Maintenance, General maintenance notes, Periodic pressure tests – Parr Instrument Series 5500 User Manual
Page 14: Compact mini bench top reactors
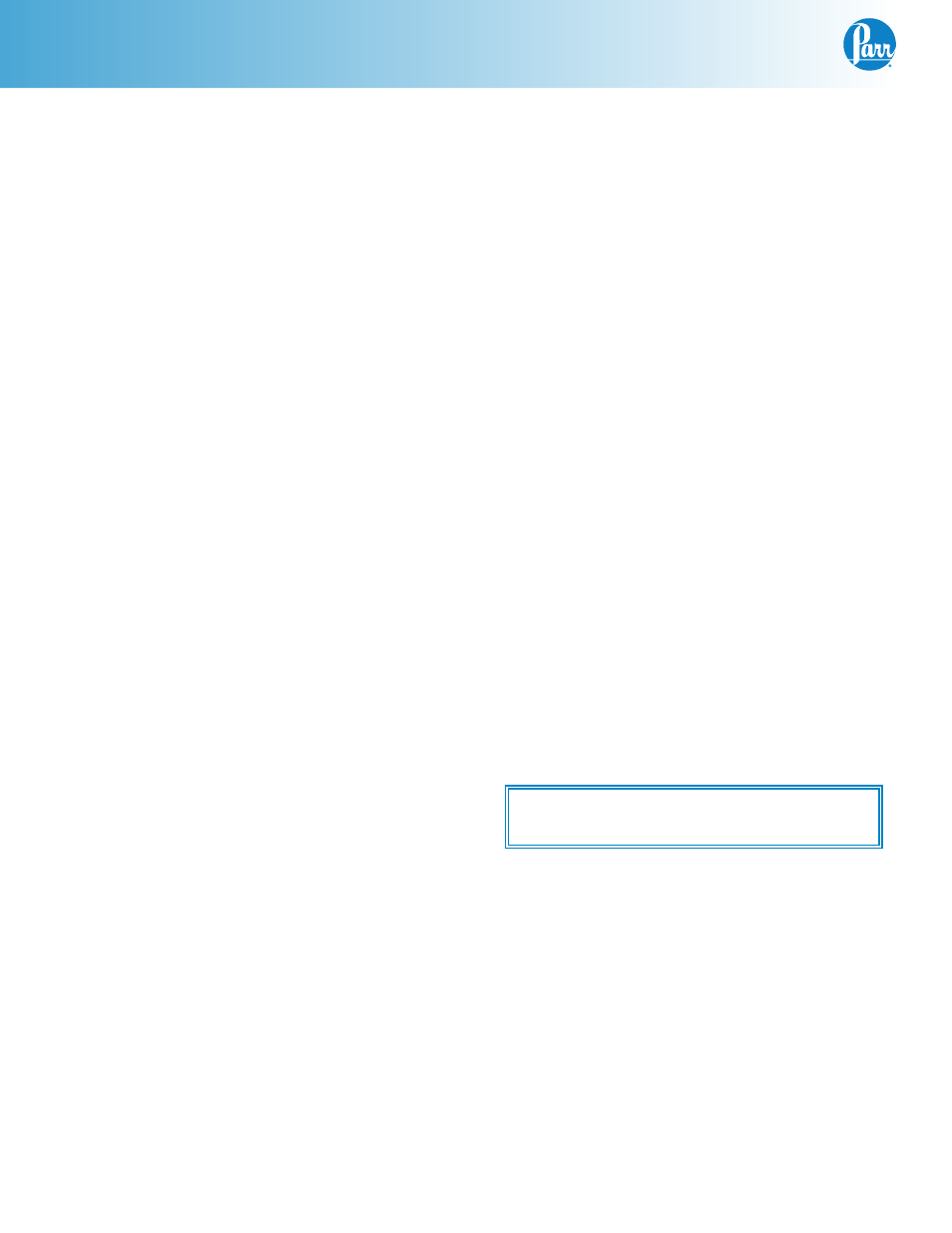
Compact Mini Bench Top Reactors
P a r r I n s t r u m e n t C o m p a n y
14
MAINTENANCE
General Maintenance Notes
1. Periodically inspect all electrical wiring and pres-
sure connections for excessive corrosion. Sus-
pect parts should be replaced by components
only supplied by Parr Instrument Company.
2. Always use appropriate wrenches on all fittings
and valves. Never use pliers or pipe wrenches.
3. Head and cylinder service fixtures are available
for convenience and protection of components
during maintenance of your reactor.
4. NPT (National Pipe Taper) threads should not be
disassembled any more than necessary. It will be-
come increasingly difficult to maintain a tight seal
with these tapered threads if the joint is made and
broken repeatedly. Grafoil tape or PTFE tape (if
temp allows) should be used on all NPT threads.
5. Do not use oil or anti-seize lubricant on threads
or fittings if the vessel is to be used with oxygen.
6. If your vessel is equipped with a loose compres-
sion ring be sure that it is in place on the head
before attaching any head fittings. The compres-
sion ring cannot be installed after fittings have
been screwed into the head.
7. Clean all threads and gas passages thoroughly
and remove all tape fragments when overhaul-
ing a vessel.
An ultrasonic bath is excellent for cleaning metal
parts, but do not place a thermocouple probe,
pressure gage, face seals or ball bearings in
an ultrasonic bath. Periodic cleaning may be
performed on the exterior surfaces of the reactor
stand with a lightly dampened cloth containing
mild soap solution. All electrical power should
be disconnected when cleaning.
8. Routinely inspect cap screws on split ring clo-
sure for lubrication and cleanliness. These
screws should not be allowed to dry because
the threads will seize. Regularly apply Parr
High Temperature Anti-Seize Lubricant (Parr No.
424HC2) before this happens.
9. If servicing assistance is needed, contact Parr
Instrument Company directly at the address
shown on the back of these instructions.
Periodic Pressure Tests
Each cylinder used in a Parr stirred reactor is tested
under hydrostatic pressure to the higher of 1.43
times the rated working pressure at room tem-
perature or 1.30 times the rated working pressure
corrected for temperature before it is released from
the factory. Micrometer caliper measurements are
taken during this test to check the deflection of the
walls under pressure. Excessive deflection or failure
of the metal to resume its original dimensions after
pressure is released indicates that a cylinder is po-
tentially unsafe and it will be rejected. Similar tests
should be made at regular intervals during the life
of each cylinder, and particularly whenever the user
suspects that the equipment has been over-stressed
or damaged.
Some laboratories maintain hydraulic test facilities
and make it a rule that all pressure vessels must
be tested at regular intervals. Records are kept of
deflections at specific test pressures so that any
increase in deflection becomes a warning that the
metal has lost strength. Any cylinder that fails to
return to its original dimensions after application of
the prescribed hydrostatic test should be discarded
as unsafe for further use.
Users who do not have pressure test facilities can
return any Parr pressure vessel to the factory for hy-
drostatic testing and overhaul. This should be done
whenever the metal shows excessive damage from
corrosion or whenever an over-pressure or other
unusual occurrence raises any safety questions.
To return a vessel for repair, contact Parr Instrument
Company for a return authorization number (RMA).
Apparatus returned for testing and overhaul should
be shipped prepaid to the following address:
Ship repair to:
Parr Instrument Company
Attn: Service Department
RMA # XXXXXX
211 53rd Street
Moline, Illinois 61265
An order or letter of instructions should be mailed to
the same address, as no repair work will be started
without specific instructions and a Health & Safety
Assurance Certification form (FX004) signed by a
responsible user.