Parts replacement, Friction facings, General – Nexen SPC 837400 User Manual
Page 12
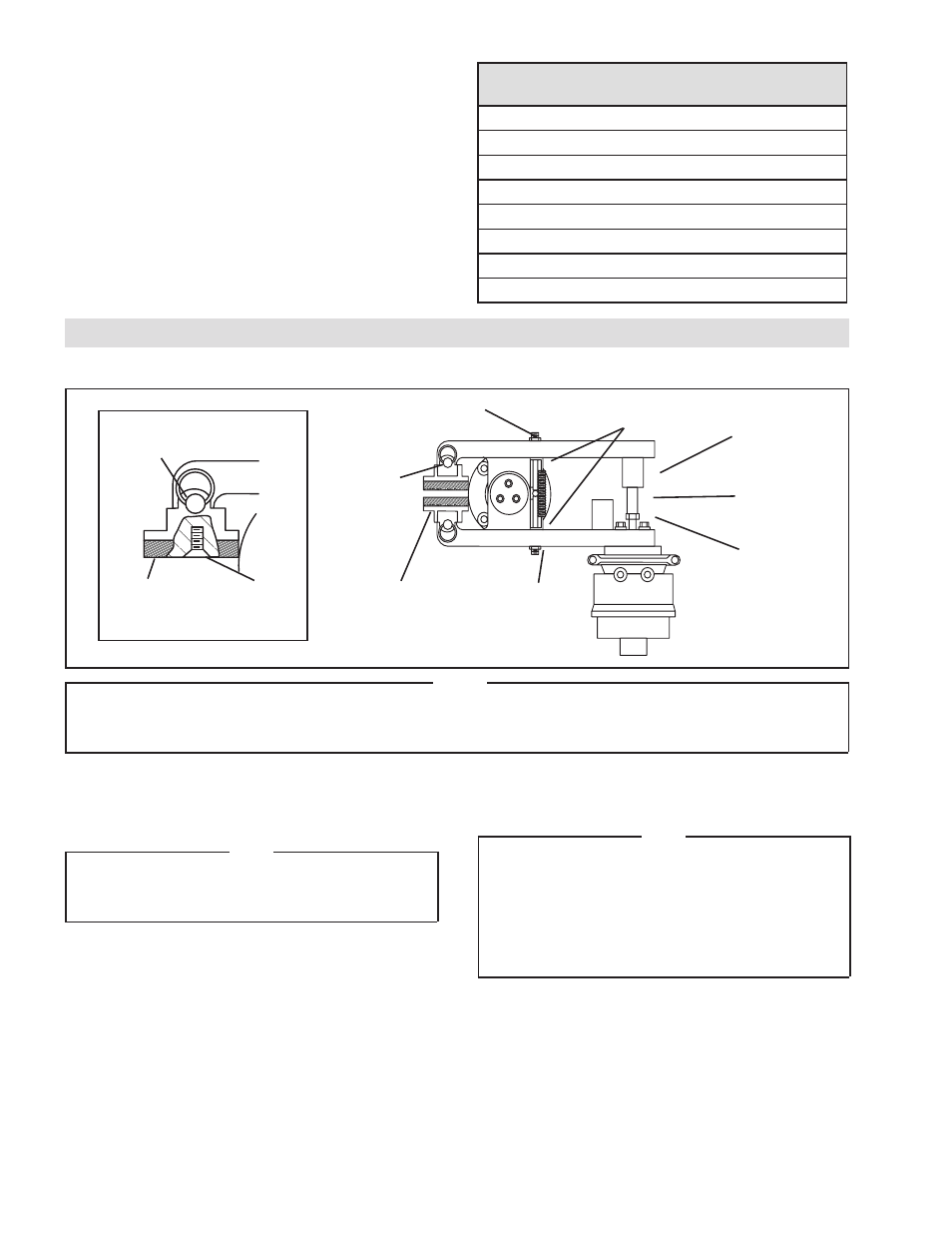
12
FORM NO. L-20095-U-1112
1. Manually release the spring actuators (See Figure
11).
2. Apply hold-off air pressure. This will remove any tension
on the Tap Bolt for easier release.
Note
Before performing step three, determine the actuator
type and select either step 3a or 3b. Step four returns
to general instructions used for both models.
o
bSolete
t
hree
-P
ort
a
ctuator
o
nly
3a. Using a 9/16 inch socket wrench, turn the tap
bolt counterclockwise until the brake is released
(approximately 40 turns). Hold-off air pressure can
be removed at this time and service performed.
t
wo
P
ort
a
ctuator
o
nly
3b. Using a 3/4 inch socket, turn the tap bolt
counterclockwise to fully cage (compress) the spring.
The spring is fully compressed when the bolt is backed
out of the unit 21mm [0.83 inches].
Figure 11
Shoe
Pins
(Item 8)
Friction
Facing
(Item 6)
Machine
Screw
(Item 15)
Adjustment Screw
(Item 18)
Block
(Item 21)
Shoe
Pins
(Item 8)
Jam Nut
(Item 19)
Spacer
(Item 32)
Jam Nut
(Item 31)
Jam Nut
(Item 19)
Friction Facing
Shoe Assembly
(Items 5, 6, and 15)
PARTS REPLACEMENT
FRICTION FACINGS
4. Remove the Shoe Pins (Item 8) (See Figure 11).
5. Remove the Friction Facing Shoe Assembly (Items 5,
6, and 15) (See Figure 11).
Note
The Machine Screws are assembled with an anaerobic
locking compound. Inserting a properly fitting
screwdriver into the head of the Machine Screw and
striking the screwdriver with a hammer will break the
crystalline structure of this locking compound and
allow removal of the Machine Screws. Never use an
impact wrench to remove the Machine Screws.
6. Remove the old Machine Screws (Item 15) and old
Friction Facings (Item 6).
7. Using new Machine Screws (Item 15), install new
Friction Facings (Item 6) (See Figure 11).
8. Tighten the new Machine Screws (Item 15) to 12-16
Nm [8-11 ft-lb] torque.
9. Reinstall the Friction Facing Shoe Assembly (Items 5,
6, and 15) and Shoe Pins (Item 8).
10. Perform Friction Facing clearance adjustment (See
FRICTION FACING ADJUSTMENT).
Note
When replacing Friction Facings, inspect the Friction Disc for scoring or grooves. If necessary, the Rotor may
be turned. A maximum of 0.76 mm [0.030 inches] may be removed from each side of the Friction Disc before
it is necessary to replace the Friction Disc.
Two-port actuator shown.
TABLE 3
M
E
T
I
.
o
N
N
O
I
T
P
I
R
C
S
E
D
E
U
Q
R
O
T
]
b
l-
t
f
[
m
N
5
1
)
g
n
i
c
a
F
n
o
it
c
ir
F
(
w
e
r
c
S
e
n
i
h
c
a
M
]
1
1
-
8
[
6
1
-
2
1
7
1
)
g
n
it
n
u
o
M
e
m
a
r
F
(
w
e
r
c
S
p
a
C
[192]
260
9
1
)
w
e
r
c
S
t
n
e
m
t
s
u
j
d
A
(
t
u
N
m
a
J
]
0
2
-
5
1
[
7
2
-
3
.
0
2
4
2
)
e
t
a
l
P
g
n
i
n
i
a
t
e
R
(
w
e
r
c
S
p
a
C
]
3
3
-
5
2
[
4
4
-
4
3
1
3
)
r
e
c
a
p
S
(
t
u
N
m
a
J
]
0
2
-
5
1
[
7
2
-
3
.
0
2
3
3
)
r
o
t
a
u
t
c
A
(
s
w
e
r
c
S
p
a
C
]
5
5
-
2
4
[
8
.
4
7
-
2
.
7
5
-
t
u
N
&
tl
o
B
,
g
n
i
R
p
m
a
l
C
r
o
t
a
u
t
c
A
]
5
3
-
5
2
[
3
.
7
4
-
7
.
3
3
-
)
ti
n
U
d
e
g
a
g
n
E
-
g
n
ir
p
S
(
tl
o
B
p
a
T
]
5
1
-
0
1
[
2
.
0
2
-
5
.
3
1
GENERAL
1. Adhere to the following bolt tightening torques (See
Table 3).
2. Inspect Actuator exterior. Replace the Actuator if it is
damaged.
3. Check tightness of all air line connections, and condition
of all air lines. Replace worn of damaged air lines.
4. Inspect Friction Facings for wear. Replace if it is worn
to approximately 7.93 mm [5/16 inch] thick.
5. Lubricate items requiring lubrication (See
LUBRICATION).