6 commissioning – Glow-worm Micron 50FF User Manual
Page 18
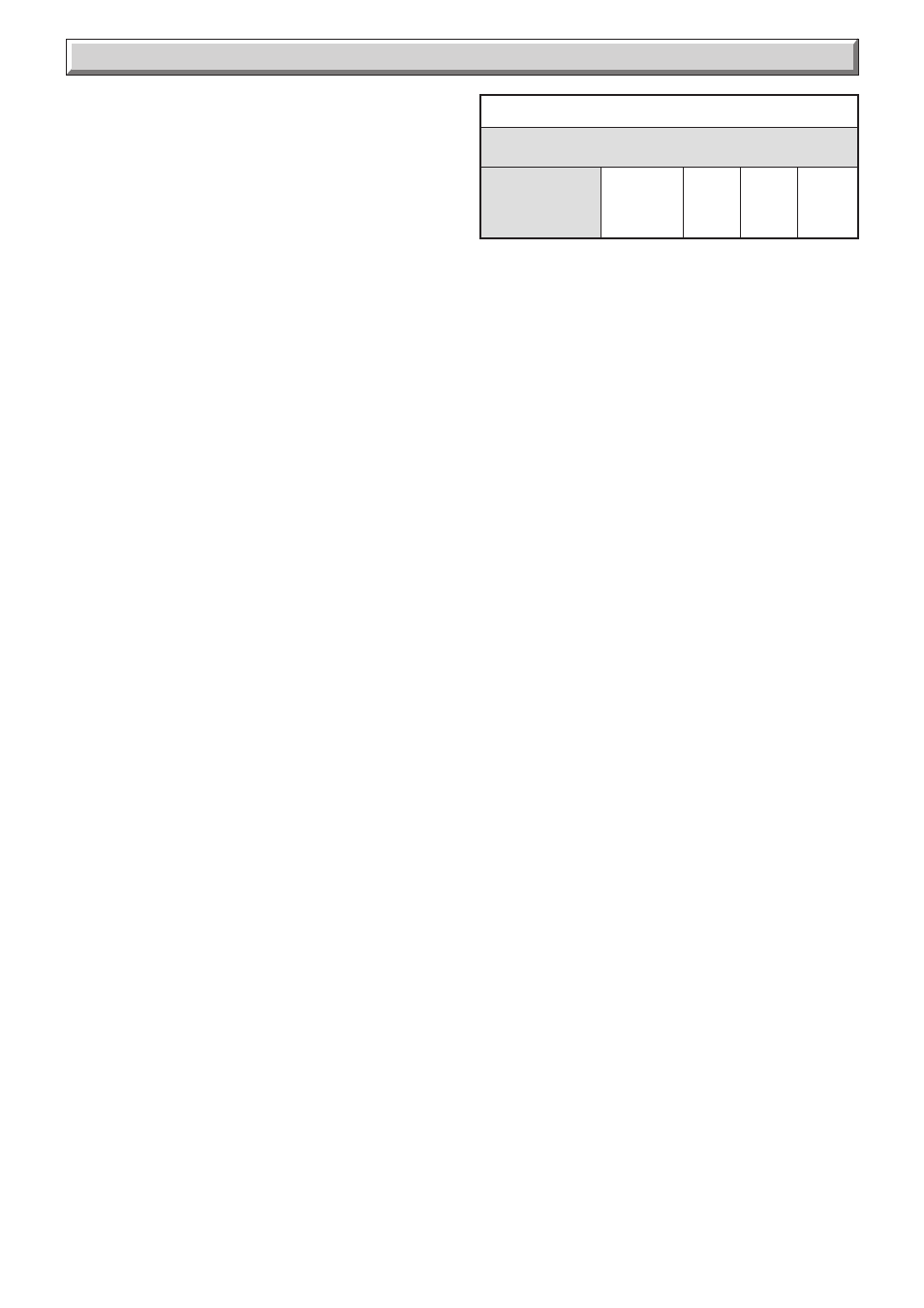
18
2000225227C
6 Commissioning
6.4 Testing - Electrical
Turn the boiler temperature control knob fully clockwise to the
maximum setting, which is approx. 82
O
C (180
O
F).
The lighting sequence is automatic as follows:
The fan will operate for 10 seconds prior to the start of the
ignition sparks, the gas valve solenoids will open and the burner
will light. This is shown by the "Burner Lit" LED on the control
panel lighting up.
The burner will stay alight until switched off, either by the
temperature control or remote system control. At this point the
fan will overrun by 5 seconds.
To make sure that the flame supervision device is working
correctly the following should be done.
With the burner alight, turn the gas service cock "OFF", see
diagram 6.2.
After a short period the burner will go out but the fan will overrun
for 5 seconds.
The correct working of the flame supervision device is shown by
the "Burner Lit" LED going out and the lighting sequence
starting up, as follows:
1. Fan starts.
2. Spark ignition operates for 10 seconds.
3. Fan will overrun for 5 seconds.
4. The fan will start again.
5. After 10 seconds the spark ignition operates, this continues
for a further 10 seconds.
6. Fan will overrun for 5 seconds.
This sequence is repeated ONCE more and the boiler will shut
down. The following illumination will happen with the LED on
the front of the control panel, "Reset" permanently ON and
"Burner Lit" flashing fast (8 Hz).
If the above lighting sequence fails, refer to section 9 - Fault
Finding.
To continue, turn the gas service cock "On", see diagram 6.2.
To restart the lighting sequence, turn the temperature control
knob to "O" then fully clockwise to "Max".
During Normal Operation when the boiler switches "Off", the
burner will go out. The automatic lighting sequence will work
again when heat is required.
6.5 Testing - Gas
With the boiler on proceed as follows:
Undo the screw which secures control box, see diagram 5.10,
Open control box, see diagram 5.10.
WARNING: The multifunctional control and fan operate on
mains voltage, terminals will be live.
Test for gas soundness around the boiler gas components
using a suitable leak detection fluid, in accordance with the
current issue of BS6891.
Check the burner gas pressure at least 10 minutes after the
boiler has lit, refer to Data Label.
If necessary, remove cap and adjust the gas pressure to obtain
the required setting turning screw clockwise, to decrease
pressure, see diagram 6.2.
Replace cap.
Should any doubt exist about the gas rate, check it using the gas
meter test dial and stop watch, at least 10 minutes after the
burner has lit, making sure that all other gas burning appliances
and pilot lights are off.
The gas rates shown in Table 2 are for guidance only, dependent
on the heat setting.
Turn the temperature control knob fully anticlockwise to “0”.
Isolate from electrical supply.
Remove the pressure gauge from the test point and refit screw,
making sure a gas tight seal is made.
Refit control box and fascia.
Note: The fixing holes of the fascia are slotted to allow fine
adjustment, to align control cover with casing.
When the temperature control is turned to the “0” position, by
hand, wait at least 30 seconds before turning On again.
There may be an initial smell given off from the boiler when new,
this is quite normal and it will disappear after a short period of
time.
6.6 Testing - All Water Systems
Allow the system to reach maximum working temperature and
examine for water leaks.
There should be no undue noise in the system.
The boiler should then be turned off and the system drained off
as rapidly as possible, whilst still hot.
Refill the system.
6.7 Open Vented System
Ensure there is no pumping over of water or entry of air at the
open vent above the feed and expansion cistern.
6.8 Adjustment - Fully Pumped Open Vented
and Sealed Water Systems
When commissioning the system the boiler should first be fired
on full service, that is, central heating and domestic hot water.
Adjust the pump to the system design setting then balance the
system, making adjustments as necessary.
6.9 Thermostatic Radiator Valves
If thermostatic radiator valves are fitted care must be taken to
ensure that there is an adequate flow rate through the boiler
when they close, refer to the current issue of BS7478 for
guidance. If fitted to all radiators ensure a bypass is fitted and
adjust to achieve a temperature difference no greater than 20
o
C
between flow and return with the thermostatic valves closed.
6.10 Completion
Adjust the boiler temperature control and any system controls to
their required settings. In addition it is necessary to complete the
"Benchmark" logbook.
For IE, it is necessary to complete a "Declaration of Conformity"
to indicate compliance to I.S.813. An example of this is given in
the current edition of I.S.813.
Testing Flue Gases: If any doubt exists that the flue products
are not exhausting correctly, investigate by use of a gas analyser
(FGA).
50FF
MIN.
MED. MAX.
APPROX.
m3/h
1.35
1.51
1.66
GAS RATE
ft3/h
47.78 53.18 58.44
Table 2