after a step change, there will be little overshoot.
Note:
In pressure control systems the system widely determines the response behaviour of the control loop. During
testing the customer system is simulated as closely as possible. In some cases however readjustment is
needed for optimum performance under actual conditions.
3.7
Manual operation
By means of manual operation of the micro push-button switch some important actions for the instrument can
be selected/started. These options are available in both analog or BUS/digital operation mode.
(see also manual operation in document number 9.17.023)
These functions are:
- reset (instrument firmware-program reset)
- auto-zeroing (remove zero-drift offset in sensor bridge)
- restore factory settings (in case of unaccidently changing of the settings)
for FLOW-BUS only:
- automatic installation to FLOW-BUS (installs instrument to free address)
- remote installation to FLOW-BUS (instruments will be installed by E-7000 or PC-software)