Installation – Nexen QFB-2500 964086 User Manual
Page 5
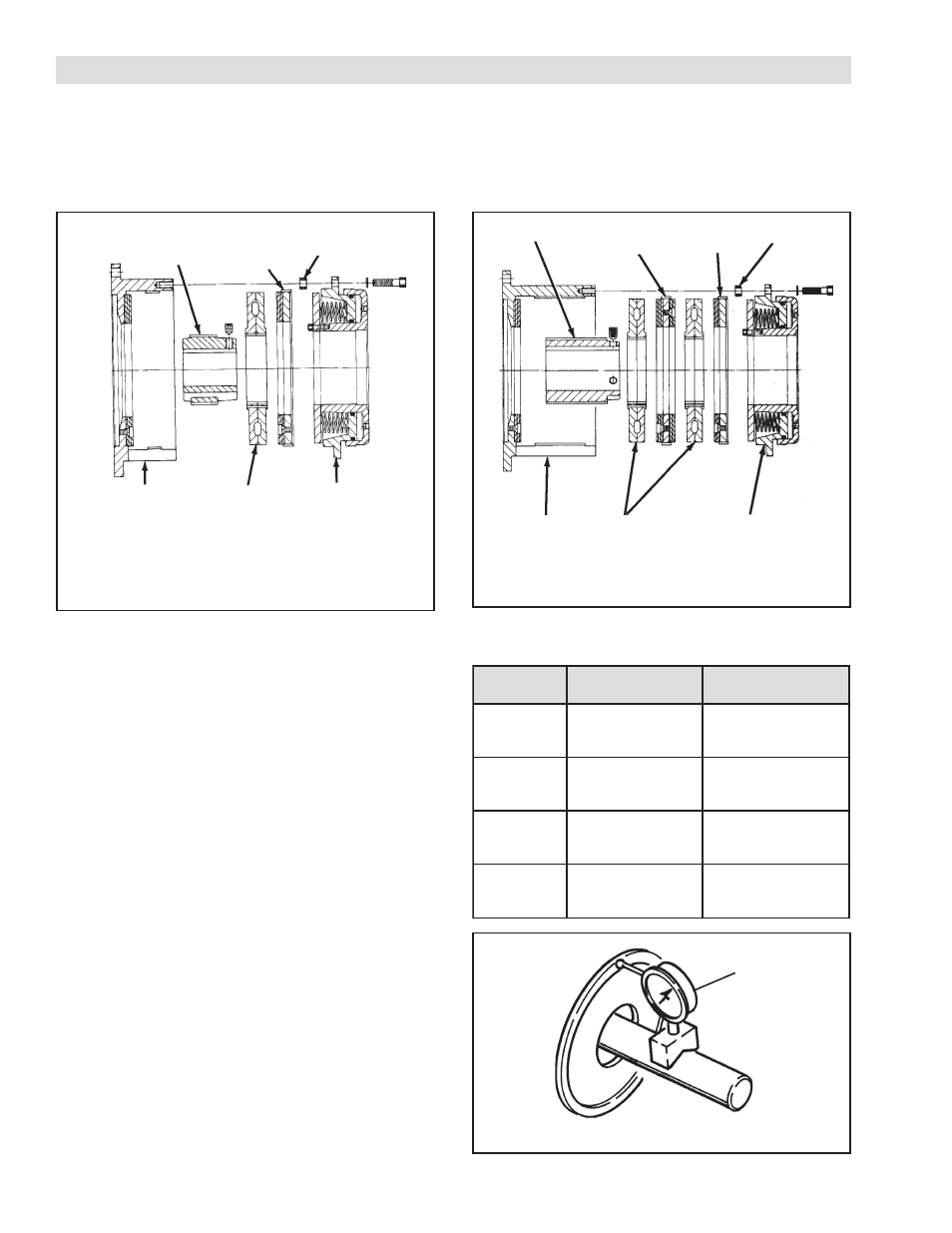
FORM NO. L-20117-F-0210
5
L
E
D
O
M
R
E
T
E
M
A
I
D
T
O
L
I
P
E
L
C
R
I
C
T
L
O
B
0
5
1
1
-
B
F
D
0
5
1
1
-
B
F
Q
.
n
I
5
7
3
.
1
1
]
m
m
9
.
8
8
2
[
.
n
I
0
5
7
.
4
1
n
o
6
]
m
m
7
.
4
7
3
[
0
5
6
1
-
B
F
D
0
5
6
1
-
B
F
Q
.
n
I
0
5
2
.
6
1
]
m
m
8
.
8
1
4
[
.
n
I
0
0
0
.
0
2
n
o
2
1
]
m
m
0
.
8
0
5
[
0
0
2
2
-
B
F
D
0
0
2
2
-
B
F
Q
.
n
I
5
7
3
.
1
2
]
m
m
9
.
2
4
5
[
.
n
I
0
0
5
.
5
2
n
o
2
1
]
m
m
7
.
7
4
6
[
0
0
5
2
-
B
F
D
0
0
5
2
-
B
F
Q
.
n
I
5
7
3
.
4
2
]
m
m
1
.
9
1
6
[
.
n
I
0
5
7
.
8
2
n
o
2
1
]
m
m
3
.
0
3
7
[
INSTALLATION
NOTE: Nexen’s spring engaged, air disengaged Dual Faced Brakes (DFB) and Quad Faced Brakes (QFB) are designed
for horizontal shaft mounting only.
Nexen’s DFB and QFB elements are partially assembled at the factory. Before installation, separate the elements
into subassemblies as shown (See Figures 1 and 2).
Hub
Friction Plate
Assembly
Friction Plate
Assembly
Shims
Housing/Facing
Assembly
Disc
Assembly
FIGURE 2
QFB
Cylinder, Piston/
Pressure Plate
Assembly
Friction Plate
Assembly
Hub
Housing/Facing
Assembly
Disc
Assembly
Cylinder, Piston/
Pressure Plate
Assembly
Shims
FIGURE 1
DFB
1. Provide a piloting flange and 5/8-11 tapped holes in
the bearing supported device or machine component
prior to installing the housing (See Table 1 for Pilot
Diameter and Bolt Circle).
2. Attach the Housing/Facing Assembly to the bearing
supported device or machine frame using customer
supplied Grade 8, 5/8-11 Socket Head Cap Screws.
NOTE: Control perpendicularity between the shaft and
housing mounting surface. Use a Dial Indicator
for measurements. Perpendicularity should be
less than 0.015 TIR (See Figure 3).
3. Apply Loctite
®
242 to the threads and tighten 5/8-11
Socket Head Cap Screws to recommended torque
(See Table 2).
4. Install customer supplied key into shaft.
5. Lubricate Hub splines (Item 1) with Never-Seez
®
or an
equivalent high temperature, anti-seize lubricant.
6. Slide Hub (Item 1) over key and onto shaft (See Figures
1 and 2).
TABLE 1
FIGURE 3
Dial Indicator
- QFB-1150 964080 QFB-2500 964087 QFB-1150 964081 QFB-1150 964167 DFB-1650 964074 DFB-1650 964305 DFB-1650 964075 DFB-1650 964301 DFB-2200 964076 QFB-1650 964082 QFB-1650 964219 DFB-2200 964077 QFB-1650 964083 QFB-1650 964272 DFB-2500 964078 DFB-1150 964072 QFB-2200 964084 DFB-1150 964073 DFB-1150 964045 DFB-1150 964270 DFB-1150 964169 DFB-2500 964079 QFB-2200 964085 QFB-2200 964286 DFB-1150 964017 QFB-1150 964017 DFB-1650 964020 QFB-1650 964020 DFB-2200 964023 QFB-2200 964023 DFB-2500 964026 QFB-2500 964026