Motor heating – Applied Motion ST10-Plus User Manual
Page 28
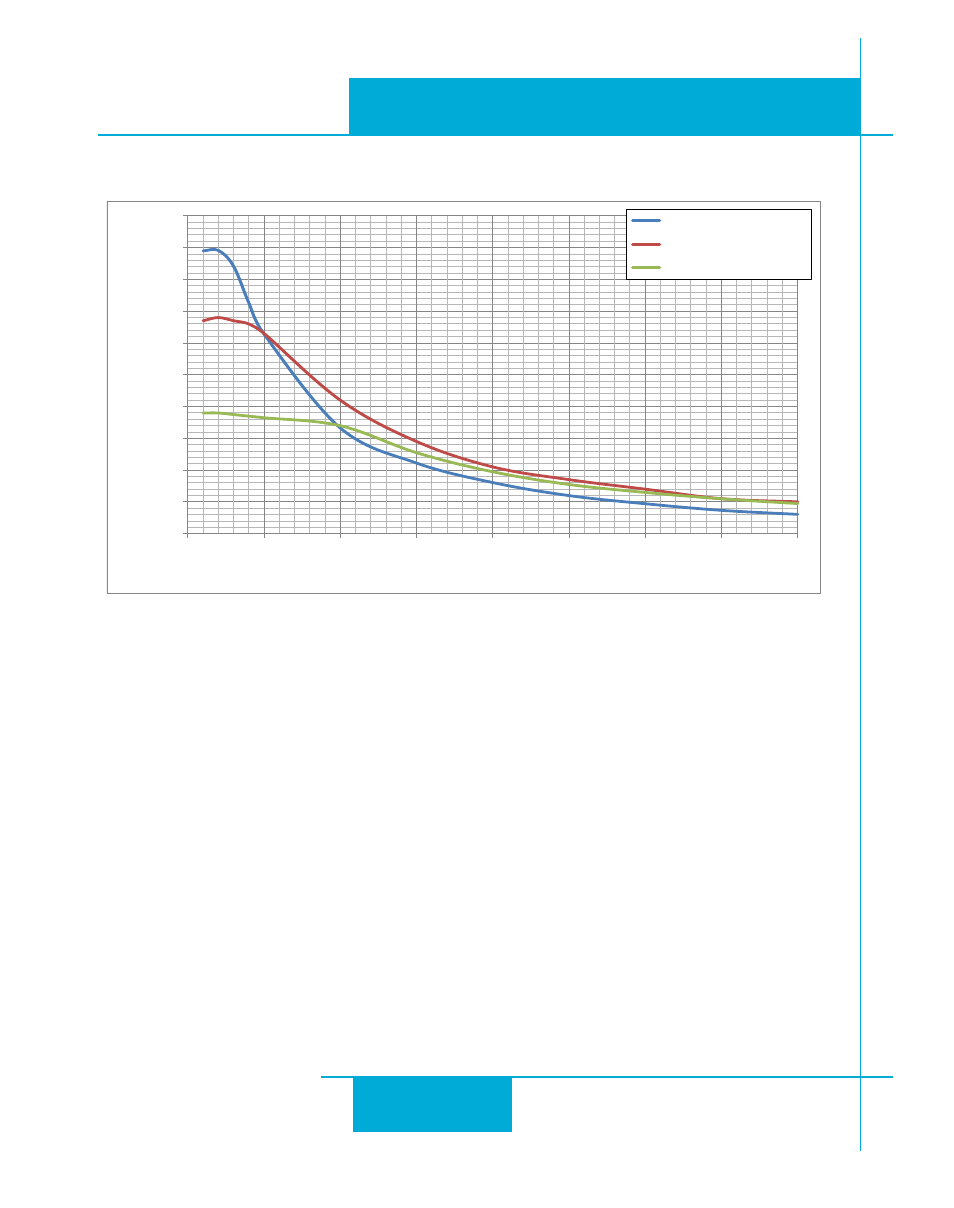
28
ST5/10-S Hardware manual
920-0027 Rev. D
2/7/14
Motor Heating
Step motors convert electrical power from the driver into mechanical power to move a load. Because step motors
are not perfectly efficient, some of the electrical power turns into heat on its way through the motor. This heating is
not so much dependent on the load being driven but rather the motor speed and power supply voltage. There are
certain combinations of speed and voltage at which a motor cannot be continuously operated without damage.
We have characterized the recommended motors in our lab and provided curves showing the maximum duty
cycle versus speed for each motor at commonly used power supply voltages. Please refer to these curves when
planning your application.
Please also keep in mind that a step motor typically reaches maximum temperature after 30 to 45 minutes of
operation. If you run the motor for one minute then let it sit idle for one minute, that is a 50% duty cycle. Five min-
utes on and five minutes off is also 50% duty. However, one hour on and one hour off has the effect of 100% duty
because during the first hour the motor will reach full (and possibly excessive) temperature.
The actual temperature of the motor depends on how much heat is conducted, convected or radiated out of it. Our
measurements were made in a 40°C (104°F) environment with the motor mounted to an aluminum plate sized to
provide a surface area consistent with the motor power dissipation. Your results may vary.
HT34-504/505/506 with ST10
60 VDC power supply, 20000 steps/rev, all motors connected in parallel
0
100
200
300
400
500
600
700
800
900
1000
0
5
10
15
20
25
30
35
40
oz
-in
rev/sec
HT34-506 (6.72 A/phase)
HT34-505 (7.56 A/phase)
HT34-504 (7.56 A/phase)