I. locating and mounting unit, A. mounting base, B. clearances – Bryant 452W User Manual
Page 4: Ii. connecting chilled-water lines, Table i, A. materials, B. pipe length and diameter, C. insulation, D. height of coil above absorption unit
Attention! The text in this document has been recognized automatically. To view the original document, you can use the "Original mode".
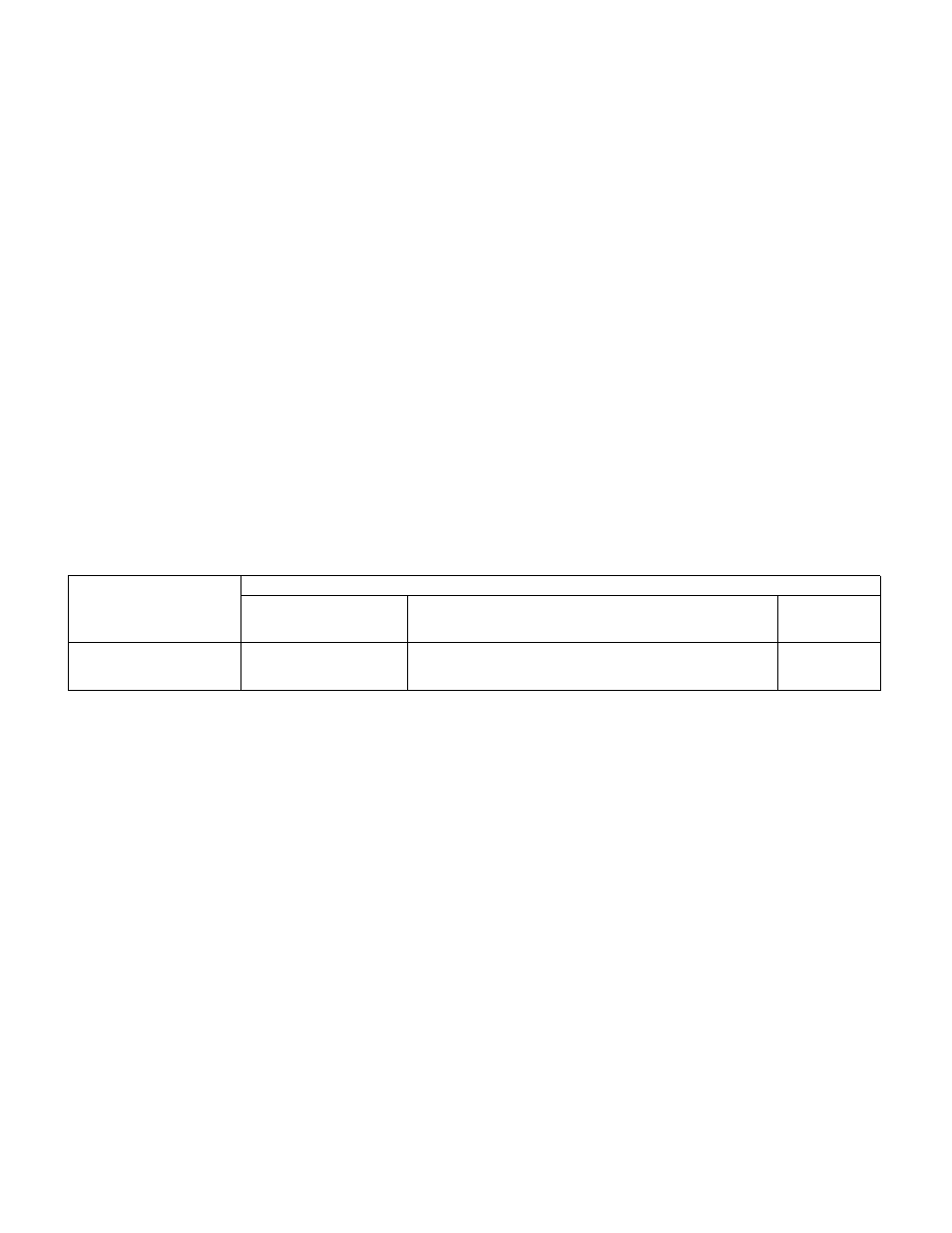
I. LOCATING AND MOUNTING UNIT
The absorption unit is approved for outdoor in
stallation only and may be located at ground level or
on the roof. Consult local or other applicable codes for
information concerning proximity to property lines,
height above roof, obstructions, etc.
A. Mounting Base
1. USE NONCOMBUSTIBLE MATERIALS.
2. Suggested types of mounting base for ground in
stallation ;
a. Precast concrete lintels. Use three lintels the
depth of unit, one each under right and left
end of unit, and one at center of unit.
b. Concrete blocks. Use one block at each corner
of unit plus blocks under the two long sides
midway between the corner blocks.
c. Concrete slab. Minimum thickness 4 inches.
3. Leave sufficient clearance (6 inches minimum)
between unit base and roof for proper air cir
culation when installing unit on a roof. Use
precast concrete lintels or concrete blocks as
described in paragraph 2, or use steel beams.
Check local codes. Refer to NBFU code for In
stallation of Heat Producing Appliances.
B. Clearances
1. Absorption unit should have a minimum clear
ance of 2 feet on all sides from any adjacent
obstruction.
2. Avoid locating the unit where hot condenser air
can impinge on nearby obstructions and mix with
the inlet air supply. The condenser air discharges
upward. The unit should be located outside of
the plumb line from any overhang when the
distance from the overhang to the top of the unit
is less than 7 feet.
II. CONNECTING CHILLED-WATER LINES
1
Refer to “Multiple Chillers and Cooling Coils,” page 1; “Operation at Atmospheric Pressure,” page 1; and
“Chilled-Water System”, page 7, before making any chilled-water connections.
TABLE I
Nominal
Pipe Size
(Inches)
^Allowable Distance Between Coil & Chiller
Polyethylene
Pipe
(Feet)
Copper
Pipe
(Feet)
Galvanized
Pipe
(Feet)
1
30
51
54
1-1/4
205
165
220
1-1/2
490
388
492
NOTE; Values shown in Table I are for one direction only. The total length of pipe from chiller to coil and return would be double the values given.
The above table applies to single unit installations only.
A. Materials
NOTE: Black iron pipe must not be used for chilled-
water piping.
1. Piping
a. Polyethylene Plastic Pipe - use medium den
sity flexible pipe whose wall thickness
approximates Schedule 40 pipe (Commercial
Standard CS 255-63). Pipe must be virgin
plastic. Do not use pipe manufactured from
reclaimed plastic.
b. Copper—satisfactory substitute.
c. Galvanized—satisfactory substitute.
2. Fittings
a. Galvanized—use when possible.
b. Brass—satisfactory substitute.
c. Nylon—satisfactory substitute.
B. Pipe Length and Diameter
Table I shows maximxom length of pipe of different
diameters that can be used between the pump
discharge and the coil inlet and still maintain
minimum allowable (design) water flow rate.
1. Multiply table values by two to obtain total
length of pipe from chiller to coil and return.
2. Length is measured along pipe path and
therefore includes vertical distance between
water coil and chiller.
3. Lengths shown in Table I are based on using a
total of eight galvanized wellhead elbows in en
tire water line (chiller to coil and return).
Lengths are predicated on use of a Bryant
matching water coil. For greater distances, use
larger pipe or add a pump. Consult your
Bryant Distributor for additional information.
C. Insulation
1. Insulate supply and return lines separately.
2. Material should be of good quality and be
covered with a good vapor barrier. Armaflex or
equivalent is recommended.
Wall thickness; 1/2 inch.
D. Height of Coil above Absorption Unit
Practical coil elevation is limited only by the at
mospheric pressure supported hydraulic head.
— 4